
유도가열을 이용한 히트파이프 작동유체 주입에 대한 연구
Abstract
The heat pipe is a device that effectively transfers heat through phase-change of the internal working fluid, and is a two-phase closed system. A general heat pipe is fabricated by maintaining a vacuum state on the inside and then injecting a working fluid that has undergone a degassing process. Such a degassing method has no problem in fabricating individual heat pipes but requires more time to manufacture heat pipe heat exchangers that require many heat pipes. Therefore, the present research proposed a method of manufacturing a heat pipe by using induction heating that can be heated to a degassing temperature in a short time and compared thermal performance with a heat pipe fabricated by the existing method. This study conducted numerical analysis and experiments using 5/8 in and 1 in diameter copper pipes. The error was found to be up to 7%; however, the trends between numerical analysis and experimental data were almost consistent. Based on the numerical analysis results, induction heating manufactured heat pipes under conditions of 90 V and 32 A. In addition, thermal resistance was measured, similar to the thermal resistance of heat pipe fabricated by the conventional degassing method. The manufacturing method by induction heating was validated by comparing thermal resistance with the existing method. It is expected that the manufacturing time of heat pipes can be meaningfully reduced and applied to the manufacture of heat pipes under various conditions using numerical analysis.
Keywords:
Heat pipe, Working fluid, Induction heating, Thermal resistance키워드:
히트파이프, 작동유체, 유도가열, 열저항1. 서 론
히트파이프란 내부 작동유체의 상변화를 통해 효과적으로 열을 전달하는 장치로, 금속 컨테이너 내부에 작동유체가 주입된 이상밀폐시스템(two-phase closed system)이다. 1942년 Gaugler에 의해 최초로 개발(1)되었으며, 미국 NASA(2)를 시작으로 1960년대부터 히트파이프 개발에 관한 본격적인 연구가 시작되었다.
히트파이프는 일반적으로 증발부, 단열부, 응축부로 구성되어있으며, 증발부에서는 작동유체의 증발 및 비등이 발생하고 응축부에서는 기화된 작동유체가 응축된다. 이러한 특성을 가지는 히트파이프는 구조 및 제작이 간단하여 태양에너지시스템, 공조시스템, 전자장비냉각 등(3-8) 다양한 분야에 활용되고 있다. 최근에는 히트파이프 열교환기(9-13)와 같이 폐열회수 분야에서도 활용 및 연구되고 있다.
본 연구에서 개발하는 히트파이프는 주로 폐열회수용 히트파이프 열교환기에 적용하고자 연구되었다. 히트파이프 열교환기는 기존의 핀튜브(fin-tube)형, 쉘&튜브 (shell&tube)형 폐열회수 열교환기에 비해 다양한 장점을 가지고 있다. 첫째, 히트파이프는 작동유체의 상변화를 이용하기 때문에 현열에 비해 상대적으로 더 많은 열전달이 가능하다. 둘째, 복잡한 유로 설계 없이 다중의 히트파이프의 제작으로도 효과적인 열교환이 가능하다. 셋째, 작동과정에서 히트파이프는 하나의 등온파이프가 되기 때문에 고온과 저온의 온도차이로 인한 열변형 문제에서 상대적으로 자유롭다. 이 밖에도 오염으로 인한 파울링(fouling)이나 고장에 대한 유지보수 측면에서도 기존 열교환기 대비 장점을 가지고 있다. 하지만 열교환기 제작을 위해 필요한 히트파이프의 개수가 증가함에 따라 히트파이프에 작동유체를 주입하는 기존 제작 방법으로는 생산성 한계에 이를 수 있고, 이를 극복할 수 있는 새로운 작동유체 주입 방법이 요구된다.
일반적으로 히트파이프는 진공상태의 파이프 내부에 탈기(degassing)된 작동유체를 주입(14-21)하여 제작된다. 작동유체가 주입된 히트파이프 주입부는 냉간 용접이나 아크 용접 등을 통해 밀봉될 수 있다. 내부의 진공도 확보와 작동유체의 탈기는 장치 내부에 불응축가스(non-condensable gas)를 효과적으로 제거하여 히트파이프의 열성능이 저하(18,22-23)되는 것을 방지할 목적으로 실시된다. 불응축가스가 히트파이프 열성능에 미치는 영향에 대해 연구를 진행한 Kim et al.(24)은 불응축가스에 의한 열성능 저하 문제를 극복하기 위해 10-3 Torr 수준의 히트파이프 내부 진공을 확보하고, 작동유체의 탈기를 1시간 동안 실시하였다. Chauhan et al.(20)과 Yuan et al.(21) 또한 최소 30분 이상 동안 작동유체를 가열하여, 불응축가스를 제거한 후 히트파이프 내부로 작동유체를 주입하였다. 하지만 이와 같은 탈기 과정은 단일 히트파이프의 제작에는 크게 문제가 될 수 없지만, 다량의 히트파이프가 설치되는 히트파이트 열교환기의 제작에는 많은 시간과 비용을 요구하게 된다. 이를 개선하기 위해서 기존의 작동유체를 주입하는 장치를 늘리는 것이 고려될 수 있으나, 히트파이프 생산성 측면에서는 비효율적이다. 따라서, 본 연구에서는 작동유체의 탈기와 주입을 별도로 하는 기존 히트파이프 제작 방법 대신 작동유체의 탈기와 주입이 동시에 가능하여, 제작시간 및 비용을 단축시킬 수 있는 유도가열 기법을 개발하였다.
