
마이크로 가스터빈 엔진에 적용된 압축기 공력성능 특징
Abstract
A centrifugal compressor is essentially applicable to a micro gas turbine because it can produce a high-pressure ratio over than 3.0 within a limited geometrical allowance. In this paper, aerodynamic design and internal flow characteristics of the centrifugal compressor were described in detail by comparing them with those of turbocharger compressors. Then a centrifugal compressor design procedure with a pressure ratio of 5.0 at the design point for a 1,000 N thrust micro gas turbine has been introduced and the internal flow field at the design point has been further investigated with CFD methods. High impeller pressure ratio led to high absolute Mach number at the impeller outlet, however, small gap between the impeller outlet and diffuser inlet did not sufficiently recover static pressure and it caused large flow separation region and corresponding total pressure at the diffuser hub. For this reason, it requires sophisticated matching between impeller and diffuser stages in micro gas turbines. Based on the internal flow analysis, ideas for further performance improvements have been proposed while maintaining essential compressor performances.
Keywords:
Gas Turbine, Compressor, Impeller, Diffuser, Aerodynamic Design키워드:
가스터빈, 압축기, 임펠러, 디퓨져, 공력설계1. 서 론
일반적으로 1,000N 전후의 추력을 생산하는 터보제트 형태의 가스터빈 엔진을 마이크로 가스터빈 엔진이라고 한다. 마이크로 가스터빈 엔진은 내부구조 및 운용방법이 간단하여, 1990년대부터 본격적으로 개발되어 RC 항공기 등에서 활용되기 시작하였다. 최근에는 터보프롭 혹은 터보샤프트 엔진으로도 파생개발 되어, 소형 무인기 영역까지 활용되는 등 그 활용도가 높아지고 있다. NASA에서는 최대 추력에 따라 Table 1과 같이 가스터빈 클래스를 구분하고 있다.(1,2) 해당 Table에 따르면 본 논문에서 말하는 항공용 마이크로 가스터빈은 Mini에서 Small Class범주에 포함되며, 해당 분류체계에서도 1,000N의 추력은 소형과 중형 엔진을 나누는 기준 추력이다. 코로나 19의 영향에도 불구하고 마이크로 가스터빈의 시장은 2030년까지 꾸준히 성장할 것으로 예상되는데, 이는 마이크로 가스터빈을 적용하는 기체가 대부분 민수용 혹은 군수용 무인기이기 때문이다. 최근에는 마이크로 가스터빈 개조개발에 관련된 연구가 활발히 진행되고 있으며, 이미 일부 마이크로 가스터빈 제작사에서는 배기노즐을 제거하고 동력터빈을 장착한 터보 샤프트 엔진 등을 시판 중이고, 터보팬 혹은 가변노즐 및 애프터버너를 장착한 초음속 엔진 등으로 개조 개발하는 연구사례도 확인되고 있다. 최근에는 마이크로 가스터빈을 전기-하이브리드 항공기의 전력 생산원으로 활용하는 연구도 진행되는 등 마이크로 가스터빈 엔진의 활용영역은 계속해서 넓어지고 있다.
이렇듯 마이크로 가스터빈의 활용도가 높아지면서, 마이크로 가스터빈의 강건성 및 성능이 처음 시장에 소개되었을 때 보다 비약적으로 개선되었다. 마이크로 가스터빈의 활용도가 확대되고 성능도 지속적으로 개선되는데 반해, 최근까지는 마이크로 가스터빈 엔진에 대해 수출입에 대한 별도의 관리가 이루어지지 않았다. 하지만 마이크로 가스터빈 엔진의 출력이 점차 높아지는 방향으로 개발되고 있고, 또한 마이크로 가스터빈 엔진의 군수용 무인기 추진기관으로 무단 전용한 사례 등이 확인되면서, 향후 고성능 마이크로 가스터빈 엔진을 군사전력물자로 분류될 가능성이 높아질 것으로 예측하고 있다. 최근에는 추력 500N을 초과하는 마이크로 가스터빈 엔진을 EU 회원국 이외에 승인 없이 수출하는 것이 금지되었으며, 일례로 독일 Jetcat社는 추력 550N급 엔진인 P550 엔진이 EU 외 국가로 수출이 제한되자 EU 외 국가로 수출하기 위해 P500 엔진을 신규 출시하는 등의 사례도 확인되었다. 마이크로 가스터빈에 대한 관련정책이 최근 빠르게 변화하고 동시에 마이크로 가스터빈에 대한 수요가 전 세계적으로 증가함에 따라 마이크로 가스터빈 공급사도 수십 개社 이상으로 확인되었다. 이에 마이크로 가스터빈 제작사들이 공개한 엔진사양을 정리하여 현재까지 출시된 마이크로 가스터빈 엔진 및 구성품의 성능을 체계적으로 분석한 연구(3), 혹은 마이크로 가스터빈 엔진 구성품 기술동향에 대한 리뷰 논문(4) 등이 발표되기도 하였다. 본 논문에서는 이에 더 나아가 마이크로 가스터빈 구성품 중 엔진 성능 및 안정성에 가장 민감하다고 알려진 원심 압축기 부분에 대한 공력설계 특징을 유사한 크기의 터보차저 압축기 공력설계 특징과 비교하여 분석하고, 1,000N급 마이크로 가스터빈에 적용 가능한 원심압축기 설계 및 수치해석을 통한 성능평가를 통해 마이크로 가스터빈 엔진용 원심압축기 내부 유동장 특성을 파악해 보고자 한다.
