
확장형 막냉각 홀이 적용된 터빈 블레이드 끝벽 막냉각 효율 측정
Abstract
In this study, the adiabatic film cooling efficiency measurement using pressure-sensitive paint under conditions simulating the actual turbine blade endwall environment was conducted to verify that the optimal fan-shaped film cooling hole developed through the plate film cooling experiment was effective even in an actual turbine environment. Two end wall specimens with the baseline fan-shaped film cooling hole and the optimal fan-shaped film cooling hole were fabricated and compared the adiabatic film cooling efficiency at the endwall surface of the turbine blade. The optimal fan-shaped film cooling hole was able to effectively cool a wider area with the effect of widening the expansion angles in both the forward and lateral directions compared to the baseline fan-shaped film cooling hole. As a result, the turbine blade endwall showed different film cooling efficiency characteristics than that of the flat plate due to the pressure gradient generated by the turbine blades. However, as in the previous study results, the optimal expansion type film cooling hole showed better film cooling efficiency under all conditions, and the difference became larger as the film cooling flow rate increased.
Keywords:
Gas Turbine, Film Cooling, Pressure Sensitive Paint키워드:
가스터빈, 막냉각, 압력감응페인트1. 서 론
가스터빈 엔진은 작동온도가 높아질수록 비출력과 효율이 높아지기 때문에 더욱 고온에서 작동할 수 있도록 기술이 발전돼왔다. 하지만 가스터빈 엔진의 작동온도는 엔진을 구성하는 부품들의 금속 내열한계온도에 제한을 받으므로 작동온도를 무한정 높일 수 없다. 금속의 내열한계온도를 넘어서는 온도에서도 가스터빈 엔진이 작동하기 위해서는 엔진의 부품들이 내열한계온도를 넘어서지 않도록 냉각을 해줘야한다. 일반적으로 알려진 가스터빈 엔진의 고온부에 사용되는 금속인 니켈합금의 경우 내열한계온도는 약 950℃ 수준이다. 최신 가스터빈 엔진의 경우 작동온도는 약 1,600℃로 금속의 내열한계온도를 크게 상회하므로 냉각 없이는 엔진 운용이 불가능하다. 가스터빈 엔진의 부품들 중에서 가장 높은 온도의 연소가스에 노출되는 연소기와 터빈 블레이드에는 다양한 방식의 냉각기법이 개발되어 적용돼 있다.
가스터빈 엔진 냉각기법 중 금속의 온도를 가장 크게 떨어뜨릴 수 있는 방법은 막냉각 기법이다. 막냉각 기법은 고온의 연소가스에 노출되는 엔진 부품의 표면에 다수의 작은 막냉각 홀을 가공하여 홀에서부터 분사되는 냉각공기로 엔진 부품을 냉각하는 방법이다. 이 방식은 간단하면서도 냉각효과가 뛰어나기 때문에 터빈 블레이드와 같이 고온에 노출되는 부품에 적극적으로 사용되고 있다.(1) 하지만 너무 많은 냉각공기가 막냉각으로 쓰이는 경우 가스터빈 엔진의 효율에 악영향을 미치므로 적은 막냉각 유량으로 더 높은 냉각 성능을 갖도록 하는 기술개발이 필요하다.
막냉각 기법은 막냉각 홀에서 분사되어 나오는 냉각공기가 고온의 연소가스와 섞이지 않고 부품 표면에 얼마나 잘 부착되어 흐르는가가 냉각 성능에 큰 영향을 미친다. 막냉각 유동이 표면에 부착되는 정도는 막냉각 홀 형상,(2) 분사방향,(3) 유동조건,(4) 분사비, 밀도비(5) 등 다양한 인자에 영향을 받는다. 그 중에서도 가장 큰 영향을 미치는 것을 막냉각 홀 형상으로, 막냉각 성능 개선을 위해 다양한 형태의 막냉각 홀 형상이 개발돼 사용 중에 있다.(6) 일반적으로 가장 많이 쓰이는 형태는 가공이 수월한 원형 홀이지만 냉각유량이 많은 고분사비 조건에서 성능이 크게 떨어진다. 고성능 엔진에서 더 나은 막냉각 성능을 위해 확장형 막냉각 홀을 적용한다. 확장형 막냉각 홀은 출구 형태가 원형이 아니고 마름모꼴 형태로 막냉각 홀 단면적이 확장되기 때문에 원형 홀 대비 더 넓은 면적을 냉각할 수 있고, 홀 출구에서 막냉각 유속이 감소돼 연소가스와의 혼합이 줄어들어 막냉각 성능이 개선된다.(7-9)
확장형 막냉각 홀은 확장각에 따라 막냉각 성능이 달라지므로 최적의 확장각을 찾는 연구가 이뤄졌다.(10) 선행연구에서는 실험계획법을 이용하여 평판에서 최적의 막냉각 성능을 갖는 확장각을 찾아냈다.(11) 해당 연구에서는 평판유동 조건에서 막냉각 성능을 평가하였으나 실제 가스터빈 내에서의 유동은 평판유동과는 거리가 있다. 예로 터빈 블레이드의 경우 블레이드 입구와 출구의 유동각이 100도 이상 회전하므로 유로 내에 큰 압력구배가 발생한다. 이 압력구배로 인해 블레이드 엔드월 모서리에서는 2차 유동 와류가 발달하여 엔드월 표면을 따라 이동한다.(12) 이러한 유동특성으로 인해 터빈 블레이드 엔드월에서의 막냉각 유동은 평판에서의 막냉각 성능과 달라지게 된다.(13)
본 연구에서는 선행연구에서 개발된 최적 확장형 막냉각 홀 형상이 실제 터빈 블레이드 엔드월에서도 개선된 성능을 갖는지 검증하기 위한 실험을 수행하였다.