유도가열이란 자기장과 전기장 사이의 상호 유도가 가능하다는 Faraday의 원리에 기반하여, 교류 전류가 인가되는 코일을 통해 피가열물의 표면을 가열하는 방법(25)이다. 유도가열시 피가열물을 감싸는 코일에 교류 전류를 인가하게되면, 해당 전류에 의해 발생한 자기장이 피가열물 내부에 와전류(eddy current)를 발생시킨다. 이 때 발생된 와전류는 금속 도체 내부의 전기저항에 의해 흐름을 방해받게 되고, 이로인해 발생한 줄 열(Joule heating)이 금속을 가열하게 된다. 유도가열은 일반적으로 재료의 전기저항이 커지고, 전기전도도가 낮아짐에 따라 유도가열의 속도가 증가하지만, 구리(copper)와 같이 상대적으로 전기저항이 낮고, 전기전도도가 큰 금속에서 조차도 유도가열이 가능하다. 인가되는 전류는 유도가열장치의 주파수와 동일한 속도로 교류되며, 유도가열장치의 주파수를 조절하면 피가열물에 흐르는 전류의 주파수를 조절할 수 있다. 이와 같은 원리로 작동하는 유도가열은 가열 시간이 빠르고, 높은 효율로 작동되며, 비접촉으로 가열할 수 있는 장점이 있다. 이러한 특징 때문에 유도가열은 산업뿐만 아니라 의료 및 요리 분야(25-27)까지 널리 이용되고 있다.
본 연구에서는 내부 진공 및 탈기 과정을 거쳐 히트파이프에 작동유체를 별도로 주입하는 기존의 히트파이프 작동유체 주입 방식에 대비하여 상대적으로 짧은 시간 안에 내부 작동유체를 탈기할 수 있는 유도가열을 이용하여 히트파이프 제작하고, 기존 작동유체 주입 방법으로 제작된 히트파이프와 열성능을 상호 비교하였다. 또한, 탈기 온도 및 유도가열에 필요한 작동 시간 및 조건을 효과적으로 예측하기 위해 다중물리 전열해석을 진행하였으며, 전열해석으로부터 얻은 유도가열 조건을 기반으로 작동유체 주입을 실시하여 히트파이프를 제작하였다.
2. 실험장치 및 방법
2.1 히트파이프 작동유체 주입을 위한 유도가열 장치
본 실험에 사용된 유도가열장치는 히트파이프 내부에 목표 부피만큼의 탈기 된 작동유체가 주입될 수 있도록 고안된 장치로, 20 : 1의 턴다운 비(turn-down ratio)로 출력을 제어할 수 있으며 최대 10 kW 까지의 출력을 낼 수 있다. 유도가열장치는 Fig. 1과 같이 유도가열의 조건을 설정할 수 있는 제어부와 실제 유도가열이 발생하는 코일부, 둘 사이를 연결해주는 케이블로 구성되어있다. 코일부는 8 mm의 직경을 가지는 구리를 이용하여 제작되었으며, 가로 길이는 456 mm이고, 총 11회 회전하여 히트파이프를 가열할 수 있도록 설계하였다. 제어부로부터 전달된 전류와 냉각장치로부터 공급되는 냉각수는 케이블을 통해 코일로 전달되며, 코일은 이를 통해 유도가열에 필요한 자기장을 만들어내게 된다.
실험에 사용된 유도가열장치는 제어부를 통해 온도제어와 출력제어의 두 가지 방법으로 가열을 조절할 수 있다. 온도제어 방법은 유도가열장치와 연결된 K형 열전대를 피가열체에 부착한 뒤 제어부에 목표온도를 설정하면, 부착된 열전대로부터 획득된 온도 정보가 제어부에 전달되어 PID 제어를 통해 유도가열의 세기를 조절한다. 출력제어 방법은 수동으로 원하는 출력값을 설정하고, 피가열체의 온도와 관계없이 지속적으로 일정한 출력 조건에서 유도가열하는 방법이다. 출력제어의 경우, 목표 온도가 없기 때문에 연속적으로 피가열체의 온도를 증가시키게 된다. 본 연구에서는 출력 조건을 기준으로 피가열체의 온도상승을 추적 및 예측하기 위해 주로 출력제어 방법을 통해 유도가열을 실시하였다.