2. 마이크로 가스터빈 압축기 특징
2.1 압축기 임펠러 공력설계 특성
추력 수백 N급 상용 마이크로 가스터빈 엔진 압축기는 승용차, 상용차에 장착되는 터보차저 압축기와 크기가 비슷하다. Fig. 1은 유사한 크기의 마이크로 가스터빈 엔진의 압축기 임펠러(출구직경 90mm)와 터보차저 압축기 임펠러(출구직경 94mm) 형상을 비교하고 있다. 두 임펠러는 설계점 성능이 유사하지만, 그림에서 볼 수 있듯이 설계형상이 다른데, 이는 설계 시 고려사항에 몇 가지 큰 차이점이 있기 때문이다.
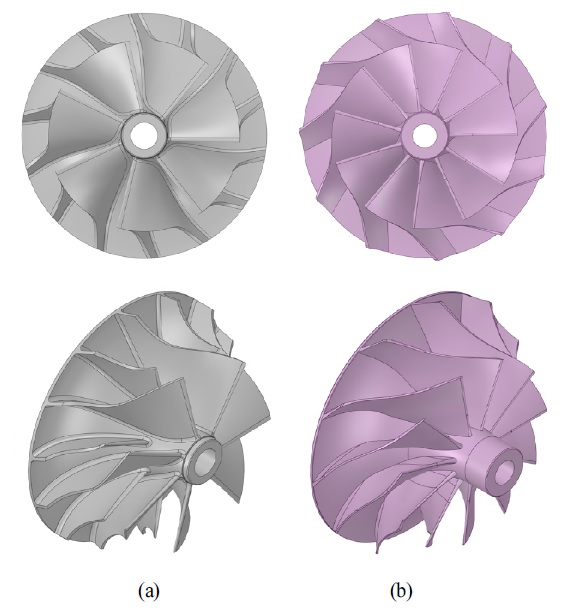
Comparison of impeller modelings: (a) Jetcat P300 MGT impeller, (b) Honeywell GTX4294R turbocharger impeller
공통 사항으로 대부분의 마이크로 가스터빈 엔진, 터보차저에서 압축기 임펠러 앞쪽에 IGV가 장착되지 않기 때문에, 설계점 회전수 근처에서 임펠러 팁 근처 흡입 유체의 상대 마하수가 1 이상이 되는 경우가 많다. 이 때문에 임펠러 전연에서 스톨이 발생할 수 있다. 터보차저에서는 임펠러 전연에서의 충격파에 의한 스톨을 지연시키고자 압력이 상승한 임펠러 내부의 유체를 재순환 시켜 임펠러 전연에 분사시키는 재순환 유로(Bleeding Port 혹은 Ported Shroud)가 설치되어 있는 경우가 많다. 하지만 마이크로 가스터빈 압축기의 경우 공간적인 제약 때문에 이러한 재순환 유로가 설치된 경우가 매우 드물지만, 연구용으로 마이크로 가스터빈 엔진에 재순환 유로가 적용되었을 때에 안정성이 크게 개선된 사례는 보고되어 있다.(5) 또한 엔진 추력 1,000N 이상의 마이크로 가스터빈 혹은 중형 가스터빈 엔진 경계에 있는 일부 가스터빈 엔진에 대해서는 경우 엔진 전연에 재순환 유로가 적용되었다고 보고되어 있다.(6) Circumferential Groove 등이 임펠러 인듀셔 영역에 적용 가능하나, 많은 마이크로 가스터빈 엔진의 경우, 질량 제한조건으로 인해 하우징의 두께가 수mm로 매우 얇게 설계되어 이조차 쉽지 않다. 이에 마이크로 가스터빈 엔진은 임펠러 전연에서 유발되는 유동 불안정성에 의한 스톨발생 위험에 노출된 경우가 많다.
또한 터보차저의 경우 임펠러 출구에서 날개의 후향각(Back Sweep Angle)을 크게 설계하여 압력비를 낮추는 대신, 출구속도 및 마하수를 감소시켜 출구에서의 스톨의 가능성을 낮추고, 출구에서 보다 균일한 유동장을 확보하게 된다.(7) 터보차저 압축기 임펠러에는 후향각을 40° 전후로 설계하는데 반해, 마이크로 가스터빈 임펠러의 경우 작은 엔진에서 가능한 높은 압력비를 얻기 위해 임펠러 출구에서의 후향각은 터보차저 임펠러보다 작게 설계한다. 이 경우 임펠러 출구에서 더 높은 압력비를 얻을 수 있으나, 출구에서의 유동 절대속도 및 마하수가 높아지게 되고, 유동의 균일도는 낮아지게 된다. 이는 하류에 위치한 디퓨져와 단 매칭을 위한 매우 중요한 설계 요소가 된다.
