
회전속도 변화에 따른 볼트 체결부 접촉강성변화를 고려한 터보분자펌프 로터의 고유진동수와 고유모드 변화에 관한 연구
Abstract
Even if active magnetic bearings are widely used in turbomolecular pumps, they experience more difficulty in controlling vibration in the unexpected frequency range, which is not considered in rotordynamics as rigid and flexible body mode. Since the blade wheel and main shaft of TMP are often assembled through bolt joint and interference fit, resonance frequencies are expected to vary according to rotating speed change, which is inevitably caused by the contact status of interference fit and blade wheel and main shaft assembled by bolt joint. In this paper, through finite element analyses, pre-stressed modal analyses are performed to compete with the variation of resonance frequencies and mode shapes for rotating parts of the large and medium capacity turbomolecular pump composed of the blade wheel and main shaft. Firstly, static strength analyses are performed to get pre-stress caused by rotating velocity and check structural integrity. Contact status is also checked on the surface of the interference fit, the surface between the balance plate and blade wheel, and the surface between the blade wheel and main shaft. Finally, modal analyses according to rotating speed are performed, and a Campbell diagram is made to find crossing points. It is found that mode separation and resonance frequency variation are caused by the contact status of the assembly of TMP rotating parts, which should be considered in the control of AMB.
Keywords:
Turbomolecular pump, Resonance frequency, Interference fit, Bolt joint, Contact status, Campbell diagram키워드:
터보분자펌프, 공진 주파수, 열박음량, 볼트 체결, 접촉 상태, 캠벨 선도1. 서 론
터보분자펌프는 반도체 공정 라인 중 극청정(Ultra Clean Environment) 및 극진공(Ultra High Vacuum) 환경을 제공하며, 터보분자펌프의 크기와 성능은 입구직경, 블레이드 각, 회전속도 등에 의해 좌우된다.(1)
또한 전체적인 배치(Layout)에 있어서도 협소한 공간 하에서 좋은 성능을 발현하기 위하여 원심력에 의한 구조강도 및 정격속도에 도달하기까지 만나게 되는 임계속도(Critical Speed)에서의 공진여부 등이 분석되어야 한다.
능동형 마그네트 베어링(Active Magnetic Bearing)은 정상적인 작동 시 마찰력과 마모율이 거의 없기 때문에 운영과정에서 터보분자펌프와 같은 별도의 윤활을 사용할 수 없는 환경에서 회전체를 지지하고 안정성을 확보하기 위해 그 사용이 증가하고 있다.(2)
안정적인 회전부의 부양을 위해 능동형 마그네트 베어링은 회전체의 시스템 분석(System Identification)을 수행하고 위치 정보를 이용하여 피드벡 제어(Feedback Control)를 필요로 한다. 하지만 대부분의 경우 회전체의 시스템 분석 시 Beam 요소를 이용한 회전체동역학(Rotor Dynamics)을 수행하여 전체 회전체 모델의 강체 모드(Rigid Mode)나 유연 모드(Flexible Mode)를 분석하며, Fig. 1과 같이 이보다 상대적으로 낮은 주파수 영역에서 발생할 수 있는 블레이드 공진 모드를 별도로 고려하여야 한다.(2)
대부분의 터보분자펌프의 회전부는 시스템 특성 상 Fig. 2와 같이 여러 단(Stage)이 종모양으로 제작된 블레이드 휠(Blade Wheel)를 마그네트 베어링으로 제어되는 주축(Main Shaft)과 일정량의 열박음(Interference Fit) 및 전하중(Pre Load)을 적용하여 볼트로 체결한다.
마그네트 베어링으로 제어하는 동안에 회전체동역학 모델에서 분석했던 강체 모드나 유연 모드 및 블레이드 휠의 블레이드 공진 모드 외에 예측하지 않았던 주파수 영역에서 진동이 발생하는 현상이 다수 직면하게 되었다.
