
마이크로 두께 구리폼의 공극률에 따른 풀비등 열전달 성능
Abstract
As electronic equipment’s overheating issues become more serious, heat transfer through latent heat, especially by utilizing boiling, is gaining more attention compared to sensible heat. Surface modification, including the use of metal foams, can be employed to enhance boiling and thus improve heat transfer performance. Metal foams, being easily obtainable and possessing a micro-porous structure, have been used in several studies for promoting boiling. However, most of these studies used metal foams with a thickness greater than 1 mm and did not consider an important factor: porosity. Therefore, this study analyzed the change in pool boiling heat transfer performance with varying porosities of micro-thick copper foam through experimentation and visualization. Experiments were conducted with copper foams of thickness 200 μm and porosities of 54 %, 68 %, and 85 %. Regarding the heat transfer coefficient, the 68 % porosity copper foam showed the highest value at 273.7 kW/m2⋅K, while the 85 % porosity foam showed the lowest at 144.2 kW/m2⋅K. The Critical Heat Flux(CHF) was highest for the 8 5 % porosity foam at 237.5 W/cm2, and lowest for the 54 % porosity foam at 174.7 W/cm2. Visualization analysis indicated that the heat transfer coefficient decreases with increasing porosity due to reduced conductive effects at low heat flux. At high heat flux, where bubble escape resistance is also a crucial factor, the 54 % porosity copper foam exhibited the highest heat transfer coefficient. At very high heat flux, where the effect of bubble escape resistance is dominant, the 85 % porosity foam achieved the highest CHF. These results provide guidance in selecting the appropriate porosity for copper foams used in boiling enhancement, based on the desired superheat and CHF.
Keywords:
Pool boiling, Surface enhancement, Copper foam, Bubble behavior키워드:
풀비등, 표면 개질, 구리폼, 버블 거동1. 서 론
최근 전자장비들은 소형화와 집적도 증가로 인해 전력 밀도가 상승하였고, 이에 따라 발열 문제가 대두되고 있다.(1) 하지만 기존의 전자장비 냉각 방법인 공냉 및 수냉 방식으로는 첨단 전자장비의 열유속을 감당하기에 한계에 도달한 상황이다. 이러한 문제에 대응하기 위해, 잠열을 이용한 냉각 방식이 기존의 현열 기반 방식에 비해 더 효율적인 대안으로 제시되고 있다.(2) 잠열은 상변화를 통해 더 많은 열을 흡수하고 방출할 수 있으며, 특히 고밀도 전자장비에서 발생하는 높은 열유속을 효과적으로 관리하는 데 유리하다. 이러한 이유로, 잠열을 활용한 상변화 열전달, 특히 비등 열전달이 주목받고 있다. 비등 열전달은 다양한 냉각 분야에서 활용될 수 있는 높은 가능성을 지니고 있어 연구가 활발히 진행되고 있다.
비등 열전달이 냉각에 적용되기 위해 개선해야 할 몇 가지 중요한 요소들이 있다. 개선된 비등 곡선을 실선으로, 일반적인 비등 곡선을 점선으로 표시하여 개선 요소들을 Fig.1 에 나타내었으며 각 요소들은 다음과 같다.(3) 첫 번째, 비등 열전달의 incipience excursion의 감소가 필요하다. Incipience excursion은 핵 비등이 시작되면서 과열도가 급격히 감소하는 현상을 말한다. Fig. 1에서도 저 열유속 구간에서 온도가 급격히 감소하는 것을 확인할 수 있다. 이로 인해 온도 변화에 민감한 전자장비에 열충격이 발생할 수 있으므로, 이를 최대한 감소시키는 것이 중요하다. 두 번째, 임계 열유속 (critical heat flux, CHF)이 될 수 있으면 늦게 발생하도록 하는 지연이 필요하다. CHF는 고 열유속에서 생성된 증기막의 열저항으로 인해 표면 온도가 급격히 증가하는 열유속 지점을 의미한다. 높은 열저항으로 인해 표면 온도가 급격히 상승하므로, CHF를 최대한 지연시키는 것이 중요하다. 마지막으로, 열전달계수의 증가가 필요하다. 풀 비등에서의 열전달계수는 열유속을 과열도로 나눈 값으로, 이는 Fig. 1에 나타난 바와 같이 비등 곡선에서의 기울기를 의미한다. 따라서 열전달계수가 증가하면, 동일한 열유속에서 표면의 과열도가 감소하기 때문에 열전달계수를 최대한 증가시키는 것이 중요하다. 이러한 요소들을 고려하여 비등 열전달의 성능을 향상시키면, 다양한 냉각 및 열관리 분야에서의 활용 가능성을 더욱 높일 수 있다.