한편 마이크로 가스터빈 혹은 터보차저 압축기 임펠러는 유동이 축방향에서 반경방향으로 방향을 바꾼 후 바로 베인리스 디퓨져 구간으로 유체가 흐른다. 이에 터보차저나 마이크로 가스터빈 압축기 형태는 원심압축기이지만 유동 특성은 사류압축기와 비슷해지는 경향이 있다.(8) 이에 사류압축기의 유동특성을 보완하고자 최근에는 동일한 자오면 형상에서 압축기 성능을 극대화하기 위한 연구가 특히 터보차저 분야에서 다수 진행 중이다. Fig. 2(a)와 2(b)에서와 같이 임펠러 전연을 축류압축기와 유사한 프로파일로 설계하여 압력비를 유지한 채 팁 부근과 50% 스팬에서 날개 부하를 완화하여 스톨마진을 증가시거나(9,10), 혹은 Fig. 2(c)와 같이 임펠러 출구 팁 부근에서 날개를 연장(Extended Trailing Edge)시켜 출구에서 추가로 압력비를 얻을 수 있고 유동의 균일성을 개선하는 커스텀 임펠러 모델이 개발되는 등(11), 터보차저의 수요만큼 매우 다양한 임펠러 성능 개선 연구가 진행되고 있다. 최근에는 마이크로 가스터빈 엔진에서도 유사한 연구가 진행되고 있다. Van der Mewre 등은 터보차저에서와 같이 임펠러 출구에 Extended Trailing Edge 기법을 적용시켜 압축기 효율 및 엔진 성능을 개선한 연구 내용을 발표하였다.(12) Li 등은 Fig. 3에서와 같이 원심압축기에 Tandem 임펠러라는 개념을 적용하여 압축기의 성능개선 및 운용영역을 확장을 시도하는 등(13) 마이크로 가스터빈 엔진에서도 최근 임펠러 성능 향상을 위해 다양한 연구가 진행되고 있다.
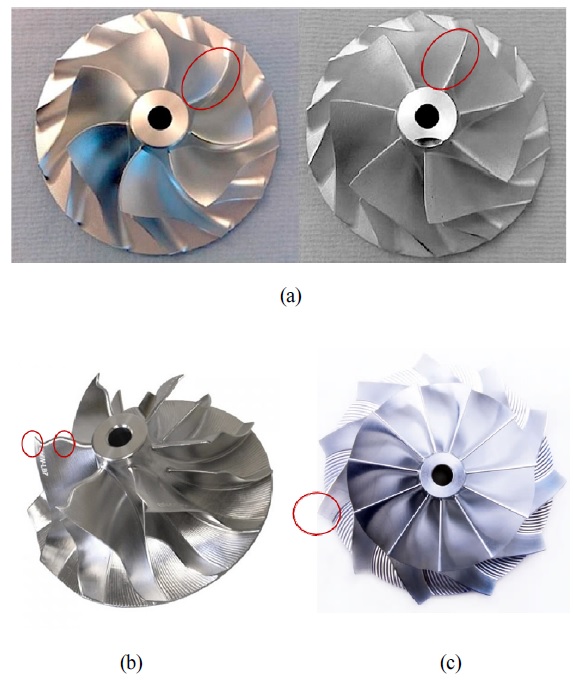
Impeller design revisions:(a) more loading at the mid-span(9), (b) more loading at tip and mid-span(10), (c) extended trailing edge(11)
2.2 압축기 디퓨져 공력설계 특징
터보차저의 경우 보통 베인리스 디퓨져를 적용하여 폭넓은 운용범위에 대응할 수 있으며 압축된 공기는 스크롤을 통해 모아 엔진으로 공급된다. 마이크로 가스터빈의 경우 베인 디퓨져를 사용하여 터보차저보다 한정된 작동영역에서 임펠러 출구의 동압을 정압으로 회복시키고, 또한 스월을 제거하여 압축된 공기를 연소기로 공급한다. 하지만 마이크로 가스터빈 엔진의 경우 제한된 공간 내에서 디퓨져를 설치하여야 하고, 또한 가공성 및 조립성이 함께 고려된 디퓨져 형상이 설계에 반영되어 공력성능이 극대화된 디퓨져가 적용된 사례를 찾기가 힘들다. 실제로 마이크로 가스터빈 내에서 가장 큰 손실이 발생하며 마이크로 가스터빈 엔진의 성능 및 작동영역을 감소시키는 부분이 디퓨져 부분이다.
