
가스터빈 동익 블레이드 회전이 팁 주변 열전달 계수에 미치는 영향에 대한 수치해석적 연구
Abstract
In this study, the variations in heat transfer coefficients (HTC) on the turbine blade tip were compared for a stationary cascade configuration, a stationary cascade configuration with a moving shroud, and a 3D annular rotating blade with stationary nozzle. The tip HTC distributions of the stationary cascade cases and 3D rotor blade case were numerically investigated. It was revealed that the location and size of the hotspot HTC regions were different for each case. Furthermore, the HTC distributions of the 3D rotor blade were conducted for various relative motions. The results showed that at the lower relative motions, the HTC distribution is similar to that of the stationary cascade configuration. However, as the relative motion is increased, the hotspot location on the tip is moved toward the pressure side and trailing edge of the blade. It was observed that the dominant effect on the HTC pattern around the 3D rotor blade tip is the viscous force generated by the relative motion of the shroud and blade tip, which surpasses the effects of centrifugal and Coriolis forces on the heat transfer characteristics of the blade tip. Additionally, the HTC distributions around the tip of the 3D rotor blade and the cascade configuration with a moving shroud were compared, which showed a similar overall HTC pattern. The findings of this study are anticipated to serve as valuable reference data for the implementation of cooling hole installations based on the hotspot regions on the gas turbine blade tips.
Keywords:
Gas turbine, Blade tip, Tip leakage flow, Cavity, Reattachment, Heat transfer coefficient, Hotspot키워드:
가스터빈, 블레이드 팁, 팁 누설유동, 캐비티, 재부착, 열전달계수, 고온부1. 서 론
가스터빈(Gas turbine)은 항공기용 가스터빈 엔진 및 산업용 발전기 등에 적용되며, 압축기, 연소기 및 터빈 등으로 구성된다. 가스터빈 내의 터빈은 회전을 통해 동축의 압축기 및 발전기를 구동시키는 역할을 하며, 보통 정익과 동익의 스테이지로 구성된다. 정익은 동익의 앞에 위치하여 유동이 동익 입구로 적절히 유입될 수 있도록 유동각 등의 입구 조건을 형성시키는 역할을 하며, 동익은 정익으로부터 유입되는 유동에 의해 회전을 하고, 동시에 기계에 에너지를 전달하는 역할을 한다. 동익은 회전하는 부품이므로 필연적으로 팁(Tip)과 쉬라우드(Shroud) 사이에 간극이 형성되어 누설 유동이 발생한다. 팁 누설 유동은 동익에서 발생하는 주요한 손실 중 하나로, 공력 손실을 초래하는 것뿐만 아니라 팁 주변에서 높은 열부하를 국소적으로 발생시킨다. 팁 누설 유동은 팁의 압력면 근처에서 베나 수축부(Vena contracta) 및 유동 박리 기포(Separation bubble) 현상을 생성한다고 알려져 있다. 이러한 현상들로 인해 블레이드 팁에서는 유동이 재부착 되어, 높은 압력 및 온도에 의해 국소적으로 열응력이 가해지는 문제가 발생하게 된다(1). 이는 블레이드 내구성 및 수명에 큰 문제를 발생시킬 수 있으므로 반드시 해결되어야 한다.
팁 주변의 공력 손실과 열응력 문제를 해결하기 위해 스퀼러 팁(Squealer tip), 부분 캐비티 팁(Partial cavity tip) 등 다양한 팁 형상이 제시되었고, 많은 연구가 수행되었다. Azad 등(2), Kwak과 Han(3)은 2차원 캐스케이드(Cascade)를 대상으로 팁에서의 열전달 계수를 측정하였고, 평판 팁보다 스퀼러 팁에서 누설 유동과 열전달 계수가 감소하는 긍정적인 결과를 확인하였다. 이후에 Saxena와 Ekkad(4)는 단일 스퀼러 팁을 압력면, 흡입면 및 캠버라인(Camber line)에 설치한 형상, Lomakin 등(5)과 Nasir 등(6)은 스퀼러 팁의 림(Rim) 부분을 일부 제거한 형상, Park 등(7)은 스퀼러 팁에 립(Rib)을 추가한 형상, Jeong 등(8)은 평판 팁과 이중 스퀼러 팁을 조합한 형상을 제시하여 공력성능과 열전달 계수에 미치는 영향에 대해 분석하였다. 팁의 형상 변화와 관련된 이전 논문을 종합하면, 스퀼러 팁 및 부분 캐비티 팁 등의 형상 변화는 팁 주변 열부하 감소에 긍정적인 효과를 나타내는 것으로 확인되었다. 그러나, 팁 주변에서 국소적으로 열부하가 집중되는 문제는 완전히 해결되지는 않았으며, 이는 형상 변경과 함께 추가적인 작업이 적용되어야 국소적인 열부하 문제를 완전히 해결할 수 있음을 의미한다. 따라서, 이를 극복하기 위해 팁을 포함한 터빈 블레이드 주변에 여러 개의 냉각 홀(Cooling hole)을 설치하는 것이 대안으로 고려되었으며, 이와 관련된 많은 연구가 수행되었다(9,10). 냉각 홀 설치 관련 연구에서는 냉각 홀을 블레이드 표면의 고온부(Hotspot) 위치에 직접 설치하거나, 냉각 홀로부터 분사되는 냉각 유량이 고온부 위치로 효과적으로 흘러갈 수 있도록 설치하는 막냉각 방법들이 조사되었다. 이러한 연구들을 통해 냉각 홀을 적절한 위치에 설치하기 위해서는 블레이드 주변에서 발생하는 고온부 위치를 정확하게 파악하는 것이 매우 중요하다는 사실이 확인되었다.