표면 개질 기술은 이러한 목표를 달성하기 위한 방법 중 하나로 연구되고 있다. 표면 개질을 통해 incipience excursion을 방지하고 CHF를 증가시킬 뿐만 아니라 열전달계수 또한 향상될 수 있다. 표면 개질법으로는 표면 거칠기 변화,(4),(5),(6) 마이크로 핀⋅채널(7),(8),(9) 등 많은 방법들이 연구되고 있다. 특히, 마이크로 다공성 구조로 표면을 개질하는 것은 비등을 촉진시키는 효과적인 방법 중 하나로 알려져 있다. 마이크로 다공성 구조는 넓은 표면적과 다수의 내부 기공으로 인해 여러 이점을 제공한다. 넓은 표면적은 열전달 면적을 증가시켜, 열이 더 효율적으로 전달될 수 있게 한다. 또한, 구조 내부의 기공들은 많은 핵 생성 지점 (nucleation sites)을 제공한다. 이 핵 생성 지점들은 비등 과정에서 기포가 형성되는 시작점 역할을 하며, 이를 통해 열전달 과정이 더욱 활발하고 효과적으로 일어날 수 있다. 이러한 특성 덕분에, 마이크로 다공성 구조는 incipience excursion을 감소시키는 동시에 열전달계수의 향상과 CHF의 지연에 기여한다.(10) 이러한 많은 장점으로 인해, 마이크로 다공성 구조를 활용한 다양한 선행 연구들이 진행되어 왔다. Bergles and Chyu(11)는 구리 분말 소결을 통해 44∼74 μm 의 입자 직경과 380 μm 의 두께를 갖는 마이크로 다공성 표면을 제작하였다. 물과 R-113을 작동 유체로 사용해 풀 비등 실험을 진행한 결과, 매끈한 표면에 비해 물에서는 최대 250 %, R-113에서는 최대 800 %의 열전달계수 향상을 보였다. 또한 incipience excursion도 두 경우 모두 급격히 감소함을 보였다. Jun et al.(12)은 구리 분말 소결을 통해 마이크로 다공성 표면을 제작하였고, 물을 작동유체로 풀 비등 실험을 진행했다. 그 결과 매끈한 표면에 비해 향상된 열전달계수와 CHF 를 보였고, 마이크로 다공성 코팅의 두께가 196 μm, 평균 입자 크기가 67 μm 일 때 가장 높은 열전달계수와 CHF를 보였다. Parker and El-Genk(13),(14)는 비전도성 유체인 HFE-7100 과 FC-72 내에서 마이크로 다공성 그라파이트의 풀 비등 열전달 성능을 측정하였다. HFE-7100 의 경우, 매끈한 구리 표면 보다 마이크로 다공성 그라파이트 표면의 열전달계수가 향상되었다. CHF는 과냉정도에 따라 60 % 까지 향상되었으며 incipience excursion은 감소하여 발생하지 않았다. FC-72의 경우, 매끈한 구리 표면에 비해 마이크로 다공성 그라파이트 표면의 열전달계수가 향상되었다. CHF는 과냉 정도에 따라 94 % 까지 향상되었으며 incipience excursion은 크게 감소하여 나타나지 않았다.
메탈폼은 마이크로 다공성 구조의 표면을 실용적으로 활용하기 위해서 효과적인 대안이 될 수 있다. 메탈폼은 셀 형태의 기공과 줄기 구조로 구성되어 있어, 큰 표면적과 많은 기공을 제공한다. 또한, 메탈폼은 구조적으로 강성이 높아 내구성이 우수하며, 저 비용으로 상용화된 제품들이 시장에 널리 보급되어 있어 접근성이 높다.(15) 메탈폼의 형상을 결정하는 주요 요소는 두께, PPI (pores per inch), 그리고 공극률 (porosity) 이 있다. PPI 는 1인치 당 기공의 개수, 공극률은 메탈폼의 전체 부피 대비 기공의 비율을 의미한다. 이러한 형상 요소들은 메탈폼의 열전달 특성에 직접적인 영향을 미친다. 따라서, 메탈폼의 장점을 활용하기 위해, 형상 요소들이 열전달 성능에 미치는 영향을 이해하는 것이 중요하기 때문에 이에 대한 연구들이 이루어지고 있다. Athreya et al.(16)은 FC-72 를 작동 유체로 사용하여 풀 비등에서 알루미늄 폼 두께의 영향에 대해서 연구하였다. 폼의 두께가 클 수록 열전달계수가 증가하였고, incipience excursion은 감소하였으며, 폼의 두께가 작을수록 CHF는 증가하였다. Xu et al.(17)은 grooved 메탈폼의 풀 비등 실험을 통해 두께, PPI 가 미치는 영향을 연구하였다. 2∼13 mm 두께, 20∼130 PPI 의 구리폼을 사용해 풀 비등 실험을 진행했으며 그 결과 PPI에 따라 열전달계수가 최대인 최적 폼 두께가 존재하였다. PPI 가 증가함에 따라 최적 두께는 감소했으며 이는 PPI 증가로 인해 기공의 직경이 감소하여 버블이 폼 내부에 정체되었고, 이 증기 버블들이 열전달을 방해했기 때문이라고 판단하였다. Manetti et al.(18)은 1∼3 mm의 두께를 가진 구리폼에 대해 풀 비등 실험을 진행하였다. 그 결과, 열유속별로 최대의 열전달계수를 가지는 최적 두께를 도출하였다. 특히 25 W/cm2 이상의 열유속에서는 최적 두께가 1 mm 보다 감소하였다. 폼의 두께 감소에 따라 버블 탈출 저항 또한 감소했고, 따라서 전도 열저항이 감소함과 동시에 증기막 형성이 방지되었다. 이로 인해, 그들은 열전달계수와 CHF 가 동시에 증가했다고 판단하였다. 또한, 매크로 두께의 메탈폼을 사용한 앞선 연구들은 분말 소결을 사용한 마이크로 다공성 표면에 비해 과열도가 최대 20K 이상으로 비교적 높은 경향을 보였다. 분말 소결을 사용한 마이크로 다공성 표면은 마이크로 두께만큼 코팅을 쌓아올리는 것과 달리 메탈폼은 주로 1 mm 보다 큰 두께를 사용하였다. 이 점이 메탈폼의 성능 향상을 방해하는 것으로 판단하여, Lim et al.(19)은 100∼500 μm 두께의 구리폼을 사용해 풀 비등 실험을 진행하였다. 두께별로 90, 130 PPI의 샘플을 사용했고, 그 결과 200 μm, 130 PPI 구리폼에서 과열도가 최대 5℃임을 보였다.