또한, 마이크로 가스터빈의 경우 임펠러와 디퓨져와의 간격이 상당히 좁게 설계되기 때문에 임펠러와 디퓨져와의 매칭이 매우 중요해진다. 일반적으로 임펠러와 디퓨져 간의 베인리스 구간에서도 일부 동압이 정압으로 회복하고, 이 상태에서 베인 디퓨져로 유체가 유입된다. 이 구간이 짧아지면 임펠러 출구에서 높은 속도를 가진 유체가 그대로 디퓨져로 유입되게 되는데, 이 경우 디퓨져 입구 마하수가 높아져 입사각에 따른 손실이 커지게 되고, 디퓨져 유입 후 가속이 발생해 디퓨져 목에서 초킹 및 이어지는 충격파가 발생하여 디퓨져 내부에서 큰 전압손실이 발생할 수 있게 된다.
그리고 앞서 언급한 것처럼 엔진 전체의 조립성에 있어서 가장 중요한 부품 중 하나가 디퓨져 단이다. 대부분의 마이크로 가스터빈 엔진에서 디퓨져 단은 외부 하우징 및 압축기 Back plate간의 간격을 조정하고 둘 사이의 조립을 가능하게 하는 부품이다. 이에 대부분 마이크로 가스터빈에서 볼트 체결이 가능하도록 보통 두꺼운 쐐기형 디퓨져를 채용하여 볼트가 디퓨져를 관통하도록 설계한다.
이에 마이크로 가스터빈 전체에서 디퓨져 내의 손실 감소가 엔진 성능 향상에 가장 큰 비중을 차지한다고 해도 과언이 아니다. 앞서 언급한 임펠러 디퓨져 내의 추가적인 베인리스 구간 확보, 디퓨져 유로의 확장 및 급격한 축 방향 유동 선회 등의 현상을 완화하면 압축기 내부에서의 손실이 크게 감소하고 이로 인한 엔진의 SFC 등이 크게 개선될 수 있다. Burger 등은 Fig. 4(a)와 같이 두 가지 디퓨져 개선안을 제안하였고, 특히 디퓨져에서 디스월러로 연결되는 부분의 유로 곡률을 감소시키고, 디퓨져에서 디스월러로 이어지는 구간을 하나의 크로스오버(Cross-over) 디퓨져 적용 시, 실험결과 동일 추력을 발생시키기 위한 RPM이 약 15% 감소한 것을 확인하였다.(14,15)Fig. 4(b)와 같이 Colorado 주립 대학의 SPEC 프로젝트에서는 압축기 단 개조 시 디퓨져 조립부를 제외하고는 디퓨져 날개폭을 줄여 초킹 등의 현상을 회피하도록 디퓨져 재설계가 진행되었다.(16) 다른 연구사례에서도 기본적으로 Fig. 5와 같이 디퓨져 개선 설계 시 90° 유로가 꺾이는 부분의 곡률을 감소하는 방향으로 설계가 되며, 대부분 크로스오버 디퓨져 혹은 솔리디티가 작은 디퓨져(Low Solidity Diffuser, 이하 LSD)의 크로스오버 디퓨져로 대부분 설계 개선안이 수렴되며, 필요시 익렬 디퓨져 사이에 보조날개를 적용하거나(17), Fig. 6(a)와 같이 Tandem 디퓨져 혹은 다단 디퓨져를 적용하여 공력성능을 극대화하기도 한다.(18,19) 최근에는 이러한 LSD 구조를 채용한 엔진도 일부 발매되고 있는데, 이러한 엔진의 경우 유사급 엔진에 비해 SFC가 낮은 특징을 보여주고 있다.(20,21) 최근에는 Fig. 6(b)와 같이 2차원 LSD 설계를 탈피하여 3차원 형상으로 설계하여 전체적인 압축기 성능과 운용범위를 모두 개선한 연구사례가 보고되기도 하였다.(22)
3. 마이크로 가스터빈 대상 압축기 설계
앞서 설명한 마이크로 가스터빈 엔진 원심 압축기 공력설계 착안점을 반영하여, 마이크로 가스터빈 엔진에 적용하기 위한 원심압축기 임펠러 및 디퓨져 설계, CFD 수치해석을 진행하여 실제 마이크로 가스터빈 내부의 유동장을 분석해 보았다. 연구대상 엔진은 1,000N급 추력을 발생시키는 터보제트 엔진 코어로부터 파생 개발된 터보샤프트 엔진으로, 해당 엔진을 전기-가스터빈 하이브리드 추진기관으로 활용하고자 하며, 하이브리드 추진기관 성능 평가를 위해서는 압축기, 터빈 구성품의 성능맵이 필요하다. 이에 대상 엔진에 대해 공개된 정보 내에서 엔진의 구성품에 대한 설계를 진행하였으며, 본 논문에서는 압축기 설계 및 유동장 분석 내용을 소개하고자 한다.
해당 엔진의 가스발생기에는 원심압축기-축류터빈 구동계가 적용되어 있다. 가스발생기 하류에는 동력터빈이 위치하며, 동력터빈은 기어박스에 연결된 샤프트를 회전시킨다. Fig. 7과 같이 구성품 설계를 위한 기본적인 형상정보가 주어져 있으며, 이는 구성품 설계를 위한 기하학적인 제약조건으로 활용된다. 이를 바탕으로 비속도 분석을 진행하여 원심압축기-가스발생기 터빈의 회전수 및 동력터빈의 회전수를 결정하였다. 가스발생기 회전수는 성능에 민감한 압축기의 회전수에 따라 결정된다. 본 압축기에 대한 주요 설계변수는 Table 2에 제시되어 있다.