가스터빈의 동익 블레이드는 오래전부터 캐스케이드 실험을 통하여 성능평가연구가 수행되었다. 이는 3D 블레이드의 회전을 적용하여 실험을 수행하는 것이 어렵고 비용이 많이 필요한 점, 그리고 3D 블레이드에서 발생 되는 2차 유동 현상들이 캐스케이드에서도 유사하게 발생 되는 점 등을 고려하였기 때문이다. 그러나 캐스케이드에서 발생 되는 2차 유동들이 실제와 유사한 경향을 보이더라도, 실제 3D 블레이드 내부에서 회전에 의해 발생 되는 원심력(Centrifugal force), 코리올리력(Coriolis force) 및 블레이드와 쉬라우드 사이에서 발생 되는 상대 운동 영향은 포함되지 않기 때문에 정확한 유동 패턴은 다를 수 있다. 이러한 차이는 블레이드 주변의 열전달 계수의 차이를 발생시키며, 결과적으로 고온부 발생 위치를 정확하게 파악하지 못하는 문제를 발생시킬 수 있다. 특히 팁 주변에서는 블레이드와 쉬라우드 사이의 상대 운동에 의한 점성 효과가 추가되어 고온부 발생 위치를 정확하게 파악하는 것을 더욱 어렵게 만들 수 있다.
터빈 내부에서의 원심력 및 코리올리력 결합 효과 관련 연구는 Sleiti와 Kapat(11)에 의해 수행되었다. 이들은 원심력 및 코리올리력의 결합은 전단부에서는 블레이드 표면의 유동 박리를 유도하고, 후단부 블레이드 표면 근처에서는 가속을 유발한다고 언급하였다. Bangga 등(12)은 코리올리력과 원심력에 대한 수식을 제시하였다. 또한, 다단 터빈 등의 다양한 터빈 형상을 대상으로 원심력 및 코리올리력의 영향에 관한 연구가 수행되었고, 모든 연구에서 통과 와류와 후류 사이에 흥미로운 메커니즘을 보였다고 언급하였다. Yaras와 Sjolander(13)는 터빈 캐스케이드에 회전 효과를 적용할 수 있는 실험장치를 구축하여 터빈 내부의 유동 패턴을 확인하는 연구를 시도하였고, 결과적으로 그들은 블레이드의 스크래핑 효과(Scraping effect)로 인해 통로 와류가 강화되고, 와류가 흡입면 쪽으로 끌린다는 결론을 내렸다. Misul(14)은 선형 캐스케이드를 대상으로 원심력 및 코리올리력 등의 회전 효과를 적용하여 시뮬레이션을 수행하는 방법을 제시하였다.
회전하는 블레이드와 정지된 쉬라우드 사이에서는 상대 운동이 발생하며, 이러한 영향에 대한 연구는 오래전부터 다양하게 수행되었다. Chyu 등(15)은 블레이드 팁과 쉬라우드의 상대 운동 효과가 팁 간극 유동에 추가적인 전단력을 가하는 것을 관찰하였고, 이러한 힘이 캐비티 내부에서 발생 되는 재순환 영역에 추가로 재순환 영역을 생성시킨다고 언급하였다. Coull 등(16)은 상대 운동 효과로 인해 팁 간극 유량이 감소 되는 것을 발견하였고, Yaras 등(13)은 상대 운동이 통로 와류와 누설 와류를 흡입면 방향으로 밀어서 부분적으로 누설 유동이 감소 된다고 언급하였다. Zhu 등(17)은 팁 간극과 쉬라우드 사이의 상대 운동에 대한 관계를 나타냈고, 팁 간극이 좁을수록 상대운동 효과는 더 커진다고 언급하였다. Zhang(18)은 팁 주변에서 상대 운동이 열전달 분포를 변경시킨다고 언급하였고, Zhou(19)는 엔드월(Endwall) 운동이 너셀 수(Nusselt number) 분포를 크게 변경시키는 것을 확인하였다. 이후 Zhou와 Virdi(20)는 스퀼러 팁에 대한 시뮬레이션을 수행하여 팁 주변에서 상대운동이 캐비티 내부의 미드 코드(Mid-chord) 주변 유동에 큰 영향을 미친다고 설명하였다. Lu 등(21)과 Xie 등(22)은 선형 캐스케이드를 대상으로 고속으로 회전하는 쉬라우드 장치를 구축하여 상대 운동에 의한 열전달 계수 분포를 확인하는 연구를 수행하였다. 따라서, 이전 연구를 종합하면, 팁 간극의 상대운동 효과는 팁 주변의 고온부 발생 위치를 정확하게 파악하기 위해 자세하게 분석되어야 하는 현상으로 확인되었다. 또한, 상대 운동에 대한 연구가 주로 캐스케이드에서 수행되었기 때문에, 실제 3D 동익 블레이드에서 상대 운동에 대한 팁의 HTC 분포 변화 연구가 필요한 것으로 조사되었다.
본 연구에서는 고정 캐스케이드(Stationary cascade), 회전이 적용된 환형의 3D 동익 블레이드(3D annular rotating blade) 및 무빙 쉬라우드가 적용된 고정 캐스케이드(Stationary cascade with moving shroud)를 대상으로 팁 주변 열전달 계수를 비교 및 분석하는 것을 목적으로 한다. 또한, 회전이 적용된 3D 환형의 동익 블레이드에서 상대 운동 변화에 따른 팁 주변의 열전달 계수 변화를 비교하여, 원심력, 코리올리력 및 블레이드-쉬라우드 사이의 상대운동 효과 중 팁 주변 열전달 계수에 가장 지배적인 영향을 미치는 현상을 확인한다.