기존 연구를 통해 밝혀진 바에 따르면, 메탈폼 사용 시 버블 탈출 저항이 열전달 성능에 중요한 영향을 미치므로, 내부 버블로 인한 증기막 형성을 최소화하여 열저항을 줄이는 것이 중요함을 알 수 있었다. 이를 바탕으로, 기존 연구들은 주로 메탈폼의 PPI 변화가 버블 탈출 저항에 미치는 영향을 연구하였으며, 이는 최적 두께 결정에 중요한 요소임을 확인하였다. 또한, 메탈폼의 두께를 마이크로 두께까지 줄임으로써 풀 비등 열전달이 더욱 향상될 수 있음을 발견하였다. 그러나 메탈폼의 중요한 형상 요소인 공극률은 기존 연구에서 충분히 고려되지 않았으며, 대부분의 연구가 90∼100 %의 좁은 범위에 국한되었다. 공극률은 PPI와 함께 메탈폼의 기공 밀도와 크기에 직접적인 영향을 미치는 요소이다. 같은 PPI 에서 공극률이 높으면 기공의 크기가 커지고, 낮으면 기공의 크기가 작아진다. 공극률의 변화는 메탈폼의 버블 탈출 저항에 영향을 미치며, 이는 비등 열전달 성능을 결정하는 중요한 요소이다. 또한, 공극률이 낮으면 메탈폼의 전체 부피 대비 기공의 비율이 적으므로, 전도열전달에 유리할 수 있기 때문에 공극률 90 % 이하에서의 열전달 특성과 성능에 대한 최적화가 필요하다.
따라서 본 연구에서는 이러한 공극률의 중요성을 인식하고, 우수한 비등 열전달 성능이 예상되는 마이크로 두께 구리폼을 활용하여 공극률 변화가 비등 열전달 성능과 특성에 미치는 영향을 분석하였다. 이를 통해, 마이크로 두께 구리폼의 비등 열전달 향상 가능성과, 공극률에 따른 비등 열전달 성능의 변화 및 구리폼에서의 비등 메커니즘을 확인할 수 있었다. 이러한 연구 결과는 비등 촉진을 위한 마이크로 두께 구리폼의 효과적인 사용 방향성을 제시하는 데 기여할 것으로 기대된다.
2. 실험 방법
2.1 풀 비등 실험 시편
본 실험에서는 서로 다른 공극률 (85 %, 68 %, 54 %)을 갖는 구리폼을 사용하였다. 각 구리폼의 두께는 Lim et al.(19)의 결과를 참고하여 열전달계수가 가장 높은 것으로 확인된 200 μm 로 설정되었다. 또한, 공극률 85 %과 68 % 구리폼은 상용품을 구매하여 사용하였으나, 54 % 의 공극률의 구리폼은 기존의 2000 μm 구리폼을 200 μm 로 압축하여 제작하였다. 각 구리폼의 부피와 질량을 측정하여 식 (1)에 따라 공극률을 계산하였고, 광학 현미경을 사용하여 Fig. 2에 각 공극률별 구리폼의 형상을 나타내었다.
(1) |
열유속을 구리폼에 공급하기 위해 Fig. 3(a) 와 같은 방식으로 실험 장치를 구성하였다. 구리폼과 세라믹 히터 결합 및 열전대 부착을 위해 10 × 10 × 5 mm3 크기의 직육면체 구리 블록을 사용하였다. 구리폼은 10 × 10 mm2 크기로 절단되어, Fig. 3(b)와 같이 구리 블록 윗면에 소결을 통해 부착되었다. 이 소결 과정은 1040℃ 의 진공로에서 1시간 동안 진행되었다. 구리 블록의 아랫면에는 10 × 10 mm2 크기의 세라믹 히터가 납땜을 통해 부착되었고, 이를 통해 일정한 열유속을 공급하면서 풀 비등 열전달 실험을 진행하였다. 세라믹 히터 주변부는 에폭시와 유리섬유로 단열 처리하여 표면 방향으로의 1차원 전도 열전달 조건이 유지되도록 하였다. 구리 블록 중앙에 부착된 열전대를 통해 온도를 측정하였으며, 이 데이터는 1차원 전도 열전달 식을 이용하여 표면 온도를 계산하는 데 사용되었다. 구리 블록은 Fig. 3(c)와 같이 에폭시를 통해 PEEK 재질의 홀더와 결합되었다. 실험 진행 전, 부착된 구리폼은 증류수와 IPA, 염산(3 %)을 통해 순차적으로 세척되었고, 이후 홀더와 챔버가 결합되었다.