히트파이프 내 작동유체 주입량은 일반적으로 증발부의 체적을 초과하지 않는다. 본 연구에서 사용된 히트파이프는 히트파이프 열교환기에 사용될 수 있도록 증발부 250 mm, 응축부 150 mm로 제작되었다. 증발부 영역에만 집중적으로 열을 인가하기 위해 Fig. 1에 도시된 바와 같이 약 300 mm이 증발부 높이 근처까지만 유도가열 코일 높이를 설계하였다. 또한, 유도가열장치 내부에 설치된 히트파이프들의 전도를 방지하기 위해 유도가열에 영향을 받지 않는 절연물질인 PEEK 재질로 제작된 받침대(holder)를 설치하여 히트파이프를 고정하였다.
2.2 유도가열을 이용한 히트파이프 내부 작동유체 가열 및 제작
히트파이프의 내부 작동유체 가열 및 제작과정은 Fig. 2에 나타나 있다. 먼저, 제작하고자 하는 구리 파이프를 유도가열 장치 사이에 설치하고, 내부 부피를 계산하여 구리 파이프 전체 부피의 약 50%가 되도록 작동유체를 먼저 주입한다. Table 1에 정리된 바와 같이 직경 5/8 in와 1 in를 갖는 구리 파이프 각각에 대해 초기 200 mm 높이로 작동유체를 주입하였으며, 각각 43 mL, 100 mL의 작동유체 주입이 요구된다.
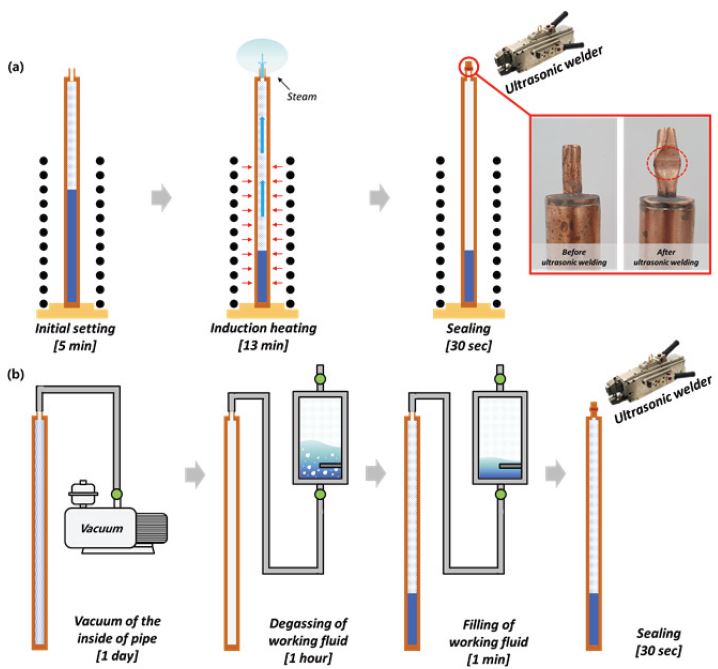
Schematic of fabrication process and time of heat pipe (a) induction heating method, (b) conventional method
본 연구에서는 증류수를 작동유체로 사용하였으며, 작동유체 주입량은 무게 측정을 통해 다시 검증하였다. 작동유체 초기 주입이 완료되면, 설치된 구리 파이프를 가열하기 위해 유도가열 장치를 작동시킨다. 이때, 유도가열 조건은 해석으로부터 획득한 조건이 사용되었으며, 출력제어 방법을 통해 유도가열을 실시하였다. 구리 파이프가 지속적으로 유도가열됨에 따라 파이프의 온도는 점차 상승하게 되며, 가열된 열은 전도열전달을 통해 구리 파이프 내부 작동유체로 전달되어 작동유체 온도를 상승시킬 수 있다. 구리 파이프 내부의 작동유체는 유도가열에 따라 증발 및 비등에 의해 기화되며, 기화된 작동유체는 파이프 상단을 통해 대기로 배출된다. 작동유체의 지속적인 기화로 인해 파이프 내부에 작동유체의 양이 감소하게 되며, 히트파이프의 작동유체 주입량이 목표한 부피에 도달하면 유도가열은 중단된다. 본 연구에서는 히트파이프 내부 작동유체의 주입량을 증발부 부피 대비 50% (높이 기준, 125 mm)로 설정하였으며, 목표 부피 획득을 위한 유도가열 시간 조건은 실험적 경험을 통해 선정하였다. 작동유체가 목표 주입량에 도달한 후에는 유도가열 장치의 가동을 중지시킨 후 짧은 시간 안에 파이프 주입부를 초음파 용접하여 파이프를 밀봉한다. 상기의 과정들을 거치면 유도가열에 의해 내부 목표 주입량을 만족하는 탈기된 작동유체가 주입된 히트파이프의 제작이 이루어지게 된다.