3.1 원심압축기 공력설계
원심압축기의 사이징 및 상세 익형설계는 Concepts NREC社(이하 CN社)의 Compal 및 AxCent를 활용하였다. 원심압축기는 주날개(Main Blade) 사이에 부날개(Splitter)를 적용하여 입구에서의 유로차폐를 최소화하였다. 설계 요구 압력비와 함께 충분한 스톨마진 확보를 위해서 임펠러 출구에 약 20°의 후연각을 주었다. 또한 임펠러 흡입면 팁 영역에서의 추가적인 압력 상승 및 허브에서 팁까지 압력 균일도를 개선하기 위해 임펠러 출구에 Lean 각도를 적용하였다.(23) 앞서 언급한 것과 같이 임펠러 출구-디퓨져 간의 간격이 매우 중요하며, 본 연구에서는 디퓨져 입구 반경/임펠러 출구 반경이 약 1.09가 되도록 베인리스 구간을 주었다. 일반적인 원심압축기의 디퓨져 입구 반경/임펠러 출구 반경임펠러 출구 반경 1.06∼1.12 사이에 분포하는데, 본 압축기에서는 임펠러 출구에서 1 이상의 절대 마하수가 예측되기 때문에 수치해석을 활용한 압축기 성능예측이 용이하도록 임펠러와 디퓨저 간의 간격을 조정하였다.
임펠러 하류에는 채널-캐스케이드 하이브리드 형태의 디퓨져를 적용하였다. 일반적인 직선형 쐐기 디퓨져 대신에 쐐기가 곡률을 가지도록 설계하여 디퓨져 출구 반경을 줄이고자 하였는데, 일반 채널 디퓨져의 디퓨져 출구 반경/디퓨져 입구 반경 값이 1.7∼1.8 사이에서 분포하는 반면 본 연구에서는 반경방향 길이 제한조건으로 인해 해당 값이 1.3미만으로 설계되었다. 디퓨져 내부에서 발생하는 유동박리 및 이에 따른 유로차폐로 인해 엔진으로 유입되는 공기의 질량유량이 제한될 수 있어, 이를 최대한으로 억제하고자 디퓨져 날개 개수 및 형상 등을 조정하였다. Fig. 8은 설계된 압축기 단의 3D 형상을 보여준다.
3.2 원심압축기 수치해석 및 결과
수치해석에는 상용 CFD 코드인 CFX를 사용하였으며, 격자는 Turbogrid를 이용하여 Hexa기반 격자계를 구성하였다. 임펠러 입구에는 전압력, 전온도 및 유동방향을 경계조건으로 주었으며, 디퓨져 하류에는 작동 조건에 따라 평균 정압력 혹은 질량유량을 경계조건으로 주었다. 임펠러와 디퓨져 간의 인터페이스로 Mixing plane을 사용하였으며, 옵션 중 Constant total pressure 옵션을 사용하여 인터페이스 하류에서의 속도를 계산하는데 전압력 및 유동방향을 사용하도록 하였다. 본 연구에서와 같이 임펠러와 디퓨져 간의 간격이 좁은 경우 해당 옵션을 사용하면 수치해석의 안정성이 높다고 알려져 있다.(24)
Fig. 9는 설계 회전수에서의 압축기 압력비 및 효율을 나타내고 있다. CFD에서 예측된 유량은 약 1.5% 정도 크게 예측되었으나 이는 설계의 미세 조정으로 조정 가능한 수치이다. 이에 전압력비 5.0의 수치해석 결과에 내부 유동장 분석을 진행하였다. Fig. 10은 설계점에서의 10%, 50%, 90% Span에서의 상대 마하수 분포를 나타내고 있다. 임펠러 허브 근처에서의 마하수는 1.0 이하의 값을 나타내며 상대적으로 두꺼운 날개 전연에서 유동 박리 없이 유체가 임펠러 쪽으로 잘 유입되는 것을 알 수 있다. 팁에서는 임펠러로 유체가 유입 시 주날개 전연에서 최대 마하수가 1.5 도달 후 충격파가 발생하는 것을 확인할 수 있다. 보조날개에서도 그 영역은 좁지만 유사한 충격파가 발생하는 것을 확인할 수 있다. 이러한 임펠러 전방 충격파가 마이크로 가스터빈의 작동영역을 제한하게 된다. 산업용 압축기의 경우 임펠러 전방에 IGV 등을 적용하여 임펠러 입구에서의 상대속도 및 상대 마하수를 감소시킬 수 있어 충분한 스톨마진을 확보할 수 있게 된다. 