2.2 풀 비등 실험 장치
풀 비등 실험과 이를 통한 열성능 측정 및 가시화를 위해 Fig. 4 와 같이 실험 장치를 구성하였다. 전체 실험 장치는 풀 비등 실험 챔버, 가시화 장치, 전원공급장치, 데이터 취득 장치로 구성되어 있다. 풀 비등 실험 챔버는 0.25 W/m⋅K의 열전도율을 가지는 PEEK 재질로 제작하였으며, 150 × 120 × 185 mm3 의 크기와 20 mm의 벽 두께를 갖는다. 따라서 풀 비등 실험 챔버는 작동유체에 공급된 열량이 외부로 유출되지 않도록 단열되었다. 구리폼과 홀더는 풀 비등 챔버의 중앙에 설치하였고, 챔버에 설치된 유리창을 통해 가시화 할 수 있다. 또한, 구리폼과 홀더를 카트리지 히터보다 높은 위치에 배치하여 작동유체를 가열할 때, 히터의 위치로 인한 작동유체 대류 유동 영향을 최소화 할 수 있도록 하였다. 작동 유체와 실험 시편의 온도를 측정하기 위해서 T형 열전대 (Omega Engineering, Inc)를 사용하였고, 챔버 내부 압력 측정을 위해서 압력계 (Omega Engineering, Inc) 를 설치하였다. 또한 시편의 열유속 공급과 작동유체의 포화온도를 일정하게 유지하기 위해 각 두 대의 전원공급기(N8741A & N8952A, Keysight Technologies Inc) 를 사용하였다. 온도와 챔버 내부 압력, 인가 전압 데이터 취득을 위해서는 두 대의 DAQ (FD-11614, National Instrument Inc & DAQ970A, Keysight Technologies Inc)를 사용하였고, 인가 전류 측정을 위해서 디지털 멀티미터 (34461A, Keysight Technologies Inc)를 사용하였다. 위 장치들은 LabVIEW 소프트웨어를 통해 연결되어 온도, 내부 압력, 인가 전압 및 인가 전류 데이터를 실시간으로 취득 및 확인하였다.
2.3 데이터 처리 및 불확도 분석
비등이 발생하는 표면온도 Tw는 Th, k, q″,L을 통해 식 (2)로 계산할 수 있다. Th는 구리 블록에 부착된 열전대의 온도이고, k는 구리의 열전도율, q″는 세라믹 히터에서 공급한 열유속, L은 온도 측정 지점과 표면 사이의 거리이다.
(2) |
비등 표면의 면적과 세라믹 히터의 면적이 같고, 히터의 주변부가 단열되어있으므로 구리 표면 방향으로 1차원 전도열전달을 가정하였다. 열전달계수 h는 뉴턴의 냉각법칙인 식(3)에 따라 공급된 열유속 q″와 과열도 ΔTsat로 계산하였다.
(3) |
본 실험의 측정불확도는 국제표준화기구(International Organization for Standardization, ISO)의 측정불확도 표현 지침(20)에 따라, 식 (4)∼(6)을 통해 계산되었다.
(4) |
(5) |
(6) |
과열도와 열전달계수 및 기타 변수들(전압, 전류, 전력, 열유속)에 대한 불확도를 Table. 1에 정리하였다. 열전달계수에 대한 최소 및 최대 상대 불확도는 각 2.77, 15.79 % 이었다. 열전달계수의 최대 불확도는 저 열유속구간에서 발생하였지만, 5 W/cm2 이상의 열유속에서는 열전달계수의 상대 불확도가 10 % 미만임을 알 수 있었다.
2.4 풀 비등 실험 과정
본 실험은 대기압 하의 포화상태 물을 작동유체로 사용하여 실험하였다. 실험 진행 전 작동유체를 풀 비등 실험 챔버에서 1시간 동안 끓여 챔버 내부의 작동유체에 잔존하는 불응축 가스를 제거하였다. 열원으로 사용된 세라믹 히터에는 전원공급기를 통해 단계적으로 열량을 증가시키며 실험을 진행하였다. 구리 블록 내부 열전대의 측정 온도 편차가 0.1℃ 이하일 때, 풀 비등 실험의 정상상태 (steady state) 온도가 수렴한 것으로 간주하고, 다음 단계로 진행하기 위해 일정량의 열유속을 증가시켰다. CHF에 도달한 후 표면 온도가 급격히 증가하여 히터 접합부의 온도가 150℃ (히터의 한계 온도)에 도달할 때 열량 공급을 중단하였다. 열량의 증가량은 0∼5 W 범위에서는 0.5 W, 5∼20 W 범위에서는 1 W, 20∼100 W 범위에서는 2.5 W, 100∼200 W 범위에서는 5 W, 200∼W 범위에서는 2.5 W 씩 증가시키면서 실험을 진행하였다. 풀 비등 실험 과정 중에는 작동유체의 하부, 상부, 증기의 온도를 측정하여 풀 비등 챔버 내부의 작동유체 온도가 균일한지 확인하였다. 풀 비등 챔버를 밀폐 상태로 유지하면서 내부 압력을 압력계로 측정하였으며, 측정된 압력값이 1기압의 포화상태를 일정하게 유지할 수 있도록 내부 응축 코일에 공급되는 유량을 적절하게 제어하였다.