2. 연구방법
2.1 압력감응페인트
본 연구에서는 막냉각 효율 측정에 압력감응페인트(PSP)를 이용한 물질전달 실험법을 이용하였다. 물질전달 실험법은 열전달 실험법에서 발생하는 전도에 의한 오차를 없앨 수 있기 때문에 막냉각 연구에서 많이 활용되는 방법이다.(14,15)
압력감응페인트는 특장 파장대의 빛을 조사하면 또 다른 파장대의 빛을 발하는 특성이 있는 물질로, 발광시 대기 중의 산소분압에 따라 빛의 세기(Intensity)가 달라진다. 산소를 포함하는 공기를 주유로에 흘려주고, 산소를 포함하지 않는 기체를 냉각유체로 흘려주면 산소분압 분포에 따라 압력감응페인트가 발광하는 세기의 구배가 발생한다. 압력감응페인트는 산소농도가 낮을수록 발광세기가 증가하므로 냉각이 잘 되는 영역이 밝게 빛나게 된다. 이 밝기의 세기를 카메라로 촬영하면 막냉각 효율을 계산할 수 있다. 막냉각 효율 계산에는 아래 식을 사용한다.[14]
(1) |
위 식을 이용하여 압력감응페인트로 막냉각 효율을 계산하기 위해서는 산소분압과 페인트의 발광세기에 대한 상관관계를 정의해야 한다. 이를 위해 대기압에서부터 진공까지 압력조절이 가능한 감압챔버를 만들었으며 여기에 시험리그에 설치된 것과 같은 LED조명(LM2X-DM-400, ISSI)과 CCD카메라(PSP-CCD-M, ISSI)를 설치하여 압력과 온도 변화에 따른 발광세기를 촬영하였다. 그 결과는 Fig. 1에 나타내었다. 본 연구에서 사용한 압력감응페인트는 ISSI사의 Binary FIB PSP로 대기온도 10∼40℃ 범위에서는 온도에 따른 영향은 무시할 만한 수준으로 판단되며, 해당 데이터를 바탕으로 최소자승법(Least-Square Fitting)으로 교정커브 근사모델을 만들어 사용하였다. 막냉각 효율에 대한 불확도 분석결과는 Fig. 2에 나타내었다.(16)
압력감응페인트는 시간에 따라 발광세기(Intensity)가 감소하는 광열화(Photodegradation) 현상이 발생하는데 이를 보정하기 위하여 각 촬영 이미지마다 산소분압이 일정한 영역의 발광세기를 샘플링하여 광열화가 발생한 정도를 계산하여 이미지 전체의 발광세기를 보정하여 사용하였다.
2.2 시험설비 및 시험조건
Fig. 3에는 본 연구에서 사용된 터빈 블레이드 캐스케이드 시험 설비를 나타내었다. 터빈 블레이드 캐스케이드 유로 측 공기 공급은 500마력 압축기를 사용하였으며, 캐스케이드 상류에 벤츄리 유량계를 설치하여 유량을 측정하고 3방밸브로 불필요한 유량은 우회시켜 유량을 조절하였다. 공급되는 유동의 온도와 압력은 터빈 블레이드 캐스케이드 상류의 정체챔버에서 측정하였다.
본 실험에 사용된 터빈 블레이드 형상은 항공용 터보팬 엔진의 고압터빈 블레이드를 모사한 형상이다. 일반적인 터빈 블레이드의 경우 허브와 팁에서의 유동각이 다르기 때문에 뒤틀림이 있는데, 고압터빈 블레이드의 경우 허브에서 팁까지의 길이가 짧아 허브와 팀에서의 유동각 차이가 크지 않다. 때문에 본 연구에서는 허브에서 팁까지 뒤틀림 없이 형상이 일정한 2차원 블레이드를 모사하여 선형 캐스케이드를 제작하였다. 캐스케이드를 구성하는 블레이드는 총 5개이며 양쪽 끝 벽을 블레이드의 압력면과 흡입면으로 모사하여 총 6개의 터빈 블레이드 유로를 모사하였다. CFD를 이용하여 출구 덕트의 유동각을 변경해가며 캐스케이드 주기성을 만족하는 조건을 찾았으며 이를 제작에 반영하였다.