또한 유사한 크기의 임펠러가 적용되는 터보차저에서는 앞서 언급한 것과 같이 재순환 포트를 적용하여 스톨마진을 확장할 수 있게 된다. 하지만 공간 및 질량 제한조건이 가장 까다롭게 적용되는 마이크로 가스터빈 엔진에서는 임펠러 전연에서 스톨마진을 확장할 수 있는 추가적인 장치가 적용되기 매우 어렵다. 다만 마이크로 가스터빈의 경우 엔진 출구의 별도 배압이 걸리지 않는다면 하나의 작동선도에 따라 작동점이 이동하기 때문에 회전수에 따른 압축기의 작동선도를 정확히 예측하여 운전 중 스톨을 회피하여야 할 것이다. 대부분의 상업용 압축기 혹은 터보차저의 압축기에서는 임펠러 하류에서의 절대 마하수는 일반적으로 0.8∼0.9 사이로 설계하는데 반해, 본 해석 결과 임펠러 출구 절대 마하수는 전 영역에 걸쳐 마하수 1을 상회한다. 본 압축기의 경우 작동점에서의 전압력비가 5.0이기 때문에 임펠러 출구의 후연각을 키워 스톨마진을 증가시키는 데 한계가 있었다. 이에 압축비를 높이기 위해 후연각을 조정하여 전체 전압력 중 동압의 성분을 높였고, 이에 임펠러 출구 절대 마하수가 1.0을 상회하도록 설계되었다. 한편 임펠러 하류에서의 유동각 분포는 허브에서 쉬라우드까지 크게 변하며, 이에 2차원 형상으로 설계된 디퓨져 입구에서 높이에 따라 상당히 큰 입사각을 가지게 될 수 있게 된다. Fig. 10 (a)의 디퓨져 허브에서는 디퓨져 압력면에 대해 큰 음의 입사각을 가지고 디퓨져로 유체가 유입되는 것을 확인할 수 있다. 이에 유동이 가속 후 디퓨져 내부에서 충격파가 발생하며, 압력면에서 큰 유동박리가 발생하는 것을 볼 수 있다. 반면 임펠러 쉬라우드 쪽으로 갈수록 날개각과 유동각의 차이가 줄어들도록 설계되어 Fig. 10(c)의 90% 스팬에서는 입사각이 양의 값으로 전환되어 압력면에서 유동 박리 현상이 거의 사라지는 것을 확인할 수 있다. 본 연구에서는 디퓨져 하류에서의 90° 밴드 영역이 생략되어 있는데, 해당 영역에서 유동이 엔진 하우징 쪽으로 치우칠 때 손실을 최소화할 수 있다.
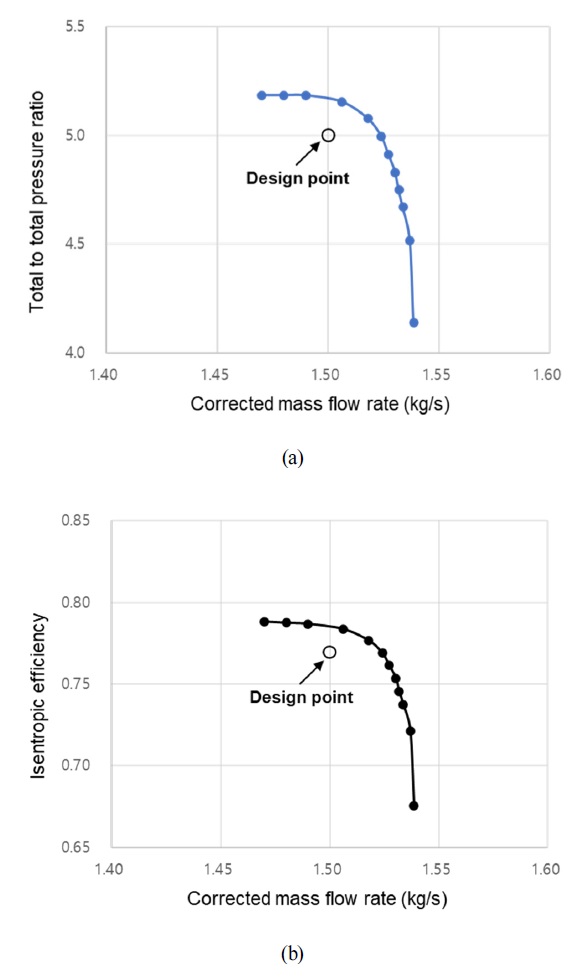
Compressor performance curve at design RPM: (a) Total to total pressure ratio, (b) isentropic efficiency
Fig. 11은 10%, 50%, 90% 스팬에서의 절대 전압력 분포를 나타내고 있다. 앞서 언급한 것처럼 10% 스팬에서의 디퓨져 영역에서 큰 손실이 발생하는 것을 확인할 수 있다. 10% 스팬에서 큰 유로 차폐가 발생하기 때문에 허브에서 쉬라우드 방향으로 디퓨져 내 유동이 쏠리면서 90% 스팬에서는 디퓨져 내에서 전압력이 회복되는 것처럼 보인다. 반면 Fig. 12에서는 입구에서 출구까지 전압력 분포를 나타내고 있다. 임펠러 출구에서 설계 압력비보다 훨씬 높은 6.0에 가까운 압력비를 나타내고 있으며, 디퓨져 출구에서는 임펠러 출구 전압력 대비 약 15%의 전압력 손실을 나타내고 있다. 연구대상 원심압축기에서 쐐기형 디퓨져를 적용하고 임펠러 디퓨져 간의 간격이 좁음에도 불구하고, 기존 에어포일 디퓨져를 장착한 설계안과 유사한 수준의 압력 손실량이 예측되었다.(19) 수치해석 결과 디퓨져 단의 유동이 압축기 성능을 저하시키는 것을 확인할 수 있었으며, Chung 등이 선행연구에서 수행한 상용 마이크로 가스터빈 수치해석에서도 유사한 문제가 발생한 사례가 있다.(25) 이에 다수 선행연구 등을 통해 확인된 크로스오버 디퓨져 적용 혹은 적층제조(26) 등을 통한 3D 디퓨져 적용을 통해 디퓨져 내의 손실 감소 및 전체 엔진 성능을 개선할 수 있을 것으로 보인다.