3. 결과 및 토론
3.1 풀 비등 곡선
구리폼의 풀 비등 실험에 앞서 평균 거칠기 (Ra) 가 0.03 μm 인 매끄러운 구리 표면에서 풀 비등 실험을 먼저 진행하여 풀 비등 실험의 정확성을 검증하였다. 그 결과, Rohsenow의 상관식(21)을 기준으로 했을 때 Fig. 5와 같이 실험 결과와 상관식의 그래프가 일치함을 확인하였다. 일반적으로, Rohsenow의 상관식은 온도에 대해서 ±4.6 %의 오차를 보인다.(22) 오차가 4.6 % 이내인 실험 데이터는, Sample #1의 경우, 열유속 범위 10∼60 W의 온도 데이터이고, Sample #2의 경우, 열유속 범위 25∼60 W의 온도 데이터이다. 저 열유속에서는 Sample #1의 온도는 최대 11 %의 오차를 보였고, Sample #2의 온도는 최대 41 %의 오차를 나타내었다. 60 W 이상의 고 열유속에서는 CHF에 도달하여 오차가 크게 발생하였다.
구리폼의 비등 곡선과 열전달계수 분포는 각각 Fig. 6(a)와 Fig. 6(b)에 나타내었다. 매끈한 표면에서의 풀 비등 실험 결과와 비교했을 때, 구리폼의 CHF 가 증가되고 과열도가 감소하는 결과를 보였다. 가장 높은 열전달계수를 가진 공극률 68 % 구리폼에서는 50 W/cm2에서 5.22℃로 측정되었으며, CHF 의 경우 공극률 85 % 구리폼에서 237.5 W/cm2 로 나타났다. 반면에 매끈한 표면은 50 W/cm2에서 15.53℃의 과열도를 보였고, CHF 는 82 W/cm2 로 측정되었다. 따라서, 구리폼이 매끈한 표면에 비해 비등 열전달 성능 측면에서 현저히 향상되었음을 확인하였다. 다른 공극률의 구리폼과 서로 비교했을 때는 열유속 구간에 따라 과열도, 즉 열전달계수의 양상이 변화하였다. 50 W/cm2 이하의 열유속에서 공극률 54 %, 68 % 구리폼은 비슷한 경향을 보였지만, 공극률 85 % 구리폼은 상대적으로 낮은 열전달계수를 보였다. 열유속 20 W/cm2 에서는 공극률 54 % 구리폼의 열전달계수가 47.0 kW/m2⋅K, 68 % 구리폼은 51.2 kW/m2⋅K로, 큰 차이가 없었지만, 공극률 85 % 구리폼은 27.4 kW/m2⋅K로 비교적 낮은 열전달계수를 보였다. 50 W/cm2 보다 높은 열유속 구간에서는 공극률 68 % 구리폼의 열전달계수가 가장 크게 상승하였으며, 85 % 공극률의 구리폼은 가장 낮은 열전달계수를 보였다. 실제로, 100 W/cm2 에서 공극률 68 % 구리폼의 열전달계수는 165.6 kW/m2⋅K로, 공극률 54 % 구리폼의 열전달계수인 126.5 kW/m2⋅K와 1.3배 이상 차이를 보였다. CHF의 경우 공극률 54 % 구리폼에서 170 W/cm2, 공극률 68 % 구리폼에서 205 W/cm2, 공극률 85 % 구리폼에서 237.5 W/cm2 의 값을 가졌다. 이에 따라, Fig. 7과 같이 공극률 증가에 따라 열전달계수는 증가 후 감소, CHF는 증가하는 경향을 나타내었다.
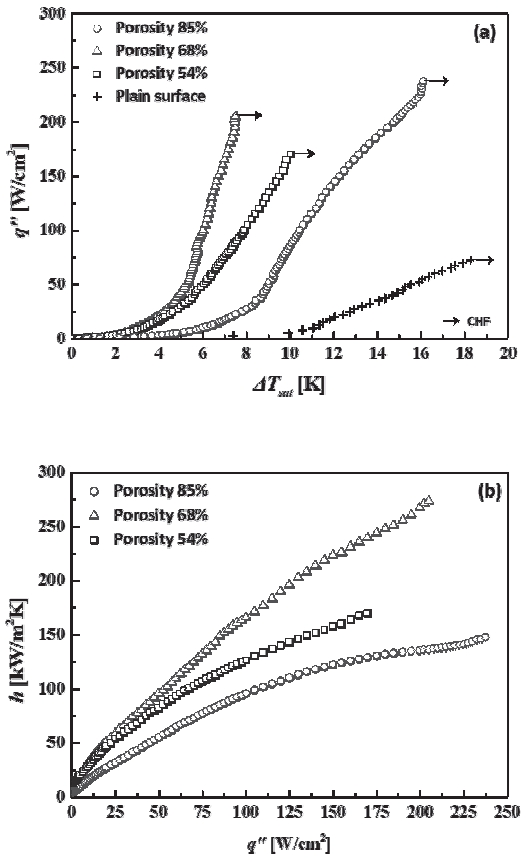
Pool boiling performance of micro-thick metallic foam with different porosity. (a) Plot of heat flux against wall superheat and (b) heat transfer coefficient against heat flux
이와 같은 경향은 구리폼의 공극률 변화에 따른 전도 열전달의 변화 및 버블의 내부 거동 변화 때문으로 추정되었다. 공극률이 증가한다면 내부 구리의 체적이 감소하여, 가열면으로부터의 전도 열전달이 저하된다. 이러한 현상은 비등을 통한 열전달이 활발하지 않은 저 열유속에서 두드러지게 나타난 것으로 확인하였다. 반면, 공극률의 증가는 내부 기공 체적의 확대를 의미하며, 이것은 버블의 원활한 방출을 촉진한다. 이로 인해 버블이 내부 구조에 갇혀 열저항을 형성하지 않고 원활히 탈출하게 되는데, 이는 비등이 활발히 일어나는 고 열유속 열전달 성능 향상에 지배적인 것으로 판단할 수 있다. 따라서 공극률 변화에 따른 열전달 특성 변화에 대한 입증을 위해 다음 절에서 비등 가시화 영상을 분석하였다.