2. 수치해석 방법
2.1 해석 모델 선정
본 연구에서는 무인항공기용 가스터빈 엔진에 적용하기 위해 개발된 터빈 형상을 전산 해석 모델로 선정하였다. 이 터빈 모델은 단(Stage)으로 구성되며, 정익 블레이드는 36개, 동익 블레이드는 56개이다. 입구 조건은 고온고압의 조건이며, 동익 블레이드 팁의 마하수는 약 0.265를 나타낸다. 전산 유동해석과 실험의 비교검증은 동익 블레이드 팁 형상을 사용하여 Fig. 1과 같이 고정 캐스케이드(stationary cascade) 형상으로 모델링하여 진행되었다. 회전이 포함된 3D 환형의 해석 도메인은 Fig. 2와 같이 정익-동익의 단으로 구성하였다.
2.2 수치해석 설정
Fig. 1의 고정 캐스케이드 도메인 내부 해석 격자는 Pointwise V18.3 소프트웨어(23)를 이용하여 Fig. 3과 같이 정렬 격자와 비정렬 격자가 모두 포함된 쿼드(Quad) 타입으로 생성되도록 하였다. 적절한 격자 수를 결정하기 위해 Grid Convergence Method (GCI)(24,25)를 이용하였고, Fig. 4와 같이 GCI1,2, GCI2,3값 모두 2% 이내를 보이는 약 850만 개의 격자 수를 적절한 격자 수로 결정하였다. 벽면에서는 격자가 조밀하게 형성되어 Y+가 2 이하가 되도록 설정하였다. 유동해석은 ANSYS CFX 2020 R1 소프트웨어(26)를 사용하였으며, 난류 모델은 SST RM(Reattachment modification) 모델을 적용하였다. 본 연구 대상인 스퀼러 팁의 경우, 압력면 림에서 박리된 유동이 캐비티 바닥에 재부착되며, 이때 고온부가 발생하는 특징을 갖는다. 따라서, 유동의 재부착 위치를 가장 적절하게 예측하는 것으로 알려진 SST RM 난류 모델을 본 연구의 난류 모델로 선정하였다(27,28). 고정 캐스케이드의 입출구 조건은 실험 수행이 가능한 압력과 온도조건으로 마하수 상사를 통해 결정되었다. 입구 경계조건은 Fig. 1과 같이 속도, 온도 및 난류 강도 등이 설정되었으며, 쉬라우드 근처에는 속도 프로파일을 적용하였다. 출구 경계조건으로는 정압을 적용하였고, 작동 유체 조건으로는 이상기체를 사용하였다. 쉬라우드와 허브는 모두 단열 조건을 적용하였고, 블레이드는 HTC(Heat transfer coefficient)를 계산하기 위해 일정한 벽면 온도(Constant wall temperature)와 단열 벽면(Adiabatic wall) 조건에서 모두 계산하였다. 본 연구에서 사용된 열전달 계수(HTC)는 식 (1)과 같다.
(1) |
여기에서, Wall heat flux는 블레이드 벽면에서의 열유속을 나타내며, T는 일정한 벽면 온도가 적용되었을 때의 계산된 블레이드 벽면 온도를 의미하고, Tadw는 단열 벽면 조건이 적용되었을 때 계산된 블레이드 벽면 온도를 의미한다. 식 (1)을 이용한 HTC 계산 절차는 Fig. 5와 같다.
3D 환형의 정익-동익 도메인은 Fig. 2와 같으며, 정익 블레이드 2개와 동익 블레이드 1개로 구성되었고, 입출구는 각각 동익과 정익 블레이드의 약 3배로 확장하여 설정하였다. 3D 환형의 정익-동익 해석 영역은 ANSYS Mesh 소프트웨어(29)를 이용하여 Fig. 6과 같이 비정렬 사면체 격자(Tetrahedron grid)로 생성하였다. 허브, 쉬라우드 및 블레이드 벽면에는 모두 20개 이상의 프리즘 층(Prism layer)을 적용하였다. 격자 수는 Fig. 7과 같이 Grid Convergence Method (GCI)를 이용하여 GCI1,2, GCI2,3값이 모두 2% 이내를 보이는 약 1,000만 개의 격자 수를 적절한 격자 수로 결정하였다. 벽면 근처(Near wall)에서는 격자를 조밀하게 생성하여 Y+ 값을 2 이하가 되도록 설정하였다. 3D 블레이드의 경계조건은 Fig. 2와 같이 입구에는 고온고압 조건을 설정하였으며, 출구에는 정압조건으로 설정하였다. 허브와 쉬라우드는 단열 벽면 조건으로 설정하였다.
2.3 수치해석 검증
수치해석 검증은 고정 캐스케이드 형상을 대상으로 스팬 50%, 90%에서 정압계수분포(Fig. 8) 및 팁의 HTC 분포(Fig. 9)를 실험 결과와 비교하여 진행하였다. 한편, 실험은 한국항공대학교 실험실에서 수행되었으며(30), 실험에서 사용된 고속시험리그와 선형 캐스케이드 형상을 Fig. 8에 나타냈다. 본 연구에서 정압계수분포는 식 (2)와 같이 계산된다.