Fig. 4에는 터빈 블레이드 엔드월에서의 막냉각 효율 측정을 위한 설비의 구성을 자세히 나타내고 있다. 압력감응페인트가 도포된 터빈 블레이드 엔드월을 촬영하기 위해 캐스케이드 외부에 총 2개의 LED와 1개의 CCD카메라를 알미늄 프레임에 고정하여 설치하였다. 터빈 블레이드 캐스케이드의 위쪽 벽면은 촬영을 위해 압력감응페인트가 발광하는 빛의 파장대와 LED조명이 내는 빛의 파장대가 모두 투과가 가능한 투명 아크릴을 이용하여 제작하였다.
Fig. 5에는 냉각유동 모사 챔버와 여기에 설치된 터빈 블레이드 엔드월 시편을 나타내었다. 냉각유동 모사 챔버에는 터빈 블레이드 엔드월 시편이 설치되므로 교체 탈착이 가능하도록 제작하였다. 막냉각 유동의 공급은 캐스케이드의 바닥면에 설치된 챔버를 통해서 이뤄진다. 막냉각 유동 모사를 위한 공기공급은 50마력 압축기를 이용하며, 질소공급은 질소봄베와 레귤레이터를 이용하여 공급한다. 공급되는 유량은 코리올리유량계를 이용하여 측정하였으며, 솔레노이드 밸브를 이용하여 유량을 제어하였다.
2.3 터빈 블레이드 엔드월 시편
본 연구에서 사용된 터빈 블레이드 엔드월 시편은 SLA 방식의 3D 프린터를 이용하여 제작하였다. SLA 방식은 액상의 광경화수지를 이용하므로 파우더나 필라멘트를 이용하는 다른 방식의 3D 프린터보다 제작물의 정밀도가 좋기 때문에 높은 정밀도를 요구하는 막냉각 홀 형상 구현에 적합하다.
터빈 블레이드 엔드월 시편에 설치된 막냉각 홀의 배치는 Fig. 6에 나타내었다. 터빈 블레이드의 입구에서 출구까지 유동이 흐르며 선회하기 때문에 위치에 따라 유동각에 맞게 막냉각 홀의 분사각을 달리해야 한다. 이를 위해 우선 터빈 블레이드 유로를 그림에서와 같이 횡방향과 유동방향으로 나누어 좌표계를 만들었으며, 이 좌표계 위에서 터빈 블레이드의 전단에서부터 목(Throat)까지 총 9개의 홀을 유사한 간격을 갖도록 배치하였다. 막냉각 홀의 위치를 Table 1에 나타낸 것과 같이 정의하여 배치하였다.
막냉각 홀의 위치가 정해지면 각 위치에서 가장 가까운 블레이드의 압력면과 흡입면의 유동각을 찾아서 거리에 반비례하게 가중치를 곱한 뒤 평균값을 취하여 막냉각 홀의 분사각으로 정의한다. 여기서 정의된 막냉각 유동의 분사각이 주유동의 유동각과 다를 수 있다. 터빈 블레이드 엔드월에서는 블레이드 모서리에서 발달하는 와류와 압력면과 흡입면 사이의 높은 압력구배에 의해서 복잡한 3차원 유동이 발생하므로 막냉각 유동이 설치된 분사각과 다른 거동을 보일 수 있다. 본 연구의 목적은 막냉각 홀 개선형상에 대한 터빈 유로 내에서의 막냉각 성능 평가로, 막냉각 홀 위치와 분사각에 따른 막냉각 성능 특성은 분석은 다루지 않았다.
2.4 확장형 막냉각 홀 형상
본 실험에서 사용한 막냉각 홀의 형상은 Fig. 7에 나타내었다. 확장형 막냉각 홀 중에서 가장 잘 알려진 형상은 모든 방향으로 확장각 7도를 갖는 7-7-7 홀[2]로, 해당 형상을 기준으로 선형연구를 통해 개발된 최적 확장형 막냉각 홀 성능을 비교하였다. 두 막냉각 홀 형상의 홀 직경(D), 홀 길이(L), 전방분사각(α)은 공통으로 같다. 차이점은 전방확장각(βfwd), 횡방향확장각(βlat), 홀 길이비(Lfwd/Lm) 로 전체적으로 확장비(AR)가 커지면서 막냉각 홀의 표면적이 넓어졌다. 막냉각 홀 형상에 대한 구체적인 수치는 Table 2에 나타내었다.
2.5 시험조건
Table 3에는 본 연구에서 수행한 시험조건을 요약하여 나타내었다. 압축기를 통해 공급되는 전체 유량은 약 1.7 kg/s로 터빈 블레이드 유로 수로 나누면 유로 당 공급유량은 약 283.3 g/s로 이를 터빈 블레이드 코드길이(C) 기준 레이놀즈 수로 환산하면 입구기준 약 400,000, 출구기준 약 570,000이다. 이는 완전 난류유동으로 가정할 수 있으며 실제 항공용 엔진 내 레이놀즈 수와 유사한 수준이다.