3.2 비등 가시화 및 토의
풀 비등 실험과 동시에 초고속 카메라를 사용해 풀 비등이 발생할 때의 가시화를 진행하였고, 이를 통해 구리폼의 공극률에 따른 풀 비등 열전달 특성을 확인할 수 있었다. 특히, 공극률 85 %의 구리폼은 저 열유속 구간에서부터 다른 샘플들과 열전달계수에서 차이를 보였다. 이 차이의 원인을 알아보기 위해, 저 열유속 구간인 1 W/cm2 에서 각 공극률별 가시화 결과를 비교하여 Fig. 8에 나타내었다. 그 결과, 모든 구리폼의 비등이 시작되었지만 공극률 85 %의 구리폼에서의 버블 생성 및 비등이 상대적으로 덜 활발하다는 것을 확인할 수 있었다. 관련 선행 연구인 Xu et al.(22)의 실험 결과에서는, 40 PPI, 두께 7 mm, 공극률 90, 95, 98 %의 구리폼이 공극률 증가에 따라 열전달계수가 감소한 것으로 보고하였다. 그들은 공극률 증가에 따른 구리폼의 단면적 감소를 열전달계수 감소의 원인으로 보았다. 마찬가지로, 공극률 85 %의 구리폼은 다른 구리폼에 비해 기공의 크기가 크고, 단면적이 작다. 따라서 본 실험에서도, 공극률이 증가할수록 전도열전달의 효과는 감소하고, 이것은 비등이 지배적이지 않은 저 열유속에서 공극률 85 % 구리폼의 열전달 성능을 감소시키는 원인이 될 수 있음을 확인하였다.

High-speed visualization of bubble nucleation of porosity (a) 54%, (b) 68%, (c) 85% copper foam at 1 W/cm2
앞의 Fig. 6에 나타난 바와 같이 공극률 54 %와 68 % 구리폼의 열전달계수는 50 W/cm2 이후 부터 유의미한 차이를 보였다. 이 차이를 분석하기 위해, 50 W/cm2 에서 54 % 와 68 % 공극률을 가진 구리폼의 비등 현상을 초고속 카메라로 1ms 간격으로 촬영하였으며, 이를 Fig. 9 에 나타내었다. 각 화살표는 구리폼 측면의 버블 발생 지점을 가리키며 각 지점에서의 버블 생성 주기를 분석하였다. Fig. 9(a)의 공극률 54 % 구리폼에서는 생성된 버블들이 5 ms의 시간동안 탈출하지 못한 채 성장만 했음을 확인할 수 있었다. 반면, Fig. 9(b)의 공극률 68 % 구리폼에서는 생성된 버블들이 5 ms의 시간 동안 탈출 및 재성장한 것을 확인할 수 있었다. 이를 통해, 공극률 68 % 구리폼은 공극률 54 % 구리폼에 비해 버블 생성, 성장 및 탈출의 주기가 짧은 것을 확인하였다. 이는 공극률 54 % 구리폼은 발생한 버블이 내부 구조의 방해로 탈출이 어렵고, 공극률 68 % 구리폼에 비해 버블이 성장할 수 있는 기공이 적기 때문인 것으로 판단할 수 있다. 저 열유속인 1 W/cm2 에서와 달리, 50 W/cm2 에서는 비등이 더 활발하게 발달하였으며, 이로 인해 발생하는 버블의 양도 상대적으로 많아졌다. 이러한 상황에서는 전도 열전달 보다 비등을 통한 열전달이 더욱 중요한 역할을 하게 되며, 이는 공극률 68 % 구리폼에서 비등이 더 활발하게 발생하도록 하여 결국에는 열전달계수의 증가를 가져온다.