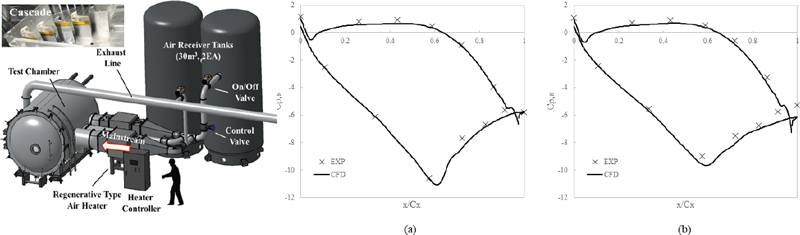
Validation of Cp,s between experimental result and CFD simulation in stationary cascade: (a) 50% of span, (b) 90% of span
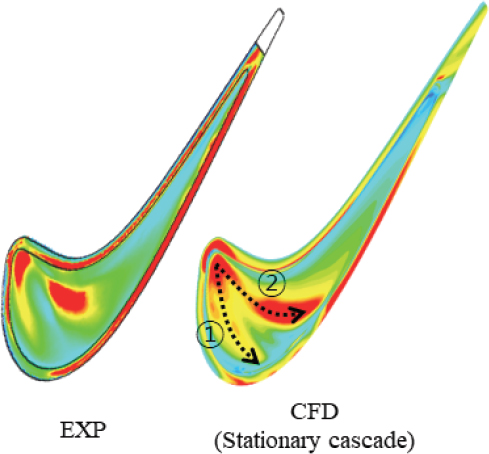
Validation of HTC distribution near the tip between experimental result and CFD simulation in stationary cascade
(2) |
여기에서, Ps,surface는 블레이드 표면에서 정압력, Pt,inlet는 입구에서 전압력, Ps,inlet는 입구에서 정압력을 의미한다. 스팬 50% 및 90% 위치에서 정압계수분포의 경우, 해석결과가 실험 결과에 상당히 근접하게 나타나는 것으로 확인되었다. 팁의 HTC의 경우, LE(Leading edge) 근처의 팁과 캐비티 바닥, 미드 코드 근처 캐비티 바닥에서 발생한 고온부가 해석과 실험 양쪽에서 상당히 유사한 경향을 보였다. 특히, LE 근처 캐비티 바닥에서 고온부가 발생한 이후 고온부가 두 갈래로 분리되는 현상이 유사하게 관찰되었다. 한편, 본 연구에서는 Fig. 9의 CFD 결과에서 HTC가 두 갈래로 분리되는 부분을 각각 고온부 ①, ②로 명명하기로 한다. 고온부 ①은 LE 근처 림에서 박리된 유동, 고온부 ②는 압력면 림에서 박리된 유동이 각각 캐비티 바닥에 재부착되며 발생 된다.
3. 결과 및 논의
3.1 고정 캐스케이드 및 3D 동익 블레이드 팁의 HTC 비교
고정 캐스케이드 및 3D 동익 블레이드 해석결과를 팁의 HTC 분포로 Fig. 10과 같이 비교하였다. 고정 캐스케이드는 실제 3D 동익 블레이드 팁의 형상을 이용하여 단순화시킨 모델로 실험에서 다양한 연구를 수행하기 위해 사용되는 모델이다. 이러한 고정 캐스케이드에는 회전이 적용되지 않으므로 팁의 HTC에 회전 효과가 포함되지 않는다. 따라서, 회전 효과가 포함된 팁의 HTC와의 차이를 비교하기 위해, 회전 효과가 포함된 3D 동익 블레이드 팁의 HTC 분포와 비교하였다. 여기에서, 3D 동익 블레이드 팁의 HTC는 3D 환형의 정익-동익 도메인(Fig. 2)에서 동익 블레이드 팁의 HTC를 나타낸다.
Fig. 10에서 팁의 HTC 비교결과, 고온부 ①의 경우, 고정 캐스케이드보다 3D 동익 블레이드에서 약간 감소하였으며, 고온부 ②의 경우, 고정 캐스케이드보다 3D 동익 블레이드에서 압력면과 TE 쪽으로 더 이동한 것을 확인할 수 있다. 팁의 HTC를 정량적으로 비교하기 위해, Fig. 11과 같이 고정 캐스케이드 및 3D 동익 블레이드의 팁 주변 HTC를 임의로 축코드 방향 5등분을 하였고, 전체 면적 평균값에 대한 각 구간의 면적 평균값으로 구한 Normalized HTC를 비교하였다. 1∼2번 영역에서는 3D 동익 블레이드의 HTC 값이 고정 캐스케이드보다 감소하였고, 3번 영역에서는 거의 유사하였으며, 4∼5번 영역에서는 증가하였다. 고정 캐스케이드와 3D 동익 블레이드 모두 TE로 향할수록 전반적으로 HTC 값은 감소하였지만, 3D 동익 블레이드의 4번 영역에서는 3번 영역보다 HTC 값이 오히려 증가하는 경향을 보였다. 이는 3D 동익 블레이드와 쉬라우드의 상대 운동에 의한 점성 효과로 고온부 ②가 압력면과 TE 쪽으로 이동하였기 때문으로 보인다.