2.3 유도가열된 히트파이프 표면 온도 측정
일반적으로 유도가열 과정에서 발생한 기전력은 열전대를 이용한 온도측정에 대하여 오차를 유발할 수 있는 것으로 알려져 있다.(28-29) 따라서, 본 실험에서는 해석에 사용될 표면 온도 데이터의 신뢰성을 확보하기 위해 먼저 열전대 형식에 따른 측정온도들을 비교 검증하였다. Fig. 3에 도시된 바와 같이 3가지 타입의 OMEGA사의 K형 열전대를 준비하고, 유도가열시 구리 파이프의 표면 온도를 측정하였다. Bare 열전대는 보호 피복을 모두 벗겨낸 금속 도선 상태에서, 금속의 끝단을 점용접(spot welding)하여 구리 파이프에 부착하였다. Teflon 열전대는 열전대의 금속 도선이 Teflon 피복으로 보호되어 있으며, 열전대 끝단의 피복만을 제거한 뒤 점용접하여 파이프 표면에 부착하였다. Sheath 열전대는 금속 열전대 외부가 Inconel 피복으로 보호된 직경 0.5 mm인 열전대로서, 끝단을 구리 파이프 표면에 부착하였다. 3 가지 타입의 열전대 모두 파이프의 동일한 위치에 부착한 후 에폭시로 고정하였으며, 이때 Teflon 열전대의 금속 끝단은 모두 에폭시 도포 영역 안에 위치시켰다.
열전대 검증을 위해 Table 1에 나타난 5/8 in 외경을 갖는 길이 400 mm의 구리 파이프가 사용되었다. 구리 파이프의 중심 높이에서의 온도 변화를 관찰하기 위해 3개의 열전대 모두 200 mm 높이에 설치되었다. 유도가열이 작동되는 주파수는 31 kHz로 고정하였으며, 1800 W부터 3600 W까지 600 W식 인가전력을 증가시켜가며 유도가열이 열전대의 온도 측정에 미치는 영향을 평가하였다.
Fig. 3에서 인가전력이 증가함에 따라 Bare 열전대의 측정온도가 급격히 상승하고, 이후 3600 W에서는 급격한 온도 변동이 발생하는 것을 볼 수 있다. Bare 열전대와 비교하면 Sheath와 Teflon 열전대에서는 급격한 온도상승은 나타나지 않았으며, 인가전력이 증가함에 따라 일정하게 온도가 상승함을 확인하였다. 유도가열이 종료된 직후, Bare 열전대 온도가 급격히 감소하였으며, Sheath와 Teflon 열전대로부터 측정된 온도와 비슷한 값으로 수렴함을 확인할 수 있다. 이를 통해 Bare 열전대는 유도가열 과정에서 온도측정에 크게 영향을 받는 것을 확인하였다. 따라서, 내부 금속들이 피복된 Sheath와 Teflon 열전대는 유도가열이 온도측정에 미치는 영향이 거의 없음을 확인하였다. 따라서 본 연구에서는 유도가열 과정에서 구리 파이프의 표면 온도를 보다 정확하게 측정하기 위해 Sheath 열전대를 사용하였다.
3. 유도가열 전열해석 및 계산
본 연구에서는 유도가열에 의한 전열 해석을 하기 위해 다중물리(multi-physics) 유한요소해석이 가능하며, 유도가열 해석 툴을 내재하고 있는 COMSOL® Multiphysics을 사용하였다. 유도가열의 해석에는 전자기 유도 방정식과 고체 및 유체의 열전도 방정식을 이용하였으며, 두 지배방정식이 커플링되어 전자기 유도로부터 발생된 열이 전도를 통해 금속 및 유체까지 전달될 수 있도록 하였다. 주파수 도메인(frequency domain)에서는 자기장에 의한 유도가열을 계산하였고, 시간 종속 도메인(time dependent domain)에서는 그에 따른 열전달을 전열해석 하였다. 각 지배방정식은 아래와 같은 식을 가진다.
(1) |
(2) |
여기서 μ는 투자율, A는 자기포텐셜, ω는 인가각속도, σ는 전기전도도, cp는 열용량, k는 열전도도, Q는 발열량을 나타낸다.
해석에 사용된 형상은 Fig. 1에 제시된 유도가열 장치가 가지는 수치와 동일한 값을 기반으로 형상 모델링 하였으며, 해석은 아래의 가정과 함께 계산되었다. 첫째, 사용된 구리 파이프의 상대 투자율 및 상대 유전율에 대해서는 모두 1로 고정하였다. 둘째, 유도가열 코일은 11번의 턴(turn)을 가지는 원형링의 회전체로 고려하였으며, 이는 2차원 축대칭 계산을 통해 구현하였다. 셋째, 코일 조건은 single turn으로 지정하였으며, 11턴의 코일들이 모두 연결되도록 하였다. 넷째, 계산의 간편성을 위해 코일 내 흐르는 냉각수를 무시하고, 코일의 외부 온도는 15℃로 일정하게 유지한다고 가정하였다. 다섯째, 모든 전열해석은 상변화를 고려하지 않으며, 물의 비등점인 100℃ 미만까지만 진행되었다. 계산에 사용된 조건은 실험 조건과 동일하며, Table 1과 같다.
유도가열의 전열해석에 앞서 본 연구에서 수행하는 전열해석의 타당성을 평가하기 위해 표피 효과에 따른 침투 깊이(skin depth) 이용하였다. 침투 깊이는 다음과 같이 식 (3)을 이용하여 나타내었다.