본 연구에서는 회전속도가 상승함에 따라 블레이드 휠과 주축 간의 열박음 상태나 전하중을 적용한 볼트체결부의 강성 변화가 기존에 고려하지 않았던 추가적인 공진모드를 발생하는 것으로 예상하여 이를 3차원 유한요소해석을 통해 분석하고, 회전속도 변화에 따른 고유진동 모드의 변화를 Campbell 선도로 분석해 보았다.
터보분자펌프 관련 국내 연구 사례로는 터보분자펌프의 회전체동역학해석(3), 터보분자펌프의 설계를 위한 유한요소해석(4), 터보분자펌프의 블레이드 휠의 형상최적설계(5) 관련 연구 사례가 있다.
국외 연구 사례로는 제어를 위한 베어링 및 축의 회전체 동역학 해석 및 시험(6,7), 자기베어링과 연계한 대용량 터보분자펌프 형상 설계(8), 터보분자펌프 블레이드의 모드해석을 위한 모델링 기법(1), 터보분자펌프 블레이드 휠에 대한 모드해석(9) 사례가 있다.
하지만 금번 논문에서 다루고자 하는 회전속도 변화에 따라 블레이드 휠과 주축 간 볼트 체결 강성 변화에 따른 고유진동수의 변화를 고려한 연구사례는 없는 상황이다.
2. 유한요소모델 및 정적강도해석
대용량(Large Capacity) 모델과 중용량(Medium Capacity) 모델이 같은 단수로 설계되더라도 블레이드 휠 형상이 다소 다르기 때문에 두 가지 모델을 각각 고려하였으며, 본 해석의 목표에 해당하는 부품만을 고려하기 위해 Fig 2(a)에 해당하는 부품만 유한요소해석에 포함시켰으며, 주축의 경우도 자기베어링이나 모터와 관련된 부품은 모두 제외하고 순수 축 부품만 고려하였다.
고유진동 모드를 분석하기에 앞서 모드해석에서 적용할 전응력(Pre-Stress)을 얻고, 회전부의 구조 건전성을 검토하기 위해 정적강도해석을 ANSYS Mechanical 프로그램을 이용하여 수행하였다. 또한, 조립 상태 및 작동조건에 따라 열박음면과 볼트 체결 시 밸런스 판(Balance Plate), 블레이드 휠(Blade Wheel) 및 주축(Main Shaft)이 만나는 면에서의 접촉 상태의 변화를 알아 보았다.
Fig. 3과 같이 하중으로는 자중(Gravity)와 정격회전속도의 104%에 해당하는 원심력을 적용하였으며, 반경(Radial)방향 및 축(Axial)방향 경계조건은 자기베어링에 의해 제어되는 면을 기준으로 마찰력이 없는 구속조건(Frictionless)을 적용하였다.
대용량 터보분자펌프 회전부 유한요소모델의 경우 Fig.4와 같이 3,978,361개의 절점(Node)과 2,558,601개의 요소(Element)로 구성하였으며, 강도해석 후 모드해석을 연계해서 수행하기 위해 컴퓨팅 환경과 해석시간을 고려하여 위의 개수를 선정하였다.
회전부 결합 시 Fig. 2(b)와 같이 블레이드 휠과 주축 간에 편심으로 최대 0.03mm, 최소 0.01mm의 열박음량(Interference Fit)을 각각 적용하고, Fig. 2(a)와 같이 밸런스 판을 거쳐 블레이드 휠과 주축을 볼트 체결 시 1개 당 10,876N의 체결력을 전하중으로 적용하였다.
모든 부품 간 접촉조건은 마찰계수 0.15를 적용한 ‘Frictional’ 비선형 접촉조건을 적용하였다.
주요 결과로는 Fig. 5 및 Table 1과 같이 블레이드 휠의 축방향/반경방향 최대 변위, 볼트와 주축에서의 최소 안전계수(인장항복강도/발생한 최대 Von-Mises 응력)를 비교하였다. 특이한 것은 단별로 축방향 변위 방향이 다르게 발생하며, 최대 반경방향 변위는 블레이드 휠의 Drag 부분에서 발생했다. 열박음량의 변화가 발생 변위에는 큰 영향을 주지 못했지만, 열박음량의 증가가 볼트와 주축의 안전계수를 증가시키는 효과는 있는 것으로 판단된다.