3.2 상대 운동 변화에 따른 3D 동익 블레이드 팁의 HTC 비교
본 연구에서는 3D 동익 블레이드와 쉬라우드의 상대 운동 변화에 따른 팁의 HTC 변화를 비교하기 위해, 3D 환형의 정익-동익 도메인(Fig. 2)에서 동익 쉬라우드의 회전속도를 변경하여 팁의 HTC 변화를 파악하는 연구를 수행하였다. 보통 전산 해석에서 회전계의 경계조건 설정 시 도메인 전체를 회전 프레임으로 설정하고, 쉬라우드를 counter rotating wall로 설정하여 동익 블레이드만 회전이 적용되도록 설정하는 것이 일반적이다. 본 연구에서는 이러한 동익 쉬라우드의 회전속도를 변경하여 상대 운동의 영향을 비교하는 방법을 채택하였다. 이는 정익 블레이드로부터 유입되는 동익 입구 조건을 일정하게 유지하며, 3D 동익 블레이드와 쉬라우드 사이의 상대 운동이 팁의 HTC에 미치는 영향을 파악하기 위해서다. 따라서, 본 연구에서는 상대운동비(Relative motion ratio)를 식 (3)과 같이 도입하기로 한다.
(3) |
여기에서, RPMBlade는 동익의 회전속도, RPMShroud는 동익 쉬라우드의 회전속도를 의미한다.
3D 동익 블레이드와 쉬라우드의 상대운동비는 Table 1과 같이 0, 0.236, 0.472, 0.708, 1로 선정하였고, 0일 때는 상대 운동이 없는 것을 의미하고, 1일 때는 쉬라우드에 counter rotating wall이 적용된 것을 의미한다. 이 상대 운동에 따른 3D 동익 블레이드 팁의 HTC 분포 변화를 Fig. 12와 같이 나타냈다. 3D 동익 블레이드 팁과 쉬라우드의 상대 운동이 작은 경우에는 3D 동익 블레이드 팁의 HTC 분포가 고정 캐스케이드 팁의 HTC 분포와 유사한 경향을 보였다(Case 1∼2). 3D 동익 블레이드 팁과 쉬라우드의 상대 운동이 커질수록(Case 2∼5) 3D 동익 블레이드 팁의 고온부 ①은 점점 감소하였으며, 고온부 ②는 압력면과 TE 쪽을 향해 이동하는 경향을 보였다. 즉, 이러한 결과는 3D 동익 블레이드와 쉬라우드 사이에 발생 되는 상대 운동이 팁 주변 열전달 계수에 가장 지배적으로 영향을 미치고 있다는 것을 의미한다.
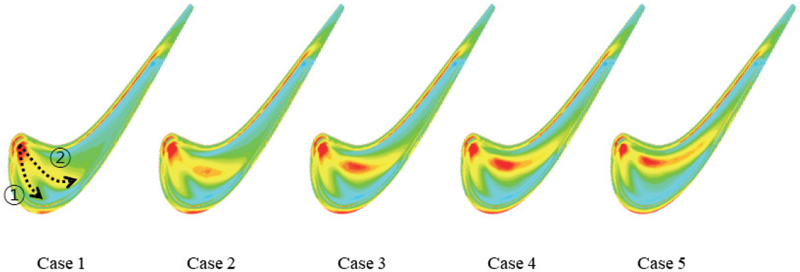
Comparison of HTC distribution near the tip for each case with different relative motion in the 3D rotating blade
상대 운동 변화에 따른 팁의 HTC 변화가 가장 크게 발생 되는 영역을 확인하기 위해, Fig. 13과 같이 축코드 방향으로 5등분 후 전체 면적 평균값에 대한 각 구간의 면적 평균값으로 구한 Normalized HTC를 비교하였다. 각각의 영역별로 팁의 HTC 값은 서로 다른 변화를 보이며, 1번 영역과 4번 영역에서 가장 큰 변화가 나타나는 것으로 확인되었다. 2번 영역과 3번 영역도 변화가 있지만, 1번 영역과 4번 영역보다 변동 값이 적은 것으로 확인되었으며, 5번 영역은 다른 영역에 비해 거의 변화가 없는 것으로 확인되었다. 1번 영역과 2번 영역의 HTC 감소는 상대 운동이 증가함에 따라 고온부 ①이 점점 감소하였기 때문으로 판단된다. 3번 영역과 4번 영역의 HTC 증가는 상대 운동이 증가함에 따라 고온부 ②가 점점 압력면과 TE 쪽으로 이동하였기 때문으로 보인다. 5번 영역에서 상대 운동에 따른 HTC 값이 전체적으로 변화가 거의 없는 이유는 Fig. 12와 같이 고온부 ②가 5번 영역까지는 영향을 거의 미치지 않았기 때문으로 보인다.
블레이드 팁과 쉬라우드 사이의 상대 운동의 변화가 블레이드 팁 주변의 고온부 발생 위치 변화에 미치는 영향을 자세히 파악하기 위해, 유선(Fig. 14) 및 와도 분포(Fig. 15)를 비교 분석하였다. Fig. 14에는 축코드 10%, 20%, 30%, 40%, 50% 위치의 평면에서 유선을 나타내며, 압력면 림에서 박리된 유동이 캐비티 바닥에 재부착 되는 것을 확인할 수 있다. 또한, 상대 운동이 커질수록 쉬라우드의 점성력에 의해 재부착되는 위치가 압력면과 TE 쪽을 향하여 이동하는 것을 확인할 수 있다. 이 재부착 되는 위치는 Fig. 12에서 고온부 ②가 발생 되는 위치와 같다.