(3) |
여기서 μr은 비투자율을 나타낸다.
식 (3)에 따른 이론값과 전열해석 결과는 Fig. 4에 나타내었다. 이론값과 해석값 모두 저주파에서 고주파로 갈수록 침투 깊이가 얇아짐을 보였다. 표피 효과의 이론값과 해석값의 차이는 주파수가 커짐에 따라 감소하였으며, 주파수 조건 10 Hz를 기준으로 최대 약 2.1%를 나타내었다.
COMSOL에서 제공한 매뉴얼(30)에 따르면 1에 가까운 mesh quality일수록 해석의 수렴성이 높아짐을 확인할 수 있다. 또한, Stute et al.(31)에서는 mesh quality가 0.1 이하 일 경우 수렴성의 발산이 야기될 수 있다고 보고했다. 본 해석에서는 가장 조밀한 타입의 extremely fine mesh를 생성하여 해석을 진행하였다. Extremely fine mesh의 경우, 평균 29553개의 element 및 평균 0.6532의 quality를 가지는 fine mesh와 평균 10901개의 element 및 약 0.5889의 quality를 가지는 normal mesh에 비해 약 6∼15배 많은 element를 가짐에도 불구하고, 평균 0.9060의 quality를 가졌다. 또한, 해석 소요시간이 최대 90 s 밖에 걸리지 않았다. 따라서, 해석시간 단축을 위한 mesh 수렴 테스트는 별도로 진행하지 않았다. Extremely fine mesh 조건에서 파이프 직경이 증가함에 따라 element 수가 738개 증가하고, 각각의 평균 mesh quality는 0.9074와 0.9046로 나타남을 확인하였으며, Table 2에 나타내었다. 본 해석에서의 mesh quality는 COMSOL 기반 해석을 진행한 Stute et al.(31)과 Min et al.(32)의 mesh quality가 평균 0.06∼0.64 인 것을 고려할 때 1에 비교적 근접한 값을 갖는 것으로 판단하였다.
4. 유도가열 실험 결과
4.1 유도가열에 따른 표면 온도 측정 결과 및 해석
유도가열에 따른 전열해석 결과와 비교 검증할 온도 데이터를 얻기 위해 유도가열 과정에서의 구리 파이프의 표면 온도를 측정하였다. 유도가열시 구리 파이프의 높이에 따른 온도 분포를 파악하기 위해 50, 150, 250, 350 mm 위치에 Sheath 열전대를 부착하여 실험하였다. 실험은 주입구가 개방된 구리 파이프 전체 부피의 절반만큼 증류수를 주입한 뒤 인가전압과 직경을 변화시켜가며 실시하였으며, 유도가열 조건은 Table 1에 나타나 있다.
히트파이프를 제조하기 위해 유도가열을 이용한 구리 파이프 가열 과정에서의 전열해석과 실험결과는 Fig. 5에 나타내었으며, 해석결과 앞에는 ‘S’, 실험결과 앞에는 ‘E’로 표기하였다. Fig. 5를 통해 5/8 in 구리 파이프에서는 유도가열시 인가된 전압조건과 관계없이 150 mm, 250 mm, 50 mm, 350 mm 순으로 높은 온도를 보여주고 있다. 또한, 인가된 전압이 증가함에 따라 150 mm와 350 mm 간의 온도 차이가 점차 증가함을 볼 수 있다. 이때 350 mm와 150 mm 위치에서의 최대 온도차이는 실험값을 기준으로 90 V 인가 시 15.9℃, 70 V 인가 시 10.5℃, 50 V 인가 시 5.3℃로 나타났다. 이와 같은 경향은 1 in 직경의 구리 파이프에서도 동일하게 확인할 수 있다. 1 in 직경의 구리 파이프 또한 인가전압과 관계없이 150 mm와 250 mm 에서 거의 동일한 온도를 나타내고, 50 mm 와 350 mm 에서 유사한 경향을 보여주며, 전열해석과 실험에서 모두 비교적 일치하는 표면 온도를 보여주고 있다. 1 in 직경의 경우, 실험값을 기준으로 최대 온도차는 90 V 인가 시 16.5℃, 70 V 인가 시 9.4℃, 50 V 인가 시 5.7℃로 나타났다. 구리 파이프의 직경과 인가전압에 관계없이 150 mm 과 250 mm에서 50 mm 와 350 mm에 비해 높은 온도를 갖는 이유는 다음과 같이 유도가열의 자기밀도를 이용하여 설명할 수 있다.
Fig. 6과 같이 코일 중심부에는 유도가열을 촉진시키는 자기밀도(magnetic density)가 집중되는데 비해 코일 외곽 쪽으로 갈수록 자기밀도는 감소한다. 감소된 자기밀도에 의해 유도가열 영향 또한 감소하며, 특히 유도가열 코일의 영역에서 벗어난 350 mm 지점은 하단부의 유도가열 영역으로부터 전도된 열에 의해서만 가열이 이루어지기 때문에 상대적으로 낮은 온도를 갖게 되고, 외기에 의한 열손실 또한 작용하여 실험값 및 해석값 모두에서 상대적으로 낮은 온도를 가지게 된다.
