
Performance Test and Aerodynamic Design on the High Pressure Ratio Centrifugal Compressor of a Turbocharger
It is necessary to design a compressor with high pressure ratio that satisfies the IMO(international maritime organization) NOx emission regulation for the marine diesel engine. Impeller was designed using the modified slip factor with the flow coefficient. The main purpose of this study is to investigate the sensitivity of the compressor performance by the vaned diffuser geometries. The first vaned diffuser type was based on a NACA airfoil, the second was channel diffuser, and the third was conformally transformated configuration of a NACA65(4A10)06 airfoil. The sensitivity of the performance was calculated using a commercial CFD program for three different diffuser geometries. The channel diffuser showed the wide range of operation and higher pressure characteristics, comparing with the others. This is attributed to the flow stability at diffuser. Combined with this results with impeller design, the optimized compressor was designed and verified by the test results.
Keywords:
Diesel engine turbocharger, Mean-line prediction, Diffuser, Pressure recovery coeff., Pressure loss coeff., 디젤 엔진 터보차져, 평균 유선법, 디퓨저, 압력 회복계수, 압력 손실계수1. 서 론
2011년부터 IMO(국제해사기구)의 강화된 NOx(기존 대비 20% 저감, Tier II) 환경규제에 따라 선박용 중속 디젤엔진은 흡기밸브의 닫힘 시기를 종래보다 빠르게 하는 Miller timing을 적용함으로써 엔진내부의 최고온도를 낮추어 NOx 발생량을 저감하는 방식을 채택하고 있다. 이 방법에서는 흡기밸브가 열려 있는 시간이 단축되므로 기존 압력비(약 4.3)의 터보차져로는 엔진에서 필요로 하는 공기량을 공급할 수 없게 된다.
따라서 터보차져는 기존과 동일한 공기량을 공급하기 위해 고압력비(4.65 이상)의 사양이 요구되고 있다. 당사에서 요구되는 터보차져 압축기의 설계사양은 Table 1과 같다.
대형 터보차져의 경우에는 일반적으로 압축기의 효율이 85%이지만 고압력비의 중형 터보차져의 경우에는 현재 가장 경쟁력 있는 선진사 기준으로 최대효율을 설정하였다. 안정적인 운전영역 확보를 위하여 요구되는 서지마진은 13 % 이상이다. 2016년부터는 NOx 규정(기존대비 80 % 저감, Tier III)이 더욱 엄격해짐에 따라 약 7~8 수준에 달하는 고압력비를 요구하고 있다. 하지만 1단으로는 고압력비를 실현하는데 있어서 구조적 한계가 있으므로 2단의 터보차져를 적용하는 연구가 진행되고 있으며(ABB사, Warsilar사) 1단으로는 티타늄 합금이 간혹 적용되기도 하지만 비용증가로 대량생산하기는 힘들다.(BorgWarner사) 또한, 고압력비는 터보형에서는 보통 축류형에 적용되므로 원심형의 압축기에 대한 논문 및 자료는 거의 없는 실정이다. 본 논문에서는 고압력비의 원심압축기 설계를 수행하고 시험으로 검증한 방법을 소개하고자 한다.
압력비를 증가시키는 일반적인 방법은 임펠러의 회전수를 증가 또는 출구직경을 증가시키는 것이지만 소재의 허용응력이 존재하므로 구조강도상의 한계에 직면하게 되므로 적절한 절충점을 찾아야 한다. 본 연구에서는 기존 알루미늄 합금강의 소재를 변경하지 않고 50,000 시간의 내구수명을 보증하는 것을 기준으로 하여 회전수와 날개 수, 출구직경을 검토하였다. 5.0 이상의 고압력비에서 운전되는 경우에는 최대응력이 급격히 증가하게 되므로 이를 방지하기 위한 임펠러 후면 냉각설계가 적용되었으며 특허로 등록된 상태이다. 고압력비뿐만 아니라 고효율(80 %)의 압축기를 설계하기 위하여 디퓨저의 형상(NACA, modified airfoil, Channel type), 입구직경, 출구직경을 변수로 최적 매칭설계가 적용되었다.
최적 설계된 압축기의 성능을 검증하기 위하여 압축기, 연소기, 터빈으로 구성된 터보차져 시운전 설비를 구축하여 실제 엔진의 운전조건을 만들어 시험하였으며 시험결과로부터 설계된 압축기의 성능을 만족하는 결과를 확인하였으며 설계방법의 타당성을 검증하였다.