냉각공기 유량은 주 유량대비 0.25∼1.25% 범위에서 변경해가며 시험을 수행하였다. 터빈 블레이드 유로 내에서도 위치에 따라 유속과 압력이 달라지기 때문에 막냉각 홀이 형상과 공급압력이 같더라도 막냉각 홀 위치에 따라 분사되는 유량이 다르다. 보통 압력이 높은 터빈 블레이드의 상류에서는 막냉각 유량이 적게 분사가 되고, 유동이 가속되어 압력이 낮아지는 하류에서는 막냉각 유량이 많이 분사된다. 그리고 터빈 블레이드의 압력면이 흡입면보다 압력이 높기 때문에 압력면에 가까울수록 냉각 유량이 적게 분사된다. 본 시험에서는 각 막냉각 홀마다 유량계를 달아 유량을 측정할 수 없었으므로 막냉각으로 공급된 총 유량을 기반으로 터빈 블레이드 엔드월 전체의 평균 막냉각 분사비를 계산하여 표에 제시하였다.
Fig. 8 에는 터빈 블레이드 전단부(Leading edge)에서부터 0.2C 상류에서 측정한 입구유동의 경계층 프로파일을 나타내었다. 터빈 블레이드 캐스케이드 입구기준 레이놀즈 수는 약 400,000으로 완전 난류유동으로 가정할 수 있으며 경계층 또한 난류경계층 유동을 따른다고 가정할 수 있다. 측정결과 경계층 두께는 블레이드 높이(H)의 약 0.3배이며, 막냉각 홀 직경(D)의 17.5배이다.
3. 연구결과
3.1 터빈 블레이드 엔드월 유동 특성
막냉각 홀 형상에 따른 막냉각 효율을 설명하기 앞서, 터빈 블레이드 유로 내에서의 유동 특성에 대한 이해가 필요하다. 막냉각 유동의 거동은 주유동에 영향을 많이 받는데, 터빈 블레이드 엔드월에서는 일반 평판에서와는 다른 독특한 유동 특성이 있기 때문에 막냉각 유동 또한 평판에서와는 다른 특성을 보인다.
터빈 블레이드 엔드월에서의 첫 번째 유동 특성은 유체가 블레이드를 따라 선회하며 만드는 압력구배이다. 압력구배에 따라 블레이드의 볼록한 면을 흡입면, 오목한 면을 압력면이라 부른다. 유체는 터빈 블레이드 유로를 흐르며 압력이 높은 압력면에서 압력이 낮은 흡입면으로 방향으로 힘을 받게 된다.
두 번째는 터빈 블레이드 상류에서 하류로 유동이 흐르면서 가속이 되는 현상이다. 일반적으로 터빈 블레이드는 유로가 좁아지며 유동을 가속시키는 역할을 한다. 때문에 블레이드 하류로 이동하며 유체의 속도는 점점 높아지고, 압력은 유속과 반대로 점점 낮아진다. 터빈 블레이드의 목(Throat)에서 속도는 최대가 되고 압력은 최저가 된다.
세 번째는 터빈 블레이드와 엔드월이 만나는 모서리에서 발달하는 와류이다. 터빈 블레이드의 전단부에서는 입구 유동의 경계층의 압력구배에 의해 말발굽 와류가 발생한다. 이 와류는 터빈 블레이드의 압력구배에 따라 압력면에서 흡입면 방향으로 엔드월 중앙을 가로질러 이동한다. 이 와류는 압력면에 도달하면 블레이드 흡입면을 따라 리프트 되어 블레이드 하류로 빠져나간다.
위와 같은 특성은 막내각 홀 형상에 관계없이 터빈 블레이드 유로에서 공통적으로 나타나는 특성이며, 이에 대한 이해를 바탕으로 본 연구에서 측정된 막냉각 효율 결과를 분석하였다.
3.2 터빈 블레이드 엔드월 막냉각 특성
본 연구에서는 막냉각 유량을 주유로 입구 유량 대비 0.25∼1.25% 범위에서 0.25% 단위로 변경해가며 터빈 블레이드 엔드월에서의 단열 막냉각 효율 측정시험을 수행하였고 각 유량별 측정결과를 제시하였다.
위에서 설명한 터빈 블레이드 엔드월에서의 유동 특성이 막냉각에 미치는 영향을 분석하였다. 터빈 블레이드 유동장은 막냉각 유량, 홀 형상에 관계없이 공통 현상으로 나타내므로 모든 케이스에서 관찰 가능하다.
터빈 블레이드 유로 내에는 블레이드 압력면에서부터 흡입면까지 압력이 낮아지는 압력구배가 존재한다. 이 압력구배에 의해 엔드월에서 분사된 막냉각 유체는 터빈 블레이드 유로를 따라 흐르며 압력면에서 흡입면 쪽으로 밀려나게 된다. 이러한 현상은 그림에서 막냉각 효율의 궤적을 통해 확인할 수 있으며, 이로 인해 두 막냉각 형상 공통적으로 흡입면에 가까운 영역에서 전반적인 막냉각 효율이 높게 나타나다. 터빈 블레이드 엔드월과 흡입면이 만나는 모서리에 도달한 막냉각 유체는 흡입면을 타고 올라가 블레이드 일부를 냉각하는 효과를 갖는다.