Fig. 6 부터 Fig. 8은 조립 상태 및 작동조건(열박음 후, 열박음+전하중을 적용한 볼트 체결 시, 열박음+전하중을 적용한 볼트 체결+정격속도 104% 작동 시)에 따른 부품 간 접촉부 압력분포 및 접촉상태를 보여주고 있다.
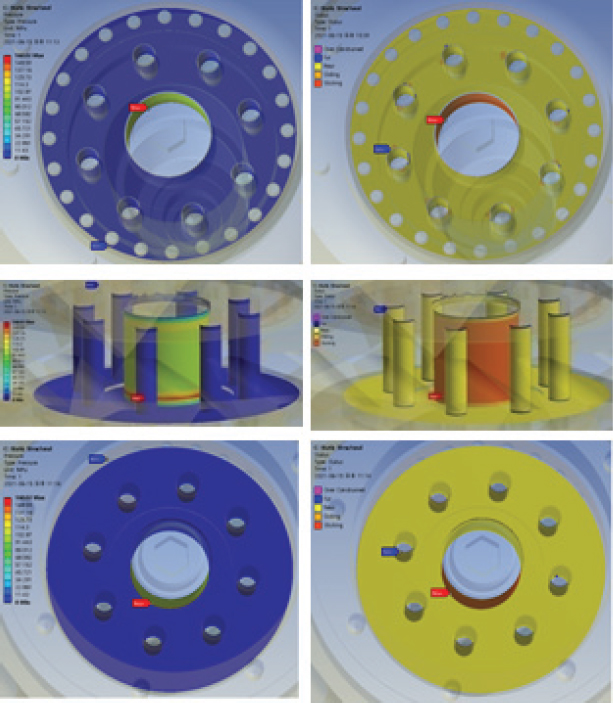
Contact Pressure and Contact Status When only Applying Interference Fit Between Blade Wheel and Main Shaft
Fig. 6과 같이 열박음만 적용한 경우 밸런스 판과 블레이드 휠의 접촉면과 블레이드 휠과 주축의 접촉면에는 접촉면 사이에 움직이지 없이 잘 고정되는 상태를 보여주는 기준인 접촉상태가 ‘Sticking’인 영역은 나타나지 않으며, 오롯이 열박음면만 접촉상태가 ‘Sticking’인 영역이 발생하는 것을 볼 수 있다.
하지만 열박음 후 전하중을 적용한 볼트 체결 시 Fig. 7과 같이 밸런스 판과 블레이드 휠의 접촉면과 블레이드 휠과 주축의 접촉면에도 접촉상태가 ‘Sticking’인 영역이 대부분을 차지하는 것을 볼 수 있다.
마지막으로 정격속도의 104% 작동 시에는 열박음면이나 블레이드 휠과 주축의 접촉면에는 접촉상태가 ‘Sticking’인 영역은 일부 영역에서만 나타나며, 단지 밸런스 판과 블레이드 휠의 접촉면에만 부분적 또는 대부분이 접촉상태가 ‘Sticking’인 영역이 발생하는 것을 알 수 있다.
열박음량이 작은 경우에는 접촉상태가 ‘Sticking’인 영역마저 감소하는 것을 알 수 있다.
Table 2의 결과를 보면 정격속도의 104% 작동 시 열박음량이 0.03mm일 때 보다는 0.01mm일 때 접촉상태가 ‘Sticking’인 영역이 줄어들며, 대용량 모델일 때 접촉상태가 ‘Sticking’인 영역이 더 줄어들어 볼트 체결로 인해 확보할 수 있는 접촉강성은 더 불리하게 확보되는 것을 예상할 수 있다.
Fig. 9와 같이 정격속도로 블레이드 휠이 회전할 때 원심력에 의해 변형이 발생하며, 이를 위해 볼트가 허용하는 전하중을 충분히 적용하더라도 그것이 주축과 충분한 접촉강성을 갖게 하는데는 한계가 있다는 결론을 얻을 수 있다.