Table 3은 유도가열 시 파이프 외경에 따른 최대 및 최소 온도를 나타낸다. 파이프의 외경이 5/8 in에서 1 in로 증가함에 따라 실험과 해석결과 모두에서 동일 인가전압 대비 최대, 최소 온도가 감소하는 것을 확인할 수 있다. 이것은 구리 파이프 직경이 증가함에 따라 외부 대기에 노출된 파이프의 표면적이 증가하기 때문으로 판단된다.
Fig. 7은 인가전압에 따른 외경별 평균 오차이다. 평균 오차는 식 (4)로부터 계산되었으며, 아래와 같이 계산된다.
(4) |
여기서 N은 실험 및 해석결과에 사용된 온도 데이터 개수이며, 총 100개의 데이터를 사용하였다.
Fig. 7을 통해 전열해석과 실험 사이의 평균 오차는 파이프의 직경이 커짐에 따라 증가함을 확인하였다. 이는 외기 영향에 대한 고려가 해석에는 충분히 고려되지 못했기 때문으로 판단된다. 또한, 5/8 in와 1 in 직경의 구리 파이프 모두 최대 평균 오차는 50 mm에서 나타남을 확인할 수 있다. 이는 Fig. 1에 도시된 히트파이프 받침대가 실제 코일 하단의 유도가열을 일부 저해하였으나, 해석상에는 해당 영향이 충분히 반영되지 못했기 때문으로 판단된다. Fig. 5의 결과에서도 50 mm 에서의 실험온도가 전열해석 온도 보다 낮은 것을 확인할 수 있다.
모든 전열해석 결과는 실험결과 대비, 최대 7.2%, 최소 0.6%의 평균 오차를 가졌다. 해당 오차는 유도가열을 이용하여 노심용융물-냉각재 상호작용 설비를 모사한 Min et al.(32)의 실험값과 COMSOL 기반 해석값의 최대오차가 5.8% 수준인 것을 고려하였을 때, 타당한 수준으로 판단할 수 있다.
4.2 작동유체 주입방법에 따른 히트파이프 열성능 비교
본 연구에서는 유도가열을 이용하여 작동유체를 주입한 히트파이프를 제작하고 기존의 방법으로 제작된 히트파이프와 열성능을 비교하여, 유도가열을 이용한 히트파이프의 제조 방법의 유용성을 확인하였다.
기존의 방법으로 제작된 히트파이프는 Kim et al.에서 제시한 방법(24)과 동일한 방법으로 제작되었다. Fig. 2(b)에 나타낸 바와 같이, 히트파이프를 진공펌프와 연결한 뒤 히트파이프의 내부압력이 10-3 Torr가 될 때까지 진공을 유지한다. 이후 작동유체를 탈기 챔버에 넣어 약 1시간 정도 가열하여 탈기 시킨 후, 탈기된 작동유체를 히트파이프에 주입하고, 초음파용접을 이용하여 밀봉한다.
유도가열을 이용하여 작동유체를 주입한 히트파이프 제작은 앞서 Fig. 2(a)에 나타낸 바와 동일하게 제작되었다. 본 실험에서는 5/8 in 구리 파이프를 이용하여 히트파이프를 제작하였으며, 증발부 부피 기준 주입비는 50%를 목표로 하였다. 전열해석 결과 중 모든 위치에서 실험값 대비 상대적으로 낮은 오차 분포를 가지며, 10분에 최대 90℃까지 상승한 90 V, 32 A 인가 조건을 실제 히트파이프 작동유체 주입 조건으로 선정하였다. 해당조건에서 히트파이프를 13분 가열 시 주입비는 약 50%에 도달하였다. Kim et al.(24)에서 제시된 방법으로 제작된 히트파이프는 주입비 50.5% 가졌으며, 유도가열 조건으로 제작된 히트파이프의 주입비는 49.9%를 가졌다.
Fig. 2에 기재된 바와 같이 히트파이프에 작동유체를 주입하는 기존 방법에서 탈기에 소요되는 시간을 1시간으로 가정하였을 때, 작동유체의 주입 시간은 약 4.6 배 단축되었고, 전체 제작 시간은 약 81 배 향상되었다.
Fig. 8에 도시된 단일 히트파이프 열성능 시험 장치를 이용하여 2가지 방법으로 제작된 히트파이프에 대하여 각각 열저항을 측정하였다. 시험 장치 하단에는 구리블록과 카트리지히터를 이용하여 증발부를 제작하였으며, 상단에는 Water jacket을 이용하여 응축부를 제작하였다. 본 실험에서는 응축부의 Water jacket에 30℃ 일정한 온도로 냉각수를 공급하였고, 증발부에서는 일정량의 열유속을 증가시키며 히트파이프의 증발부 및 응축부의 표면온도를 측정하였으며, 히트파이프의 열성능은 히트파이프의 증발부와 응축부 사이의 열저항으로 평가하였다. 실험에 사용된 장치들의 정확도 및 열저항에 대한 불확도는 Table 4에 나타내었다.