2. 임펠러 설계
유량을 결정하는 인듀서 팁반경의 설계는 상대 마하수가 소재의 구조․진동 한계값(본 연구에서는 1.2로 설정)을 넘지 않도록 설계하였으며 임펠러 출구 설계는 단순한 출구각도 및 날개수의 함수인 종래의 Wiesner 방정식 대신 회전수와 유량의 함수를 반영하여 탈설계점에서도 예측이 실제와 가깝도록 식 (1)과 같이 적용하였다. 식 (1)에서 슬립계수(slip factor)는 출구각도(β2b), 날개 수(Zb), 유량계수(Φ2 =Cm2/U2)로 구성되어 있다.(1)~(4)
Fig. 1은 압력비에 따른 압축기 기본 형상 설계 시 초기값으로 적용되는 압축기 부품 각 위치에서의 절대 마하수(임펠러 입구는 상대 마하수)를 본 연구를 통하여 설계 표준화한 결과이다. 위 그래프는 다양한 실험값으로 검증된 값으로서 누구나 쉽게 고효율에 가까운 압축기의 초기 설계 시 매우 유용하게 적용할 수 있다. 본 연구에서 설계점에서의 임펠러후향 출구각은 원주방향기준으로 65°이며 서지 마진을 고려한 디퓨저 입구의 incidence angle은 -4°를 적용하였다.
임펠러의 3차원 형상설계를 위해서 Fig. 2와 같이 우선 허브와 슈라우드의 회전면인 2차원 곡선을 반경방향과 축방향으로 구성된 자오면(meridional plane)상에서 6차 베지어 곡선(Bezier curve)을 사용하였으며 엑셀에서 날개각도와 두께가 동시에 반영되어 설계치수변화 및 각도변화에 따른 3차원 형상이 실시간으로 도출되게 하였다. 임펠러 설계에서 고압력비를 실현하기 위하여 splitter를 포함하여 날개 수는 16∼18개에서 검토되었고 출구직경의 변화에 따른 압력비 및 효율변화를 살펴보았다. 자오면상의 2차원 형상을 기반으로 캠버(camber)선을 정의하기 위하여 자오면상에서 주요 유동 방향을 따르는 좌표를 m(meridional direction)이라고 하고 이 때 m과 블레이드의 캠버선과의 사이각을 다음 식(2)와 같이 블레이드 각(β)으로 정의한다.
Fig. 3, 4는 자오면 기준으로 임펠러의 캠버각과 날개각을 식(2)와 같이 정의하였고 Fig. 5에서는 날개두께를 정의함으로서 Fig. 6과 같은 3차원 형상을 도출하였다.
3. 디퓨저 설계
임펠러 설계와 더불어 고압력비 및 고효율을 설계하기 위해서는 디퓨저의 설계가 매우 중요하다. 즉 임펠러 출구의 운동 에너지는 동력의 30~50 %에 달하므로 이를 디퓨저에서 어떻게 압력 에너지로 회수하는 가에 따라 효율 및 서지마진이 많이 달라지게 된다. 본 논문에서는 디퓨저 입구비(=베인 디퓨저 입구직경/임펠러 출구직경), 출구비(=베인 디퓨저 출구직경/임펠러 출구직경) 및 베인 디퓨저 형상변경(modified airfoil, channel diffuser, NACA65-4A10-06)을 주요 변수로 하여 성능특성을 살펴보았다.(Fig. 7 참조) 민감변수 중 하나인 디퓨저 입구각도는 설계점을 기준으로 영각(incidence angle)을 -4°로 설정하였다.(5)∼(6)
4. 케이싱 설계
케이싱 설계는 임펠러와 디퓨저에 비해 상대적으로 중요도가 낮아 설계시 간단하게 접근하는 경우가 많은데 디퓨저 출구직경과 각도 등은 서지발생과 압력손실에 민감하므로 세심한 주의가 필요하다. 최근에는 이차유동손실이 큰 대칭형보다는 효율이 좋은 overhung 타입으로 설계가 이루어진다.(2)
Fig. 8과 같이 설계의 자동화를 위해 아래 6개의 독립변수(r1, r2, θ2, I, L, d, w는 디퓨저 폭)로 식 (3)과 같이 케이싱 각도별 단면적이 계산되며 엑셀프로그램과 3차원 캐드 프로그램에서 자동 연동화시켰으며 이로부터 Fig. 9와 같은 케이싱 형상이 도출되었다.