결론적으로 회전속도에 따라 밸런스 판과 블레이드 휠의 접촉면, 열박음면 그리고 블레이드 휠과 주축의 접촉면에 접촉상태가 ‘Sticking’인 영역이 발생하는 정도가 달라져서 결국 경계조건이 달라지기 때문에(경계조건 비선형) 같은 공진 모드 그룹(Mode Family)이라도 회전수에 따라 고유진동수나 모드 형태도 달라질 수 있음을 예상할 수 있다.
3. 모드해석
3.1 중용량 터보분자펌프 회전부의 모드해석
주요 회전수 마다 정적강도해석을 수행한 뒤 이 때 발생된 전응력상태를 반영한 모드해석(Pre-Stressed Modal Analysis)을 수행하였다.
중용량 모델의 경우 최초 공진모드로는 Fig. 10(a)와 같이 모든 단의 노드 지름(Nodal Diameter)이 1인 형태를 가지는 Blade Bending 모드와 Wheel Bending 모드가 결함된 형태로 고유모드가 발생하며, 이 모드는 Fig. 11에서 보는 것과 같이 회전속도가 증가함에 따라 Fig. 10(b)와 Fig. 10(c)와 같이 모드 분리가 발생함을 알 수 있다. 이후의 공진모드로는 5단과 6단이 노드 지름이 0인 형태를 가지는 Blade Bending 모드가 축방향으로 Fig. 10(d)와 같이 Out of Phase 및 Fig. 10(e)와 같이 In Phase를 가지는 형태로 고유모드가 발생하는 것을 알 수 있다.
그 다음 공진모드로는 5단과 6단이 노드 지름이 1인 형태를 가지는 Blade Bending 모드가 Fig. 10(f)와 같이 축방향으로 Out of Phase를 가지는 형태로 발생하는 것을 알 수 있다.
논문에서의 마지막 공진모드로는 5단과 6단이 노드 지름이 2인 형태를 가지는 Blade Bending 모드가 Fig. 10(g)와 같이 축방향으로 In Phase를 가지는 형태로 고유모드가 발생하는 것을 알 수 있다.
중용량 모델에 대해 주요 회전수마다 모드해석을 수행하여 Campbell 선도를 구성해 보았다. 열박음량이 0.03mm인 경우 정격회전속도 이하에서는 공진이 발생하지 않으나, 회전수가 계속 증가하여 정격속도의 113% 정도가 되면 공진 마진이 많지 않은 것을 확인할 수 있었다. 정격회전속도 이상이 되면 모든 단이 ND1의 형태를 가지는 Blade Bending 모드와 Wheel Bending 모드가 결함된 형태로 모드로 분리되며, 회전수가 증가함에 따라 Wheel Bending 모드의 고유진동수는 감소하는 것을 알 수 있었다. 이는 회전속도에 따른 원심력의 작용으로 인한 열박음면과 블레이드 휠과 주축 간 접촉면 중 접촉상태가 ‘Sticking’인 영영의 감소로 인해 접촉강성의 저하(Degradation)에서 기인된 것으로 예상되며, 이로 인해 모드 분리도 발생하는 것으로 예상된다.
최소 열박음량(0.01mm)인 경우에도 정격회전속도 이하에서는 공진이 발생하지 않으나, 모드 분리가 발생하는 회전수가 열박음량이 0.03mm일 때보다는 낮아지는 것(정격회전속도의 75% 이상)을 확인할 수 있었다. 결론적으로 중용량 모델의 경우 열박음량이 회전 조립체 강성에 영향을 주는 것을 알 수 있다. 이는 Table 2(b)의 결과와 같이 열박음량이 0.01mm인 경우 주요 접촉면에서의 접촉상태가 ‘Sticking’인 영역이 줄어든 것이 원인으로 예상된다.