Fig. 9는 유도가열을 이용하여 제작된 히트파이프와 기존의 작동유체 주입을 이용하여 제작한 히트파이프의 열저항 비교 그래프이다. 모두 열유속이 증가함에 따라 열저항이 감소하고, 두 히트파이프 간의 열저항 차이가 감소하는 것을 확인할 수 있다. 최대 열유속 80 kW/m2 기준으로 유도가열로 제작한 히트파이프가 진공 및 탈기과정을 거친 히트파이프에 비해 약 7%의 높은 열저항을 가짐을 확인하였다. Yuan et al.이 실시한 불응축 가스로 인한 히트파이프 열성능 저하 연구(22)에서 불응축가스 존재 시 약 5배 열저항이 증가한 것과 비교하였을 때, 유도가열을 이용하여 제작된 히트파이프는 기존의 작동유체 주입 방법 못지않게 우수한 열성능을 갖는 것으로 판단할 수 있다.
5. 결 론
본 연구에서는 기존의 많은 시간이 소요되는 히트파이프의 작동유체 탈기 및 주입 과정을 유도가열방법으로 대체하여 작동유체 주입 시간을 단축시키고자 하였으며, 이와 같은 방법을 구현하는데 있어 전열해석과 실험을 통해 유도가열을 이용한 작동유체 주입 방법에 대해 다음과 같이 검토하였다.
- 1) 유도가열시 표면 온도 측정의 타당성을 확보하기 위해 열전대의 조건에 따른 온도 측정 실험을 진행하였으며, Bare 열전대의 경우 노출된 열전대 금속이 유도가열의 영향을 받아 정확한 온도를 측정하지 못함을 확인할 수 있었다.
- 2) 유도가열 실험과 전열해석 결과에서 직경과 인가전압조건과 관계없이 유도가열시 350 mm와 50 mm 지점 보다는 150 mm 와 250 mm 지점에서 높은 온도를 보였으며, 이는 코일의 중심부에 자기밀도가 집중되기 때문이다.
- 3) 전열해석 결과로부터 선정된 조건(90 V, 32 A)를 이용하여 유도가열을 통해 히트파이프를 제작하였으며, 기존 작동유체 주입 방법 대비 동등한 수준의 열저항을 갖는 히트파이프를 제조할 수 있었다.
- 4) 본 연구를 통해 유도가열을 이용한 히트파이프 제작의 유용성을 확인하였으며, 히트파이프 작동유체 주입 방법 변경에 따라 히트파이프 제작 시간을 최대 81 배 단축할 수 있었다. 또한, 전열해석 결과를 통해 다양한 직경 및 길이에 관한 히트파이프에 대한 유도가열 조건을 제시할 수 있어 히트파이프 제조 생산성을 향상시킬 수 있을 것으로 기대된다.
Acknowledgments
본 연구는 산업통상자원부의 연구비 지원을 받아 한국에너지기술평가원의 에너지수요관리핵심기술 프로그램(과제번호: 20212020800270)으로 수행되었으며, 이에 감사드립니다.
References
- R. Gaugler, 1944, US Patent No. 2350348.
-
Shukla, K. N., 2015, “Heat pipe for aerospace applications—an overview,” Journal of Electronics Cooling and Thermal Control, Vol. 5, No.1, pp. 1.
[https://doi.org/10.4236/jectc.2015.51001]
-
Mathioulakis, E., and Belessiotis, V., 2002, “A new heat-pipe type solar domestic hot water system,” Solar Energy, Vol. 72, No. 1, pp. 13∼20.
[https://doi.org/10.1016/S0038-092X(01)00088-3]
-
Shafieian, A., Khiadani, M., and Nosrati, A., 2018, “A review of latest developments, progress, and applications of heat pipe solar collectors,” Renewable and Sustainable Energy Reviews, Vol. 95, pp. 273∼304.
[https://doi.org/10.1016/j.rser.2018.07.014]
-
Yau, Y. H., 2008, “The use of a double heat pipe heat exchanger system for reducing energy consumption of treating ventilation air in an operating theatre—A full year energy consumption model simulation,” Energy and Buildings, Vol. 40, No. 5, pp. 917∼925.
[https://doi.org/10.1016/j.enbuild.2007.07.006]
- Mathur, G. D., 1996, “Using heat-pipe heat exchangers for reducing high energy costs of treating ventilation air,” Proceedings of the 31st Inter-society Energy Conversion Engineering Conference, Washington, USA, Vol. 2, pp. 1447∼1452.
-
Ahamed, M. S., Saito, Y., Mashiko, K., and Mochizuki, M., 2017, “Characterization of a high performance ultra-thin heat pipe cooling module for mobile hand held electronic devices,” Heat and Mass Transfer, Vol. 53, No. 11, pp. 3241∼3247.