5. 유동해석 경계조건
3차원 유동해석에서는 임펠러와 디퓨저의 설계 타당성을 시험 전에 미리 검증하고 내부 유동특성을 분석함으로서 문제점 및 개선대상을 파악하여 제작의 시행착오를 줄이고자 실시하였다. 유동해석에서 격자수는 격자 수 검증을 통하여 최소 격자수를 결정하였다. 임펠러는 약 190,000개, 디퓨저는 약 70,000여개로 설정하였으며 상용 프로그램인 CFX를 사용하였다.
Fig. 10에서는 유동해석을 하기 위하여 모델링된 압축기를 보여주고 있으며 Table 2에서는 지배방정식과 경계조건을 나타내고 있다. 본 해석에서 입구는 총압력, 총온도를 주었고 출구조건에서 압력조건 대신 질량유량 조건을 설정하였다. 임펠러와 베인 디퓨저 사이의 인터페이스에서는 임펠러 출구에서 발생된 제트형 웨이크가 베인 디퓨저쪽으로 전달되는 효과 등을 반영하는 Frozen rotor 기법을 적용하였다.
6. 성능시험
설계 및 유동해석의 결과를 실험값과 비교하기 위해서 Fig. 11과 같은 터보차져 전용 시운전 설비에서 성능을 계측하였다. 시험방법은 다음과 같다. 약 7 bar의 시동용 압축 탱크의 밸브의 열림으로 터보차져는 구동되기 시작하며 압축된 공기는 바이패스라인을 통해 대기로 방출된다. 터보차져가 정격 회전수의 약 30 % 정도까지 상승하게 되면 바이패스 밸브와 압축공기 탱크를 닫은 후 압축된 공기만으로 연소기에서 연소시켜 터빈으로 보내게 된다.
연소기는 Siemens-Westinghouse사의 W501D5를 개조하였다. 성능곡선 작성시 쵸킹 라인으로 운전하고자 할 경우에는 바이패스 밸브를 열고 서징 라인으로 운전할 때에는 부하밸브와 미세조정 밸브를 사용한다. 압축기 출구와 부하밸브사이에서는 ISO 규격에 맞도록 충분한 직관을 확보한 뒤 유량을 계측하게 된다.
7. 결과 및 고찰
Fig. 12, Fig. 13에서는 디퓨저를 포함하지 않고 임펠러단독 유동해석 결과를 보여주고 있다. 즉, 임펠러 날개 수와 출구직경에 따른 압력비와 동력을 나타내었다. 날개 수(8→9), 출구직경 (314 mm~324 mm)증가에 따라 압력비와 동력은 증가되고 있으며 설계점 대비 서지 마진 유량(Turn down ratio)은 약 6 %로 설계기준대비 작으며 쵸킹점과의 마진은 약 6 %로 상대적으로 크게 나타났다. 디퓨저를 제외한 설계점에서 임펠러의 요구효율은 87 %, 동력은 1,200 kW이므로 압력비는 5.26이상이어야 하며 이를 가장 가깝게 만족하는 설계형상은 날개 수 9+9, 출구직경 322 mm로 평가되었다. Fig. 14는 알루미늄 합금강의 시편에 대해 시험한 저주기 피로선도(S-N 곡선)이며 설계된 임펠러는 수명한도인 50,000 시간이상 운전가능한 것으로 나타났다.
본 논문에서 고압력비 및 고효율의 압축기를 달성하기 위한 베인 디퓨저 최적화 설계에서는 디퓨저 형상, 디퓨저 입구직경비, 출구 직경비에 대해 검토하였다.
베인 디퓨저 형상은 modified airfoil, channel diffuser, NACA65-4A10-06 airfoil 세 가지이다. 동일한 조건에서 비교해야 하므로 임펠러 형상, 베인 디퓨저 입구직경, 각도, 목 면적, 출구직경을 동일하게 설계하였다. Fig. 15~17에서는 각각 유량에 따른 압력비, 압력회복계수, 압력손실계수 변화를 보여주고 있다. 일반적으로 베인 디퓨저의 성능지수인 압력회복 계수(Cp)는 0.5~0.7을 유지해야 하며 압력손실계수(K)도 0.3이하여야 한다. 식 (4)에서 하첨자 2는 임펠러와 베인 디퓨저 중간인 인터페이스에서의 값이며 4는 베인디퓨저 출구직경 단면을 의미한다. 하첨자 0는 전(total)을 의미한다.