터빈 블레이드는 상류에서 압력이 가장 높고 하류로 갈수록 압력이 점점 낮아진다. 때문에 압력이 높은 상류에 위치한 막냉각 첫 번째 열에서는 충분한 냉각 유체가 분사되기 어려운 환경이다. 특히, 첫 번째 열에서도 압력면에 가장 가까이 위치한 1번 막냉각 홀은 냉각 유체 분사량이 가장 적으며, 막냉각 유량 0.25% 조건에서는 분사량이 미미하여 막냉각 역할을 제대로 못하고 있다. 냉각 유체 공급압을 증가시켜 막냉각 유량이 늘어나면 해당증상은 개선되지만, 모든 시험케이스에서 4번 막냉각 홀은 가장 낮은 막냉각 효율을 보인다. 반면에 주유동의 압력이 가장 낮은 터빈 블레이드의 목에 위치한 막냉각 홀 8번과 9번은 가장 높은 막냉각 효율 보인다.
터빈 블레이드 전단부에서부터 발달한 말발굽 와류는 압력구배에 의해 압력면에서 흡입면으로 이동한다. 이 와류의 경로는 6번, 8번 막냉각 홀에서 분사된 유체의 궤적을 통해서 확인 가능하다. 분사된 막냉각 유동은 와류를 만나게 되면 와류의 코어에 의해서 리프트된다. 때문에 말발굽 와류가 이동하는 경로에 있는 막냉각 홀은 낮은 막냉각 효율을 보이는데 막냉각 홀 6번, 8번을 보면 유사한 막냉각 분사량을 갖는 같은 열의 다른 홀에 비해 막냉각 효율 궤적의 꼬리가 짧고 블레이드 흡입면쪽으로 꺾여 있는 것처럼 보인다. 이러한 현상은 막냉각 유량비가 낮을수록 뚜렷이 보이고, 막냉각 유량비가 높아지면 막냉각 유동의 운동량이 증가하면서 점점 사라진다.
Fig. 9와 Fig. 10에는 각각 기본 확장형 홀과 최적 확장형 홀 형상에 대한 단열 막냉각 효율을 2차원 컨투어로 나타내었다. 해당 그림을 통해서 홀 형상에 따른 특성을 정성적으로 비교 분석하였다.
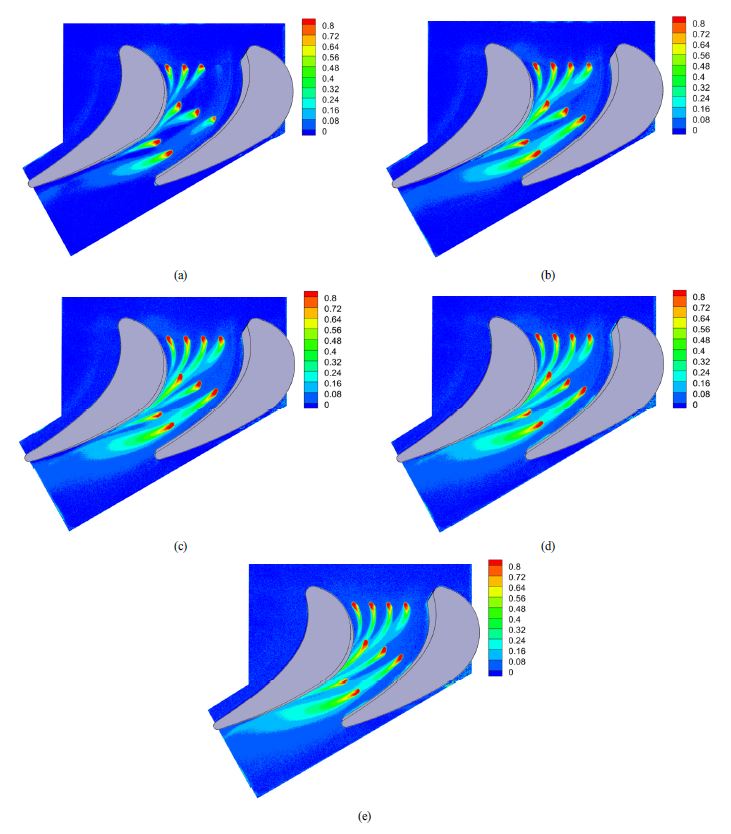
Film cooling effectiveness distribution on turbine blade endwall with baseline fan-shaped film cooling holes; cooling flow ratio of (a) 0.25%, (b) 0.50%, (c) 0.75%, (d) 1.00%, (e) 1.25%
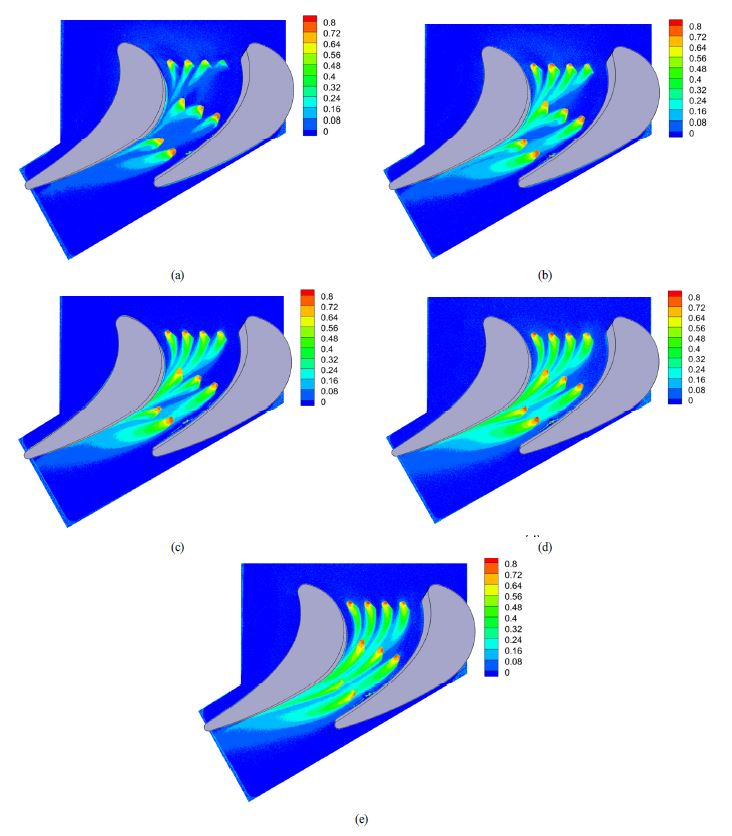
Film cooling effectiveness distribution on turbine blade endwall with optimal fan-shaped film cooling holes; cooling flow ratio of (a) 0.25%, (b) 0.50%, (c) 0.75%, (d) 1.00%, (e) 1.25%