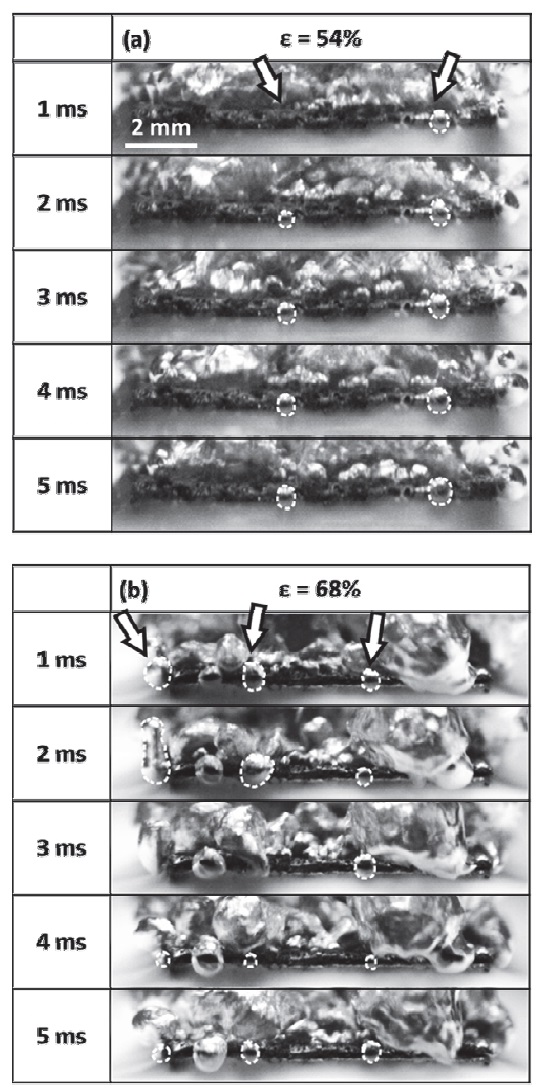
High-speed visualization of nucleation boiling of porosity (a) 54%, (b) 68% captured at 50 W/cm2 with 1 ms interval
위 결과들을 바탕으로 열유속과 공극률에 따른 비등 열전달 거동을 Fig. 10 에 스케치하여 나타내었다. 공극률이 낮을수록 구리폼의 단면적이 크기 때문에 전도열전달에는 용이하지만, 버블 탈출에는 불리하다. 반면, 공극률이 높은 경우에는 구리폼 내부의 기공의 크기가 증가하여 전도열전달은 덜 효과적이지만, 버블의 탈출이 용이해져 비등 열전달에 보다 유리한 조건을 제공한다. 저 열유속에서는 비등이 활발하지 않고, 전도 열전달이 지배적이므로 공극률이 낮은 구리폼 샘플이 열전달에 유리하였다. 비등이 진행될수록 전도 열전달보다 버블 탈출 저항이 지배적이므로 공극률이 높은 구리폼 샘플이 열전달에 유리함을 확인할 수 있었다. 열유속이 CHF 에 접근함에 따라, 구리폼 내부는 증기로 가득 차게 되며, 이로 인해 버블의 탈출 저항만이 열전달에 주요한 영향을 미치게 된다. 따라서 공극률 증가에 따라 버블 탈출 저항이 감소하였고 따라서 CHF가 증가한 것으로 판단하였다.
4. 결 론
본 연구에서는 열전달 성능이 우수할 것으로 예상되는 마이크로 두께의 구리폼과 더불어, 기존 연구들에서 시도하지 않았던 구리폼의 공극률이 비등 열전달 성능에 미치는 영향을 실험적으로 연구하였다. 실험 결과를 통해 공극률은 마이크로 두께 구리폼의 열전달 성능에 중요한 영향을 미친다는 것을 확인하였다. 이후 실험 결과 분석 및 유동 가시화를 통해 마이크로 두께 구리폼의 풀 비등 특성과 공극률에 따른 비등 열전달 변화를 확인하였다. 이를 통해 마이크로 두께 구리폼의 비등 열전달 성능 향상을 위해 적절한 공극률을 선택하는 것이 중요함을 알 수 있었다. 주요 결론은 다음과 같다.
- 1) 마이크로 두께의 구리폼 중 가장 풀비등 성능이 우수한 것으로 알려진 200 μm 두께의 구리폼을 선정하여, 공극률 54, 68, 85 %의 경우에 대해서 풀비등 실험을 진행하였다.
- 2) 최대 열전달계수의 경우 모든 열유속 구간에서 공극률 68 %일 때 가장 높은 237.6 kW/m2⋅K, 85 %의 경우 가장 낮은 144.2 kW/m2⋅K였다. CHF의 경우 공극률 증가에 따라 증가했으며 공극률 85 %일 때 가장 높은 237.5 W/cm2, 54 %일 때 가장 낮은 174.7 W/cm2 인 것으로 나타났다.
- 3) 가시화 분석 결과, 공극률의 증가에 따라 구리폼 내부 기공의 부피가 증가하므로 버블의 탈출이 원활하다는 것을 확인하였다. 따라서, 공극률 증가에 따라 버블 탈출 저항이 증가하였다. 또한, 공극률 증가에 따라 단면적이 감소하므로 전도열전달 성능은 감소하는 것을 확인하였다.
- 4) 실험 결과 및 가시화 분석 결과를 토대로, 다음과 같이 공극률과 열유속 범위에 따른 비등 열전달 메커니즘을 파악할 수 있었다. 저 열유속에서는 전도 열전달이 지배적이기 때문에 공극률이 낮은 구리폼이 높은 열전달계수가 가짐을 알 수 있다. 고 열유속에서는 버블 탈출 저항의 영향도 무시할 수 없기 때문에, 공극률이 중간치인 구리폼이 열전달계수 측면에서 유리한 것으로 판단하였다. 또한, CHF에 도달한다면 버블 탈출 저항의 영향이 매우 크기 때문에 공극률 증가에 따라 CHF가 증가하였음을 알 수 있다.
5. 후 기
이 성과는 정부(과학기술정보통신부)의 재원으로 한국연구재단의 지원을 받아 수행된 연구임(No. 2020R1A2C3008689).
References
- Zhang, Zhihao, Xuehui Wang, and Yuying Yan, 2021, “A Review of the State-of-the-Art in Electronic Cooling,” E-Prime - Advances in Electrical Engineering, Electronics and Energy, Vol. 1, 100009.
- Mudawar, I, 2001, “Assessment of High-Heat-Flux Thermal Management Schemes,” IEEE Transactions on Components and Packaging Technologies 24, no. 2, pp. 122-141.
- Liang, Gangtao, and Issam Mudawar, 2019, “Review of Pool Boiling Enhancement by Surface Modification,” International Journal of Heat and Mass Transfer, Vol. 128, pp. 892-933.