여기서 channel diffuser와 NACA65 airfoil은 전 범위에 걸쳐서 우수한 성능을 보이는 반면 modified airfoil은 낮은 압력회복 계수(0.33~0.52)를 보여주고 있으며 압력손실도 다른 두 모델에 비해 상대적으로 크게 나타남을 알 수 있다. 본 해석에서 channel diffuser가 넓은 운전범위 및 상대적으로 높은 성능을 가지는 것으로 나타났다. Fig. 18에서는 설계점 유량에서의 세 가지 베인 디퓨저 유동특성을 살펴보았다. 동일한 입구각과 목 면적으로 설계했지만 베인 디퓨저의 목 위치는 NACA65, Channel, modified airfoil순으로 나타났으며 스팬 값이 10%, 50%, 90%로 증가할수록 목의 영향은 작아지는 것으로 나타났다. 이는 주 유동이 허브쪽으로 치우치고 있음을 보여주는 것이며 날개전체에 걸친 압력분포측면에서는 channel diffuser가 압력이 상대적으로 높으며 베인 디퓨저 후류에서도 박리가 가장 작게 나타나므로 가장 효율적인 베인 디퓨저로 평가되었다.
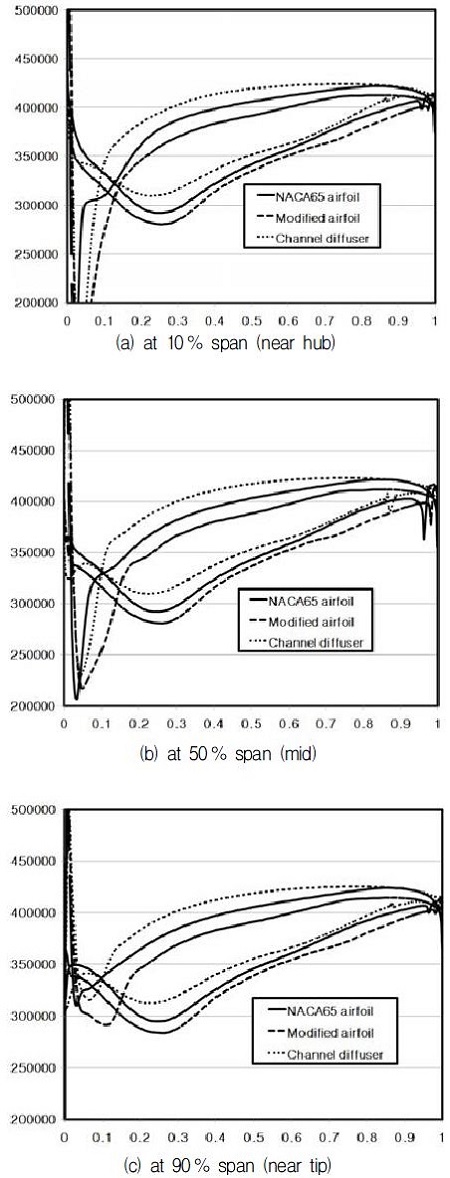
Comparison of pressure distributions for various diffuser geometries (X : streamwise direction, Y : pressure(Pa))
Fig. 19~22에서 설명하는 D2, D3, D4는 각각 임펠러 출구직경, 베인 디퓨저 입구직경 및 출구직경을 의미한다. Fig. 19, 20은 디퓨저 입구비(=베인 디퓨저 입구직경/임펠러 출구직경)변화(1.18~1.24)에 따른 압력비, 효율곡선을 나타낸다. 다른 설계변수를 동일하게 하기 위해 베인 디퓨저의 입구각도, 목면적 및 출구직경을 같도록 설계하였다. 입구비가 증가하면 압력비 및 효율이 증가하지만 입구비가 1.16을 제외하고는 전체적으로 비슷한 경향을 보인다. 입구비가 1.22와 1.24에서는 다른 경우에 비해 저 유량에서의 압력비가 높으며 서지마진이 클 것으로 예측되고 1.24인 경우에는 쵸킹 운전점이 일찍 발생할 것으로 예측된다. 따라서 해석결과로부터 베인 디퓨저 입구비가 1.22인 경우가 효율 및 운전영역 범위측면에서 가장 낫다는 것을 알 수 있다. Fig. 21, 22는 디퓨저 출구비(=베인 디퓨저 출구직경/임펠러 출구직경)변화(1.46~1.52)에 따른 압력비 및 효율곡선을 나타낸다. 베인 디퓨저 입구비와 마찬가지로 입구각도, 입구직경, 목 면적을 동일하게 설계하였다. 출구직경이 바뀌면 압축기 크기가 많이 변하지만 다른 설계변수에 비해 덜 민감함을 확인할 수 있었다. 설계점을 기준으로 출구비가 작으면 압력비가 높게 나타나고 이는 서지 마진 증가를 의미한다. 하지만 쵸킹점은 일찍 발생할 것으로 예측된다. 본 해석결과로부터 베인 디퓨저의 출구비의 최적값은 효율과 압력비를 감안하여 1.46으로 결정하였다. Fig. 23에서는 앞서 설계변수 최적화를 통해 결정된 임펠러와 베인 디퓨저의 형상을 제작하여 터보차져 전용 시험설비에서 압축기의 성능곡선을 도출하였다. 실선은 서지계측을 포함한 시험결과이며 심볼은 해석결과이다. 100 % 회전수에서 시험 결과는 유량 4.78 m3/s, 압력비 4.67, 효율 79.6 %, 동력은 1,179 kW로 설계점(유량 4.73 m3/s, 압력비 4.65, 효율 80 %)과 비교해 보면 압력비와 효율은 만족하였으나 서지마진은 부족한 것으로 나타났다.(13 % 설계기준 대비 현재 9 %) 이를 개선하기 위해 입구 재순환 케이싱의 적용시험은 진행 중이다.