Effects of relative motion on streamline and reattachment position near the blade tip: (a) Case 1, (b) Case 3, (c) Case 5
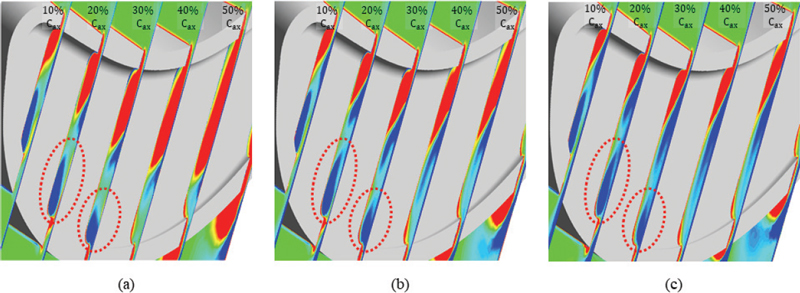
Effects of relative motion on x-component of vorticity contour near the blade tip: (a) Case 1, (b) Case 3, (c) Case 5
Fig. 15는 축코드 10%, 20%, 30%, 40%, 50% 위치의 평면에서 와도 분포를 나타내며, 붉은색 영역과 파란색 영역은 서로 반대 방향으로 회전하는 유동을 의미한다. 상대 운동이 증가함에 따라 쉬라우드의 점성력에 의해 캐비티 내의 붉은색 영역은 감소하고, 파란색 영역은 점점 증가하는 것을 확인할 수 있다. 또한, Fig. 15에서 상대 운동이 증가하면서 붉은색 점선 영역 내의 파란색 와도가 캐비티 바닥 근처에서 압력면 및 쉬라우드를 향해 약간씩 이동하는 현상이 포착되었으며, 이로 인해 고온부 ①이 약간씩 감소한 것으로 확인되었다.
3.3 3D 동익 블레이드 및 무빙 쉬라우드가 적용된 고정 캐스케이드 팁의 HTC 비교
Fig. 16에 3D 동익 블레이드와 무빙 쉬라우드가 적용된 고정 캐스케이드 팁의 HTC를 나타냈으며, 고정 캐스케이드 팁의 HTC와 함께 비교하였다. 여기에서, 3D 동익 블레이드 팁의 HTC는 Fig. 2의 도메인에서 동익 블레이드 팁의 HTC를 나타낸다. 또한, 무빙 쉬라우드가 적용된 고정 캐스케이드 팁의 HTC는 Fig. 1의 고정 캐스케이드 도메인에서 쉬라우드에 무빙 조건을 적용했을 때 팁의 HTC를 나타낸다.
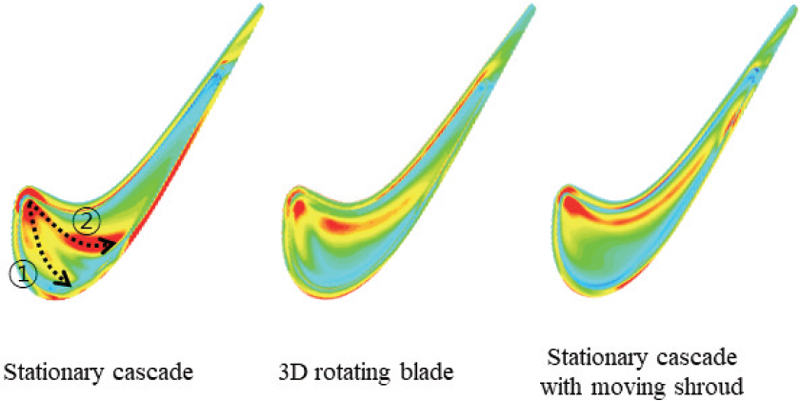
Comparison of normalized HTC distribution near the tip for stationary cascade, 3D rotating blade, and stationary cascade with moving shroud
Fig. 16에서 팁의 HTC 분포를 비교한 결과, 3D 동익 블레이드 및 무빙 쉬라우드가 적용된 고정 캐스케이드의 결과는 고정 캐스케이드 결과와는 크게 다른 것을 확인할 수 있다. 그러나, 3D 동익 블레이드와 무빙 쉬라우드가 적용된 고정 캐스케이드의 결과는 상당히 유사하게 나타나는 것으로 확인되었다. 특히, 고온부 ②가 압력면과 TE 방향으로 이동하는 경향이 유사하게 나타나는 것으로 확인되었다.
고정 캐스케이드, 3D 동익 블레이드 및 무빙 쉬라우드가 적용된 고정 캐스케이드 팁의 HTC를 Fig. 17과 같이 축코드 방향으로 5등분 후 전체 면적 평균값에 대한 각 구간의 면적 평균값으로 구한 Normalized HTC를 비교하였다. 2번 영역과 3번 영역에서는 3D 동익 블레이드 및 무빙 쉬라우드가 적용된 고정 캐스케이드 팁의 HTC가 거의 유사하게 나타나는 것으로 확인되며, 1번, 4번, 5번 영역에서는 약간 다른 값을 보였다. 1번 영역에서 약간의 차이가 발생한 원인은 Fig. 16에서 고온부 ①이 약간 감소 된 것과 관련 있으며, 4번 영역과 5번 영역에서의 차이가 발생한 원인은 고온부 ②가 3D 동익 블레이드보다 약간 더 압력면과 TE 쪽으로 이동하였기 때문으로 보인다. 위의 결과를 종합해보면, 고정 캐스케이드 팁의 HTC 분포는 3D 동익 블레이드 팁의 HTC 분포와 큰 차이를 보이지만, 무빙 쉬라우드가 적용된 고정 캐스케이드 팁의 HTC 분포는 3D 동익 블레이드 팁의 HTC 분포와 매우 유사한 경향을 나타내고 있음을 알 수 있다.