4. 결 론
본 논문에서는 마이크로 가스터빈 엔진에 적용되는 원심압축기의 공력성능 및 설계특성을 터보차저 압축기와 비교하여 설명하였으며, 마이크로 가스터빈 엔진 압축기 설계특성을 반영하여 마이크로 가스터빈 압축기 설계를 진행하였고, 해당 압축기 내부 유동장을 CFD 해석을 통해 분석함으로써 마이크로 가스터빈 엔진 내의 압축기 내부 유동장을 보다 상세히 파악할 수 있었다. 본 연구를 통해 다음과 같은 내용을 확인할 수 있었다.
1) 마이크로 가스터빈 압축기 설계 시 설계 요구 압력비를 확보하기 위해 후연각을 조정하였으며, 디퓨져의 경우 기하학적 제한조건을 만족시키기 위해 쐐기-에어포일 형상이 조합된 디퓨져 설계안을 적용하였다.
2) 마이크로 가스터빈 엔진 임펠러 전연에서의 상대 마하수 및 출구에서의 1이 넘는 절대 마하수가 예측되었다. 이에 임펠러 입구에서는 충격파에 따른 압축기 작동영역 제한 및 출구에서는 임펠러-디퓨져와의 매칭을 고려하여 설계를 진행하여야 함을 확인하였다.
3) 임펠러와 디퓨져 간의 매칭특성은 디퓨져 허브에서 쉬라우드로 갈수록 달라진다. 디퓨져 허브에서는 음의 입사각을 가지고 디퓨져에 유입되는데, 충격파에 의한 역압력구배를 극복하지 못하고 압력면에서 큰 재순환 영역 및 전압력 손실이 발생한다. 디퓨져 쉬라우드 쪽으로 가면 입사각이 양의 값으로 전환되며 재순환 영역 및 전압력 손실이 감소하는 것을 확인할 수 있었다. 제한된 공간 내에 설계된 디퓨져에서 발생하는 손실이 임펠러 출구 전압력 대비 약 15% 정도인 것으로 확인되었으며, 해당 손실원을 감소시킴으로써 압축기 효율 및 엔진 성능을 개선할 수 있을 것으로 생각된다.
Acknowledgments
본 연구는 한국항공우주연구원에서 수행 중인 ‘가스터빈기반 하이브리드 전기추진시스템 기술 개발’ 과제의 지원을 받아 수행되었습니다.
References
- https://minijets.org/en/home
- Sehra, Arun K., Shin, Jaiwon, 2003, “Revolutionary Propulsion Systems for 21st Century Aviation,” NASA TM-2003-212615.
-
Dong-Ho Rhee, Young Seok Kang, Heeyoon Chung, 2020, “Trends of Micro Turbojet Engines within Thrust Range up to 1,000N,” The KSFM Journal of Fluid Machinery, Vol. 23, No. 6, pp. 25-33.
[https://doi.org/10.5293/kfma.2020.23.6.025]
- Francis Oppong,Sybrand Johan van der Spuy, Theo von Backström, 2017, “An Overview of Micro Gas Turbine Engine Performance Investigation,” https://www.researchgate. net/publication/317312410_AN_OVERVIEW_OF_MICRO_ GAS_TURBINE_ENGINE_PERFORMANCE_INVESTIGAT ION
-
N. U. Rahman, J. F. Whidborne, 2008, “A Numerical Investigation into the Effect of Engine Bleed on Performance of a Single-Spool Turbojet Engine,” Proceedings of the Institution of Mechanical Engineers, Part G: Journal of Aerospace Engineering, Vol. 222, No. 7, pp. 939-949.
[https://doi.org/10.1243/09544100JAERO389]
-
M. Czarnecki, J. Olsen, 2018, “Combined Methods in Preliminary Micro Scale Gas Turbine Diffuser Design – a Practical Approach,” Journal of Applied Fluid Mechanics, Vol. 11, No. 3, pp. 567-575.