기본 확장형 홀 대비 최적 확장형 홀은 확장각이 커진 만큼 입출구 면적비가 증가하였고, 이로 인해 막냉각 유체의 확산현상이 더욱 두드러진다. 유체는 확산하게 되면 유속이 낮아지며 운동량이 감소하게 된다. 막냉각 유체의 운동량이 감소하면 주유동 유체의 운동량에 의해 휩쓸려나가기 쉬워 막내각 효율의 궤적이 짧게 나타나며, 반대로 막냉각 유체의 운동량이 증가하면 주유동의 영향을 덜 받으며 막내각 효율의 궤적이 길게 나타난다. 이러한 현상으로 인해 기본 확장형 홀 대비 최적 확장형 홀의 막냉각 효율의 궤적이 짧다.
반면에 막냉각 유체의 운동량이 너무 큰 경우 막냉각 유동이 엔드월 표면에 부착되기보다 주유동으로 관통하여 흘러들어가기 때문에 오히려 막냉각 효율이 낮아지는 현상이 나타난다. 막냉각 유량비가 큰 경우 (>1.0%) 기본형 막냉각 홀의 막냉각 효율 궤적이 짧아지는 현상이 나타나면서 상대적으로 최적 확장형 홀의 막냉각 효율의 궤적이 길게 나타난다. 게다가 막냉각 홀의 전방향 황장각이 커지게 되면 막냉각 유체의 전방 분사각이 작아지는 효과가 있으므로 유체가 높은 운동량을 갖고 분사되더라도 표면에 더 잘 부착돼 흐르는 효과가 있다. 결과적으로 막냉각의 유량비가 증가할수록 최적 확장형 막냉각 홀의 막냉각 효율이 전반적으로 높게 나타난다.
이상적인 막냉각 홀은 분사되는 막냉각 유체가 막냉각 홀의 확장면에서 박리되지 않고 표면을 따라 흘러야 한다. 하지만 확장각이 커질수록 유체가 막냉각 홀 표면에서 박리되기 쉬워진다. 터빈 블레이드 엔드월에서는 압력면과 흡입면의 압력구배로 인해 막냉각 홀의 좌우 압력이 다르고 주유동 방향도 막냉각 유체의 분사방향과 완전히 일치하지 않기 때문에 확장형 막냉각 홀의 경우 막냉각 유체가 확장면을 따라흐르기 보다 박리되어 한쪽으로 쏠리기 쉽다. 막냉각 홀 확장면에서 냉각 유체가 박리되는 경우 박리지점에서 생기는 음압에 의해 주유동이 홀 안쪽으로 유입되어 결과적으로 막냉각 효율에 나쁜 영향을 미친다.
최적 확장형 막냉각홀의 경우 횡방향 확장각을 키워 냉각 유체를 좌우로 더 넓게 퍼뜨려 넓은 면적을 냉각하는데 유리하도록 설계되었다. 하지만 넓어진 확장각에 의해 박리되기 쉽고, 이로 인해 주유동과 혼합되는 현상이 발생하여 홀 안쪽에서부터 막냉각 효율이 낮아지는 현상이 발생한다. 기본 확장형 막냉각 홀의 경우 홀 내부에서 박리되는 현상 없거나 발생하더라도 그 효과가 미미하여 최적 확장형 막냉각 홀 대비 홀 내부에서 높은 막냉각 효율을 보인다.