3.2 대용량 터보분자펌프 회전부의 모드해석
대용량 모델의 경우에도 최초 공진모드로는 Fig. 12(a)와 같이 모든 단의 노드 지름이 1인 형태를 가지는 Blade Bending 모드와 Wheel Bending 모드가 결합된 형태로 고유모드가 발생하며, 중용량 TMP 모델과 유사하게 회전속도가 증가함에 따라 Fig. 12(b)와 Fig. 12(c)와 같이 모드 분리가 발생함을 알 수 있다. 이후의 공진모드로는 Fig. 12(d)부터 Fig. 12(f)와 같이 1단 블레이드 모드가 노드 지름이 증가하는 형태로 공진모드가 발생하는 것을 알 수 있다.
대용량 모델에 대해서도 주요 회전수마다 모드해석을 수행하여 Campbell 선도를 구성해 보면 열박음량이 0.03mm 또는 0.01mm 인 경우 모두 정격회전속도 이하에서는 공진이 발생하지 않는 것을 알 수 있다. 하지만 Fig. 13과 같이 중용량 모델보다는 상대적으로 낮은 회전수(정격회전속도의 50% 이상)에서 모든 단의 노드 지름이 1인 형태를 가지는 Blade Bending 모드와 Wheel Bending 모드로 분리되는 것을 확인할 수 있었으며, 열박음량이 0.01mm인 경우에도 비슷한 회전수에서 모드 분리가 발생하는 것을 알 수 있다. 결론적으로 대용량 모델의 경우 열박음량이 모드 분리에 주는 영향도는 낮은 것을 확인할 수 있다. 이는 Table 2(a)의 결과와 같이 대용량 모델의 경우 열박음량에 상관 없이 주요 접촉면에서의 접촉상태가 ‘Sticking’인 영역이 일부분만 발생한 것이 원인으로 예상된다. 즉, 대용량 모델의 경우 정격회전속도의 50% 이상이 되면 주요 열박음면이나 접촉면에서는 볼트 체결 시 적용했던 전하중이 추가 강성을 크게 발생하지 못하는 것으로 예상된다. 이를 개선하기 위해 더 큰 용량의 볼트에 더 큰 전하중을 적용할 수 있겠으나, 주어진 주축의 직경으로 인해 한계가 있을 것이다.
4. 결 론
본 연구에서는 회전속도가 상승함에 따라 블레이드 휠과 주축 간의 열박음 상태나 전하중을 적용한 볼트체결부의 강성 변화가 기존에 고려하지 않았던 추가적인 공진모드를 발생하는 것으로 예상하여 이를 3차원 유한요소를 적용하여 분석하고, 회전속도 변화에 따른 고유진동 모드의 변화를 Campbell 선도로 분석해 보았다.
대용량 및 중용량 터보분자펌프의 회전부에 대해 모드해석에서 적용할 전응력(Pre-Stress)을 얻고, 회전부의 구조 건전성을 검토하기 위해 정적강도해석을 수행하였다. 또한, 조립 상태 및 작동조건에 따라 열박음면과 볼트 체결 시 밸런스 판, 블레이드 휠 및 주축이 만나는 면에서의 접촉 상태의 변화를 알아 보았다.
열박음량으로 0.03mm와 0.01mm를 각각 적용하였으며, 밸런스 판을 거쳐 블레이드 휠과 주축을 볼트 체결 시 체결력을 전하중으로 적용하였다.
열박음 후 전하중을 적용한 볼트 체결 시에는 주요 접촉면의 접촉상태가 ‘Sticking’인 영역이 대부분을 차지하였으나, 정격속도의 104% 작동 시에는 열박음면이나 블레이드 휠과 주축의 접촉면에는 접촉상태가 ‘Sticking’인 영역은 일부 영역에서만 나타나며, 단지 밸런스 판과 블레이드 휠의 접촉면에만 부분적 또는 대부분이 접촉상태가 ‘Sticking’인 영역이 발생하는 것을 알 수 있었다. 또한, 대용량 모델인 경우와 중용량 모델이더라도 열박음량이 0.01mm인 경우에는 접촉상태가 ‘Sticking’인 영역마저 감소하는 것을 알 수 있었다.