4. 결 론
본 연구에서는 고정 캐스케이드, 3D 동익 블레이드 및 무빙 쉬라우드가 적용된 고정 캐스케이드를 대상으로 팁의 열전달 계수 분포의 차이를 비교 분석하였고, 본 연구의 결론을 요약하면 다음과 같다.
- 1) 고정 캐스케이드와 3D 동익 블레이드 팁의 HTC 분포를 비교한 결과, 고온부 발생 위치는 유사하나 고온부 영역의 크기와 경향은 다르게 나타나는 것으로 확인되었다. 특히, 3D 동익 블레이드의 고온부는 팁과 쉬라우드의 상대 운동에 의해 발생 되는 점성 효과에 의해 고온부가 전체적으로 압력면과 TE 쪽으로 이동하는 경향을 보였다.
- 2) 3D 동익 블레이드에서 팁과 쉬라우드 사이의 상대 운동 변화에 따른 팁의 HTC 분포 변화를 비교한 결과, 상대 운동이 작을 때는 고정 캐스케이드 팁의 HTC 분포와 유사한 결과를 보였으며, 상대 운동이 증가함에 따라 고온부 ①은 점점 감소하였고, 고온부 ②는 압력면과 TE 쪽으로 이동하는 것을 확인하였다. 따라서, 3D 동익 블레이드 팁의 HTC는 원심력 및 코리올리력보다 팁과 쉬라우드의 상대 운동에 의한 점성 효과가 지배적인 것으로 확인되었다.
- 3) 3D 동익 블레이드와 무빙 쉬라우드가 적용된 고정 캐스케이드 팁의 HTC를 비교한 결과, 고온부 ②가 약간 더 압력면과 TE 쪽으로 이동하였지만, 전체적인 팁의 HTC 경향은 비슷한 것으로 확인되었다. 본 연구의 결과들은 터빈 팁에서 발생 되는 국소적인 열부하 문제를 해결하기 위해 냉각 홀을 설치할 경우 유용한 참고 자료로 활용될 것으로 전망된다.
Acknowledgments
본 연구는 방위사업청과 국방과학연구소가 지원하는 무인기용 고효율 터빈기술 특화연구센터 사업의 일환으로 수행되었습니다.
References
-
Lee, B. J., Park, K. S., Jeong, J. Y., kwak, J. S., & Chung, J. T., 2021, “Numerical Investigation on Effects of Rib or Cavity Design of Gas Turbine Blade Tip on the Flow and Heat Transfer Characteristics near Tip Region,” The KSFM Journal of Fluid Machinery, Vol. 24, No. 3, pp. 5–14.
[https://doi.org/10.5293/kfma.2021.24.3.005]
-
Azad, Gm. S., Han, J.-C., and Boyle, R. J., 2000, “Heat Transfer and Flow on the Squealer Tip of a Gas Turbine Blade,” Journal of Turbomachinery, Vol. 122, No. 4, pp. 725-732.
[https://doi.org/10.1115/1.1311284]
-
Kwak, J. S. and Han, J.-C., 2003, “Heat Transfer Coefficients on the Squealer Tip and Near Squealer Tip Regions of a Gas Turbine Blade,” Journal of Heat Transfer, Vol. 125, No. 4, pp. 669-677.
[https://doi.org/10.1115/1.1571849]
-
Saxena, V. and Ekkad, S. V., 2004, “Effect of Squealer Geometry on Tip Flow and Heat Transfer for a Turbine Blade in a Low Speed Cascade,” Journal of Heat Transfer, Vol. 126, No. 4, pp. 546-553.
[https://doi.org/10.1115/1.1777580]
-
Lomakin, N., Granovskiy, A., Belkanov, V., and Szwedowicz, J., 2013, “Effect of Common Blade Tip Squealer Designs in terms of Tip Clearance Loss Control,” Proceedings of the ASME 2013 Turbine Blade Tip Symposium and Course Week, TBTS2013-2040.
[https://doi.org/10.1115/TBTS2013-2040]
-
Nasir, H., Ekkad, S. V., Kontrovitz, D. M., Bunker, R. S., and Prakash, C., 004, “Effect of Tip Gap and Squealer Geometry on Detailed Heat Transfer Measurements over a High Pressure Turbine Rotor Blade Tip,” Journal of Turbomachinery, Vol. 126, No. 2, pp. 221-228.
[https://doi.org/10.1115/1.1731416]
-
Park, J. S., Lee, S. H., Kwak, J. S., Lee, W. S., and Chung, J. T., 2013, “Measurement of blade tip heat transfer and leakage flow in a turbine cascade with a multi-cavity squealer tip,” Proceedings of the ASME 2013 Turbine Blade Tip Symposium and Course Week, TBTS2013-2072.
[https://doi.org/10.1115/TBTS2013-2072]
-
Jeong, J. Y., Kim, W., Kwak, J. S., and Park, J. S., 2019, “Heat Transfer Coefficient and Film Cooling Effectiveness on the Partial Cavity Tip of a Gas Turbine Blade,” Journal of Turbomachinery, Vol. 141, No. 7, 71007.
[https://doi.org/10.1115/1.4042647]
-
Zamiri, A., Barigozzi, G., & Chung, J. T., 2022, “Large eddy simulation of film cooling flow from shaped holes with different geometrical parameters,” International Journal of Heat and Mass Transfer, 196, 123261.