- Jones, Benjamin J., John P. McHale, and Suresh V. Garimella, 2009, “The Influence of Surface Roughness on Nucleate Pool Boiling Heat Transfer,” Journal of Heat Transfer, Vol. 131, No. 12, 121009.
- Kim, Jin S., Adam Girard, Seongchul Jun, Jungho Lee, and Seung M. You, 2018, “Effect of Surface Roughness on Pool Boiling Heat Transfer of Water on Hydrophobic Surfaces,” International Journal of Heat and Mass Transfer, Vol. 118, pp. 802-811.
- Dhadda, Gurpyar, Mohamed Hamed, and Philip Koshy, 2021, “Electrical Discharge Surface Texturing for Enhanced Pool Boiling Heat Transfer,” Journal of Materials Processing Technology, Vol. 293, 117083.
- Chu, Kuang-Han, Ryan Enright, and Evelyn N. Wang, 2012, “Structured Surfaces for Enhanced Pool Boiling Heat Transfer,” Applied Physics Letters, Vol. 100, No. 24, 241603.
- Kwak, Ho Jae, Jin Hyun Kim, Byung-Soo Myung, Moo Hwan Kim, and Dong Eok Kim, 2018, “Behavior of Pool Boiling Heat Transfer and Critical Heat Flux on High Aspect-Ratio Microchannels,” International Journal of Thermal Sciences, Vol. 125, pp. 111-120.
- Pastuszko, Robert, Robert Kaniowski, and Tadeusz M. Wojcik, 2020, “Comparison of Pool Boiling Performance for Plain Micro-Fins and Micro-Fins with a Porous Layer,” Applied Thermal Engineering, Vol. 166, 114658.
- Sarangi, Suchismita, Justin A. Weibel, and Suresh V. Garimella, 2015, “Effect of Particle Size on Surface-Coating Enhancement of Pool Boiling Heat Transfer,” International Journal of Heat and Mass Transfer, Vol. 81, pp. 103-113.
- Bergles, A. E., and M. C. Chyu, 1982, “Characteristics of Nucleate Pool Boiling From Porous Metallic Coatings,” Journal of Heat Transfer, Vol. 104, No. 2, pp. 279-285.
- Jun, Seongchul, Jinsub Kim, Donggun Son, Hwan Yeol Kim, and Seung M. You, 2016, “Enhancement of Pool Boiling Heat Transfer in Water Using Sintered Copper Microporous Coatings,” Nuclear Engineering and Technology, Vol. 48, No. 4, pp. 932-940.
- El-Genk, Mohamed S., and Jack L. Parker, 2005, “Enhanced Boiling of HFE-7100 Dielectric Liquid on Porous Graphite,” Energy Conversion and Management, Vol. 46, No. 15–16, pp. 2455-2481.
- Parker, Jack L., and Mohamed S. El-Genk, 2005, “Enhanced Saturation and Subcooled Boiling of FC-72 Dielectric Liquid,” International Journal of Heat and Mass Transfer, Vol. 48, No. 18, pp. 3736-3752.
- Zhao, C.Y., 2012, “Review on Thermal Transport in High Porosity Cellular Metal Foams with Open Cells,” International Journal of Heat and Mass Transfer, Vol. 55, No. 13–14, pp. 3618-3632.
- Athreya, Badrinarayan, Roop Mahajan, and Subham Sett, 2002, “Pool Boiling of FC-72 over Metal Foams: Effect of Foam Orientation and Geometry,” 8th AIAA/ASME Joint Thermophysics and Heat Transfer Conference, St. Louis, Missouri, AIAA 2002-3214.
- Xu, Z.G., Z.G. Qu, C.Y. Zhao, and W.Q. Tao, 2011, “Pool Boiling Heat Transfer on Open-Celled Metallic Foam Sintered Surface under Saturation Condition.” International Journal of Heat and Mass Transfer, Vol. 54, No. 17–18, pp. 3856-3867.
- Manetti, Leonardo Lachi, Ana Sofia Oliveira Henriques Moita, Reinaldo Rodrigues de Souza, and Elaine Maria Cardoso, 2020, “Effect of Copper Foam Thicknes on Pool Boiling Heat Transfer of HFE-7100,” International Journal of Heat and Mass Transfer, Vol. 152, 119547.
- Lim, Hyunmuk, Su-Yoon Doh, Junyoung Choi, Jungchan Moc, Seung M. You, and Jungho Lee, 2024, “Pool Boiling Heat Transfer Enhancement Using the Micro-Thick Metallic Foam Surface in Saturated Water,” International Communications in Heat and Mass Transfer, Vol. 152, 107310.
- ISO, 1995, “Guide to the Expression of Uncertainty in Measurement”, Geneva, Switzerland, Vol. 122.
- Rohsenow, W. M., 1952, “A Method of Correlating Heat-Transfer Data for Surface Boiling of Liquids,” Journal of Fluids Engineering, Vol. 74, No. 6, pp. 969-975.
- Adrienne S. Lavine, Frank P. Incropera, David P. DeWitt, Theodore L. Bergman, 2017, Incropera’s Principles of Heat and Mass Transfer, John Wiley & Sons, New York.
- Xu, Z.G., Z.G. Qu, C.Y. Zhao, and W.Q. Tao., 2014, “Experimental Correlation for Pool Boiling Heat Transfer on Metallic Foam Surface and Bubble Cluster Growth Behavior on Grooved Array Foam Surface,” International Journal of Heat and Mass Transfer, Vol. 77, pp. 1169-1182.