8. 결 론
2011년부터 IMO(국제해사기구)의 강화된 NOx 환경규제에 따라 선박용 디젤엔진 터보차져의 압축기는 고압력비(4.65이상)를 요구하고 있다. 본 연구에서는 해당 설계점에서 80 % 효율을 목표로 최적의 임펠러, 베인 디퓨저, 케이싱설계를 수행하였으며 주요 결과는 다음과 같다.
- 1) 설계 및 해석결과로터 결정된 압축기를 제작하여 성능시험한 결과, 소요 동력 1,179 kW, 유량 4.78 m3/s, 효율 79.6 %, 압력비 4.67, 서지 9 %를 확보하여 설계점의 압력비와 효율을 만족함으로서 설계의 타당성을 검증하였다. 13 %의 목표대비 4 % 부족한 서지 마진 문제는 입구 재순환 케이싱의 설계적용을 통해 개선하고자 한다.
- 2) 베인 디퓨저의 최적형상은 modified airfoil, channel diffuser, NACA65-4A10-06 airfoil 세 가지 중에서 넓은 운전범위를 가지면서 성능도 우수한 channel diffuser로 결정하였다. 임펠러 출구직경과 베인 디퓨저 입구직경의 비는 1.16을 제외하고는 전체적으로 비슷한 경향을 보였으며 1.22인 경우가 효율 및 서지 마진 측면에서 가장 낫다는 것을 알 수 있었다.
임펠러 출구직경과 베인 디퓨저 출구 직경비는 다른 설계변수에 비해 덜 민감하였고 설계점을 기준으로 직경비가 작으면 압력비가 높게 나타나고 이는 서지마진이 증가함을 의미한다. 하지만 쵸킹점은 일찍 발생할 것으로 예측되었으며 최적값은 효율과 압력비를 감안하여 1.46으로 결정되었다. - 3) 임펠러의 출구각도, 직경, 폭은 회전수와 유량값이 반영된 slip factor를 적용하였으며 엑셀에서 3차원 형상이 도출되어 밀링 가공데이터로 자동 변환되도록 엑셀에서 설계표준화 작업을 수행하였다.
References
- J. S. Oh, (1999), A Numerical Study on Slip factor Variations in Centrifugal Compressor Impeller, KFMA, 2(3), p17-23.
- D. Japikse, (1996), Centrifugal Compressor Design and Performance, Concepts ETI, Inc.
-
H. W. Kim, J. I. Park, S. H. Ryu, S. W. Choi, and S. H. Ghal, (2009), The Performance Evaluation of Variations Diffuser Geometry of the Centrifugal Compressor in a Marine Engine(70 MW) Turbocharger, Journal of Engineering for Gas Turbine and Power, 131(1), p012201.
[https://doi.org/10.1115/1.2967733]
-
H. W. Kim, S. H. Ryu, S. H. Gahl, J. S. Ha, and Rhee
S. K. Rhee, , (2005), A Numerical Approach for the Design of the Compressor Impeller Exit Diameter in a marine Engine Turbocharger, Proceedings of the ASME Turbo Expo 2005, GT2005-68653.
[https://doi.org/10.1115/GT2005-68653]
- D. Japikse, and N. C. Baines, (1998), Diffuser Design Technology, Concepts ETI, Inc.
-
J. S. Oh, (2002), Investigation of Off-Design Performance of Vaned Diffusers in Centrifugal Compressors Part II : A Low Solidity Cascade Diffuser, ASME Turbo Expo 2002, GT2002-30388.
[https://doi.org/10.1115/GT2002-30388]