[https://doi.org/10.29252/jafm.11.03.28150]
-
Yohan Jung, Je Hyun Baek, Jun Young Park, Minsuk Choi, 2013, “Effects of Blade Back Sweep Angle on the Performance and Flow Field in a Centrifugal Compressor,” THE KSFM Journal of Fluid Machinery, Vol. 16, No. 2, pp. 48-53.
[https://doi.org/10.5293/kfma.2013.16.2.048]
- Macaera Preston Kock, 2017, “Design of a Cross-over Diffuser for a Mixed Flow Compressor Impeller,” MS. Thesis, Faculty of Mechanical and Mechatronic Engineering, Stellenbosch University
- https://www.adtechnology.com/
- https://www.bullseyepower.com/
- https://www.vividracing.com/
- Bosman Botha van der Merwe, 2012, “Design of a Centrifugal Compressor Impeller for Micro Gas Turbine Application,” MS. Thesis, Faculty of Mechanical and Mechatronic Engineering, Stellenbosch University.
-
Ziliang Li, Xin’gen Lu, Yanfeng Zhang, G. Han, Chengwu Yang, Shengfeng Zhao, 2018, “Numerical Investigation of a Highly Loaded Centrifugal Compressor Stage with a Tandem Bladed Impeller,” Proceedings of the Institution of Mechanical Engineers, Part A: Journal of Power and Energy 232, pp. 240-253.
[https://doi.org/10.1177/0957650917725406]
- C. Burger, 2015, “Design Procedure of a Compact Aerodynamic Crossover Diffuser for Micro Gas Turbine Application,” MS. Thesis, Faculty of Mechanical and Mechatronic Engineering, Stellenbosch University
-
C. J. Burger, S. J. van der Spuy and T. W. von Backström, 2019, “Design of a Compact Crossover Diffuser for Micro Gas Turbines Using a Mean-Line Code,” International Journal of Turbo & Jet-Engines, Vol. 36, No. 4, pp. 347-357.
[https://doi.org/10.1515/tjj-2017-0021]
- Dan Harthan etl al., 2018, “Specialized Propulsion Electronic Control System (SPECS) Conceptual Design Document,” University of Colorado Department of Aerospace Engineering Sciences Senior Projects - ASEN 4018.
-
Chen Jie, Huang Guoping, 2010, “Redesign of an 11 cm-diameter Micro Diffuser,” Chinese Journal of Aeronautics, Vol. 23, No. 3, pp. 298-305.
[https://doi.org/10.1016/S1000-9361(09)60219-3]
- Justin Jongsik Oh, 2018, “Diffuser Selection in Centrifugal Compressors,” https://turboaerodesign.com/
-
Young Seok Kang, Yong Min Jun, Jae Hwan Kim, 2018, “Main Components Design of a Small Turboshaft Engine,” THE KSFM Journal of Fluid Machinery, Vol. 21, No. 2, pp. 19-26.
[https://doi.org/10.5293/kfma.2018.21.2.019]
- Tom Wilkinson, 2006, “Hawk 100R Test,” Radio Control Jet International December 2006/January 2007, pp. 48-49.
- http://www.hawkturbine.com/
-
Abdelwahab A, Gerber G., 2008, “A New Three-Dimensional Aerofoil Diffuser for Centrifugal Compressors,” Proceedings of the Institution of Mechanical Engineers, Part A: Journal of Power and Energy, Vol. 222, No. 8, pp. 819-830.
[https://doi.org/10.1243/09576509JPE579]
-
Gbanaibolou Jombo, Jiri Pecinka, Suresh Sampath and David Mba, 2018, “Influence of fouling on compressor dynamics: Experimental and modelling approach,” ASME J. Eng. for Gas Turbines and Power, Vol. 140, No. 3.
[https://doi.org/10.1115/1.4037913]
-
Xiao He, Xinqian Zheng, 2016, “Mechanisms of Lean on the Performance of Transonic Centrifugal Compressor Impellers,” Journal of Propulsion and Power, Vol. 32, No. 5.
[https://doi.org/10.2514/1.B36008]
- ANSYS Press Release, 2013, ANSYS CFX Modelling Guide, Ansys Inc., Canonsburg, PA.
-
Heeyoon Chung, Dong-Ho Rhee, Young-Seok Kang, 2021, “Simulation of Aero-propulsion Micro Gas Turbine Engine Using CFD,” The KSFM Journal of Fluid Machinery, Vol. 24, No. 1, pp. 5-12.
[https://doi.org/10.5293/kfma.2021.24.1.005]
-
Jacob R. Holden, Thomas M. Caley, Brian Heberling, Cory Cantor, Eric Wesseling, Awatef A. Hamed, Mark G. Turner, Paul J Litke, Nicholas Grannan, 2016, “Novel Design and Fabrication of JetCat P90 Diffuser using Parametric Design and Optimization Tools,” The proceedings of 54th AIAA Aerospace Sciences Meeting, Sandiego, CA, AIAA 2016-2128.
[https://doi.org/10.2514/6.2016-2128]