Fig. 11에는 터빈 블레이드 엔드월 표면에서 횡방향 평균 단열 막냉각 효율을 나타내었다. 해당 그림은 Fig. 9과 Fig. 10에 나타낸 2차원 막냉각 효율 컨투어에 Fig 5에 나타낸 좌표계를 정의하고, 압력면과 흡입면을 횡방향으로 연결하는 선 위에서의 단열 막냉각 효율의 평균값을 계산해 축방향으로 나타내었다. 촬영 이미지의 픽셀은 균등간격을 가지므로 단열 막냉각 효율의 평균값은 산술평균을 취하였다.
막냉각 홀 첫 번째 열의 시작지점부터 비교해보면, 최적 확장형 막냉각 홀의 경우 기본 확장형 막냉각 홀 대비 홀 내부에서 막냉각 효율이 낮았으나 넓어진 출구 면적으로 인해 막냉각 유체가 더 넓은 면적을 커버하면서 횡방향 평균값은 기본 확장형 막냉각홀과 유사한 수준을 나타낸다. 막냉각 유체가 하류로 이동하면서 그리는 막냉각 효율 궤적은 기본 확장형 막냉각 홀의 경우가 길었다. 하지만 횡방향으로 넓게 퍼지지 못해 횡방향 평균값을 보면 하류로 갈수록 오히려 최적 확장형 막냉각 홀의 경우가 좋게 나타난다.
유체 분사량이 적은 경우(<0.5%), 국소적으로 최적 확장형 막냉각 홀에서 막냉각 효율이 높게 나타나는 부분 있지만 막냉각 홀 형상에 따른 큰 차이는 보이지 않는다. 유체 분사량이 많아지는 경우(>0.75%), 위에서 설명한 확산에 의한 운동량 감소 효과가 최적 확장형 막냉각 홀에서 두드러지게 나타나면서 하류로 갈수록 막냉각 효율이 전반적으로 높아진다. 게다가 막냉각 유량이 증가할수록 냉각 유체 누적에 의한 냉각 효과 개선이 더욱 뚜렷이 나타난다. 하지만 막냉각유량이 가장 많은 경우(=1.25%), 터빈 블레이드 목 부근에서는 최적 확정형 막냉각 홀도 막냉각 유체의 운동량 증가에 의한 막냉각 효율 감소효과가 관찰된다.
Fig. 12에는 터빈 블레이드 엔드월 전체 표면에서의 단열 막냉각 효율의 평균값을 나타내었다. 횡방향 평균과 마찬가지로 Fig. 5에 나타낸 좌표계를 이용하여 전체면적에서의 단열 막냉각 효율을 산술평균하였다. 면평균 막냉각 효율을 보면 모든 유량대에서 최적 확장형 막냉각 홀의 막냉각 효율이 높음을 알 수 있다. 기본 확장형 막냉각 홀의 경우 막냉각 유량비가 0.50%를 넘어가면 냉각 유량이 증가하더라도 막냉각 효율 개선이 더디지만, 최적 확장형 막냉각 홀은 냉각 효율 개선이 뚜렷이 나타난다.
4. 결 론
본 연구에서는 평판 막냉각 실험을 통해 개발된 최적 확장형 막냉각 홀 형상이 실제 터빈 환경에서도 성능이 유효한지를 검증하기 위해 실제 터빈 블레이드 엔드월 환경을 모사한 조건에서 압력감응페인트를 이용한 단열 막냉각 효율 측정 실험을 수행하였다. 기본 확장형 막냉각 홀과 최적 확장형 막냉각 홀이 각각 설치된 두 가지 엔드월 시편을 만들어 터빈 블레이드 엔드월 표면에서의 단열 막냉각 효율을 비교분석하였다.
평판시험 결과 최적 확장형 막냉각 홀은 기본 확장형 막냉각 홀 대비 전방향, 횡방향 확장각이 모두 넓어진 효과로 더 넓은 면적을 효과적으로 냉각이 가능하였다. 본 연구에서 시험한 결과 터빈 블레이드 엔드월에서는 블레이드에서 발생하는 압력구배에 의해 평판에서와는 다른 막냉각 효율 특성을 보였다. 하지만 선행연구결과와 마찬가지로 모든 조건에서 최적 확장형 막냉각 홀이 더 나은 막냉각 효율을 보였고 막냉각 유량이 많아질수록 그 차이는 더욱 커졌다.
최적 확장형 막냉각 홀은 평판에서 뿐만 아니라 실제 터빈 블레이드 엔드월에서도 냉각 성능 개선이 가능하다는 것을 실험적으로 검증하였으며, 향후 터빈 블레이드에도 적용하여 냉각 성능 개선 가능성을 검증할 예정이다.
Acknowledgments
본 연구는 산업통상자원부 주관 항공우주부품기술 개발사업의 지원(과제번호: 10083654)에 의해 수행되었습니다.