[https://doi.org/10.1016/j.ijheatmasstransfer.2022.123261]
-
Zamiri, A., You, S. J., & Chung, J. T., 2020. “Large eddy simulation of unsteady turbulent flow structures and film-cooling effectiveness in a laidback fan-shaped hole,” Aerospace Science and Technology, 100, 105793.
[https://doi.org/10.1016/j.ast.2020.105793]
-
Sleiti, A. K., & Kapat, J. S., 2008, “Effect of Coriolis and centrifugal forces on turbulence and transport at high rotation and density ratios in a rib-roughened channel,” International Journal of Thermal Sciences, Vol. 47, No. 5, pp. 609–619.
[https://doi.org/10.1016/j.ijthermalsci.2007.06.008]
-
Bangga, G., Kim, Y., Lutz, T., Weihing, P., & Krämer, E., 2016, “Investigations of the inflow turbulence effect on rotational augmentation by means of CFD,” Journal of Physics: Conference Series, Vol. 753, No. 2.
[https://doi.org/10.1088/1742-6596/753/2/022026]
-
Yaras, M. I., & Sjolander, S. A., 1992, “Effects of simulated rotation on tip leakage in a planar cascade of turbine blades: Part I-Tip gap flow,” Journal of Turbomachinery, Vol. 114, No. 3, pp. 652–659.
[https://doi.org/10.1115/1.2929189]
- Misul, D. A., Salvadori, S., Hahn, M. S. M., & Desiderio, G, 2022, “Numerical Analysis of the Influence of Rotation on Aerodynamic Effects in Axial Turbine Cascades.”
-
Chyu, M. K., Metzger, D. E., & Hwan, C. L, 1987, “Heat transfer in shrouded rectangular cavities. Journal of thermophysics and heat transfer,” Vol. 1, No. 3, pp. 247-252.
[https://doi.org/10.2514/3.35]
-
Coull, J. D., & Atkins, N. R., 2015, “The influence of boundary conditions on tip leakage flow,” Journal of Turbomachinery, Vol. 137, No. 6, 061005.
[https://doi.org/10.1115/1.4028796]
-
Zhu, D., Zhang, Q., Lu, S., & Teng, J., 2020, “Relative casing motion effect on squealer tip cooling performance at tight tip clearance,” Journal of Thermal Science and Engineering Applications, pp. 1-18.
[https://doi.org/10.1115/1.4046518]
-
Zhang, Q., O’Dowd, D. O., He, L., Oldfield, M. L. G., & Ligrani, P. M., 2011, “Transonic turbine blade tip aerothermal performance with different tip gaps—part I: tip heat transfer.”
[https://doi.org/10.1115/GT2010-22779]
-
Zhou, C., Hodson, H., Tibbott, I., & Stokes, M., 2012, “Effects of endwall motion on the aero-thermal performance of a winglet tip in a HP turbine.”
[https://doi.org/10.1115/GT2011-46373]
-
Virdi, A. S., Zhang, Q., He, L., Li, H. D., & Hunsley, R., 2015, “Aerothermal performance of shroudless turbine blade tips with relative casing movement effects,” Journal of Propulsion and Power, Vol. 31, No. 2, pp. 527-536.
[https://doi.org/10.2514/1.B35331]
-
Lu, S., Zhang, Q., & He, L., 2020, “A High-Speed Disk Rotor Rig Design for Tip Aerothermal Research,” In Turbo Expo: Power for Land, Sea, and Air (Vol. 84188, p. V07CT13A012). American Society of Mechanical Engineers.
[https://doi.org/10.1115/GT2020-14624]
- Xie, W., Peng, X., Jiang, H., Lu, S., Gu, Y., Chen, C., & Zhang, Q., 2021, “Experimental Study of Turbine Blade Tip Heat Transfer with High-Speed Relative Casing Motion,” Proceedings of the Global Power and Propulsion Society, Xi’an, China, pp. 18-20.
- Pointwise, Version 18.3, 2019, Pointwise Inc., Fort Worth, TX.
-
Celik, I. B., Ghia, U., Roache, P. J., Freitas, C. J., Coleman, H., & Raad, P. E., 2008. “Procedure for estimation and reporting of uncertainty due to discretization in CFD applications,” Journal of Fluids Engineering, Transactions of the ASME, Vol. 130, No. 7, 0780011–0780014.
[https://doi.org/10.1115/1.2960953]
-
Park, K. S., Zamiri, A., Choi, M., Lee, B. J., & Chung, J. T., 2023, “Numerical Optimization of a Stator Blade to Enhance Aerodynamic Performance in a Transonic Fan Stage,” European Journal of Mechanics-B/Fluids.
[https://doi.org/10.1016/j.euromechflu.2023.10.003]
- Ansys CFX, Version 2020 R1, 2020, Ansys Inc. Canonsburg, PA.
- Menter, F. R., Sechner, R., & Matyushenko, A., 2021. Best Practice: RANS Turbulence Modeling in Ansys CFD, 2–95. https://www.ansys.com/resource-center/technical-paper/best-practice-rans-turbulence-modeling-in-ansys-cfd
- Ansys CFX-Solver Theory Guide., 2023.
- Ansys Meshing, Version 2020 R1, 2020, Ansys Inc. Canonsburg, PA.
-
Kwak, J. S., Jeong, J. Y., Kang, Y. J., Kim, G. M., Lee, S. I., 2021, “Development of a Transonic Cascade Facility for the Heat Transfer Research of Gas Turbine Blade Tip,” The KSFM Journal of Fluid Machinery, Vol. 24, No. 2, pp. 28-33.
[https://doi.org/10.5293/kfma.2021.24.2.028]