결론적으로 정격속도로 블레이드 휠이 회전할 때 원심력에 의해 변형이 발생하며, 이를 위해 볼트가 허용하는 전하중을 충분히 적용하더라도 블레이드 휠이 주축과 충분한 접촉강성을 갖게 하는데는 한계가 있다는 결론을 얻을 수 있었다.
주요 회전수마다 정적강도해석을 수행한 뒤 이 때 발생된 전응력상태를 반영한 모드해석을 수행하였다. 중용량 모델의 경우 열박음량에 따라 모드 분리가 발생하는 회전수가 달라지는 것을 알 수 있었으며, 대용량 모델의 경우 열박음량이 모드 분리가 발생하는 회전수에 주는 영향도는 낮은 것을 알 수 있었다. 이는 볼트 체결 시 적용하는 전하중이 추가 강성을 크게 발생하지 못하는 것으로 예상된다.
본 연구의 결과를 보았을 때 터보분자펌프에 능동형 마그네트 베어링 적용 시 회전부 결합 강성을 분석하는 것은 제어 측면에서 필수불가결함을 알 수 있었다.
Acknowledgments
이 논문은 2022년도 산업통상자원부의 재원으로 한국산업기술평가관리원의 지원을 받아 수행된 논문임(과제번호 : 20011567, 과제명 : 디스플레이 반도체 공정비교용 1.3E-8mbar 이하 초고진공 터보분자펌프 기술개발)
References
-
Huang, Z., Han, B. C., and Le, Y., 2017, “Modeling Method of the Modal Analysis for Turbomoleculer Pump Rotor Blades,” Vacuum, Vol. 144, pp. 145–151.
[https://doi.org/10.1016/j.vacuum.2017.07.029]
-
Hutterer, M. and Schrodl, M., 2017, “Control of Active Magnetic Bearings in Turbomoleculer Pumps for Rotors with Low Resonance Frequencies of the Blade Wheel,” Lubricants, 5, 26.
[https://doi.org/10.3390/lubricants5030026]
- Han, J. S., 2011, “Rotor Dynamics Analysis of a Turbomoleculer Pump,” Proceedings of Korean Society for Noise and Vibration Engineering 2011, pp. 764–765.
- Lee, W. Y., Kook, J. H., Park, J. K. and Koo, B. H., 2002, “Analysis for Design of a High Vacuum Turbomoleculer Pump,” Journal of Korean Society of Semiconductor Equipment Technology, Vol. 1, No1, pp. 41–45.
-
Won, B. R., Jung, H. Y. and Han, J. S., 2013, “Structural Analysis and Shape Optimization for Rotor of Turbomoleculer Pump Using P-Method,” Transaction Korean Society of Mechanical Engineering A, Vol. 37, No. 10, pp. 1279–1289.
[https://doi.org/10.3795/KSME-A.2013.37.10.1279]
-
Hsu, C. N., 2015, “Experimental and Performance Analyses of a Turbomolecular Pump Rotor System,” Vacuum, Vol. 121, pp. 260–273.
[https://doi.org/10.1016/j.vacuum.2015.06.029]
-
Hsu, C. N., Chiang, H. W., Huang, Y. M., Fu, Y. C., Hsu, K. H. and Li, C. H., 2011, “Rotor Dynamics Analysis and Testing of a Turbomoleculer Pump Rotor-Bearing System,” ASME Turbo Expo 2011, Vancouver, Canada, GT‐2011‐46159.
[https://doi.org/10.1115/GT2011-46159]
-
Han, B. C., Huang, Z., and Le, Y., 2017, “Design Aspects of a Large Scale Turbomoleculer Pump with Active Magnetic Bearings,” Vacuum, Vol. 142, pp. 96–105.
[https://doi.org/10.1016/j.vacuum.2016.12.010]
-
Chatelet, E., D’ambrosio, F. and Jacquet-Richardet G., 2005, “Toward Global Modelling Approaches for Dynamic Analyses of Rotating Assemblies of Turbomachines,” Journal of Sound and Vibration, Vol. 282, pp. 163–178.
[https://doi.org/10.1016/j.jsv.2004.02.035]