References
-
Goldstein, R. J., “Film Cooling”, Advances in Heat Transfer, Elsevier, pp. 321-379.
[https://doi.org/10.1016/S0065-2717(08)70020-0]
-
Lutum, E. and Johnson, B. V., 1998, “Influence of the Hole Length-to-Diameter Ratio on Film Cooling with Cylindrical Holes,” Journal of Turbomachinery, Vol. 121, No. 2, pp. 209-216.
[https://doi.org/10.1115/1.2841303]
-
Park, S., Jung, E. Y., Kim, S. H., Sohn, H. S. and Cho, H. H., 2016, “Enhancement of Film Cooling Effectiveness Using Backward Injection Holes,” International Journal of Thermal Sciences, Vol. 110, pp. 314-234.
[https://doi.org/10.1016/j.ijthermalsci.2016.08.001]
-
Anderson, J. B., Wilkes, E. K., McClintic, J. W. and Bogard, D. G., 2016, “Effects of Freestream Mach Number, Reynolds Number, and Boundary Layer Thickness on Film Cooling Effectiveness of Shaped Holes,” ASME Turbo Expo, Paper No. GT2016-56152.
[https://doi.org/10.1115/GT2016-56152]
-
L. M. Wright, S. T. McClain and M. D. Clemenson, 2010, “Effect of Density Ratio on Flat Plate Film Cooling with Shaped Holes Using PSP,” Journal of Turbomachinery, Vol. 133, No. 041011.
[https://doi.org/10.1115/1.4002988]
-
Bunker, R. S., 2005, “A Review of Shaped hole Turbine Film-Cooling Technology,” Journal of Heat Transfer, Vol. 126, No. 4, pp. 441-453.
[https://doi.org/10.1115/1.1860562]
-
Gritsch, M., Colban, W., Schar, H. and Dobbeling, K., 2005, “Effect of Hole Geometry on the Thermal Performance of Fan-Shaped Film Cooling Holes,” Journal of Turbomachinery, Vol. 127, No. 4, pp. 718-725.
[https://doi.org/10.1115/1.2019315]
-
Schroeder, R. P., Thole, K. A., 2014, “Adiabatic Effectiveness Measurements for a Baseline Shaped Film Cooling Hole,” Proceedings of ASME Turbo Expo 2014, GT2014-25992.
[https://doi.org/10.1115/GT2014-25992]
- Wang, H. and Wright, L. M., 2021, “Effect of Inlet Geometry on Flat Plate Film Cooling Effectiveness from Shaped Holes,”, Proceedings of ASME International Mechanical Engineering Congress and Exposition 2021, IMECE2021-73135.
-
Lee, K. D. and Kim, K. Y., 2011, “Surrogate Based Optimization of a Laidback Fan-Shaped Hole for Film-Cooling,” Journal of Het and Fluid Flow, Vol. 32, No. 1, pp. 226-238.
[https://doi.org/10.1016/j.ijheatfluidflow.2010.08.007]
-
Seo, H, J., Park, S. H., Kwak, J. S. and Kang, Y. S., 2019, “Experimental and numerical study on the effect of fan-shaped hole configuration on film cooling effectiveness”, Proceedings of ASME Turbo Expo 2019, GT2019-90817.
[https://doi.org/10.1115/GT2019-90817]
-
Chung, H., Hong, C. W., Kim, S. H., Cho, H. H. and Moon, H. K., 2016, “Heat Transfer Measurement Near Endwall Region of First Stage Gas Turbine Nozzle Having Platform Misalignment at Combustor-Turbine Interface,” International Communications in Heat and Mass Transfer, Vol. 78, pp. 101-111.
[https://doi.org/10.1016/j.icheatmasstransfer.2016.08.022]
-
Charbonnier, D., Ott, P., Jonsson, M., Cottier, F., and Kobke, T., 2009, “Experimental and Numerical Study of the Thermal Performance of a Film Cooled Turbine Platform,” Proceedings of ASME Turbo Expo 2009, GT2009-60306.
[https://doi.org/10.1115/GT2009-60306]
-
Han, J. C., Rallabandi, A. P., 2010, “Turbine Blade Film Cooling Using PSP Technique,” Frontiers in Heat and Mass Transfer, 1-013001.
[https://doi.org/10.5098/hmt.v1.1.3001]
-
Rallabandi, A. P., Grizzle, J., and Han, J. C., 2011, “Effect of Upstream Step on Flat Plate Film-Cooling Effectiveness Using PSP,” Journal of Turbomachinery, Vol. 133, No. 4.
[https://doi.org/10.1115/1.4002422]
-
Natsui, G., Little, Z., Kapat, J. S., Dees, J. E. and Laskowski, G., 2016, “A Detailed Uncertainty Analysis of Adiabatic Film Cooling Effectiveness Measurements Using Pressure-Sensitive Paint”, Journal of Turbomachinery, Vol. 138, pp. 1-11.
[https://doi.org/10.1115/1.4032674]