[https://doi.org/10.1007/s00231-017-2022-7]
-
Yang, K. S., Yang, T. Y., Tu, C. W., Yeh, C. T., and Lee, M. T., 2015, “A novel flat polymer heat pipe with thermal via for cooling electronic devices,” Energy Conversion and Management, Vol. 100, pp. 37∼44.
[https://doi.org/10.1016/j.enconman.2015.04.063]
-
Noie-Baghban, S. H., and Majideian, G. R., 2000, “Waste heat recovery using heat pipe heat exchanger (HPHE) for surgery rooms in hospitals,” Applied thermal engineering, Vol. 20, No. 14, pp. 1271∼1282.
[https://doi.org/10.1016/S1359-4311(99)00092-7]
-
Yang, F., Yuan, X., and Lin, G., 2003, “Waste heat recovery using heat pipe heat exchanger for heating automobile using exhaust gas,” Applied Thermal Engineering, Vol. 23, No. 3, pp. 367∼372.
[https://doi.org/10.1016/S1359-4311(02)00190-4]
-
Delpech, B., Axcell, B., and Jouhara, H., 2019, “Experimental investigation of a radiative heat pipe for waste heat recovery in a ceramics kiln,” Energy, Vol. 170, pp. 636∼651.
[https://doi.org/10.1016/j.energy.2018.12.133]
-
Tian, E., He, Y. L., and Tao, W. Q., 2017, “Research on a new type waste heat recovery gravity heat pipe exchanger,” Applied Energy, Vol. 188, pp. 586∼594.
[https://doi.org/10.1016/j.apenergy.2016.12.029]
-
Brough, D., Mezquita, A., Ferrer, S., Segarra, C., Chauhan, A., Almahmoud, S., and Jouhara, H, 2020, “An experimental study and computational validation of waste heat recovery from a lab scale ceramic kiln using a vertical multi-pass heat pipe heat exchanger,” Energy, Vol. 208, 118325.
[https://doi.org/10.1016/j.energy.2020.118325]
-
Huang, B. J., Chuang, Y. H., & Yang, P. E., 2017, “Low-cost manufacturing of loop heat pipe for commercial applications,” Applied Thermal Engineering, Vol. 126, pp. 1091∼1097.
[https://doi.org/10.1016/j.applthermaleng.2016.12.062]
-
Ng, V. O., Yu, H., Wu, H. A., and Hung, Y. M., 2021, “Thermal performance enhancement and optimization of two-phase closed thermosyphon with graphene-nanoplatelets coatings,” Energy Conversion and Management, Vol. 236, 114039.
[https://doi.org/10.1016/j.enconman.2021.114039]
-
Seo, D., Shim, J., Shin, D. H., Nam, Y., & Lee, J., 2021, “Dropwise condensation of acetone and ethanol for a high-performance lubricant-impregnated thermosyphon,” International Journal of Heat and Mass Transfer, Vol. 181, 121871.
[https://doi.org/10.1016/j.ijheatmasstransfer.2021.121871]
-
Seo, D., Park, J., Shim, J., Nam, J., Shin, D. H., Nam, Y., and Lee, J., 2021, “Effects and limitations of superhydrophobic surfaces on the heat transfer performance of a two-phase closed thermosyphon,” International Journal of Heat and Mass Transfer, Vol. 176, 121446.
[https://doi.org/10.1016/j.ijheatmasstransfer.2021.121446]
-
He, T., Mei, C., and Longtin, J. P., 2017, “Thermosyphon-assisted cooling system for refrigeration applications,” International Journal of Refrigeration, Vol. 74, pp. 165∼176.
[https://doi.org/10.1016/j.ijrefrig.2016.10.012]
-
Mohseni-Gharyehsafa, B., Lyulin, Y. V., Evlashin, S. A., Kabov, O. A., and Ouerdane, H., 2021, “Characterization and performance of a 3D-printed two-phase closed thermosyphon,” Thermal Science and Engineering Progress, 101001.
[https://doi.org/10.1016/j.tsep.2021.101001]
-
Chauhan, A., and Kandlikar, S. G., 2017, “Effect of Liquid Volume on Thermosiphon Loop Performance Using Open Microchannels Manifold for CPU Cooling in Data Center,” ASME 2017 15th International Conference on Nanochannels, Microchannels, and Minichannels, Massachusetts, USA, V001T05A002.
[https://doi.org/10.1115/ICNMM2017-5529]
-
Yuan, L., Joshi, Y., and Nakayama, W., 2003, “Effect of condenser location and imposed circulation on the performance of a compact two-phase thermosyphon,” Microscale Thermophysical Engineering, Vol. 7, No. 2, pp. 163∼179.
[https://doi.org/10.1080/10893950390203341]
-
Yuan, J., Wang, C., Zhang, J., Ling, J., Zhou, Z., and Gao, F, 2020, “Effect of non-condensable gas on thermal characteristics in two-phase closed thermosyphon,” Applied Thermal Engineering, Vol. 173, 115233.
[https://doi.org/10.1016/j.applthermaleng.2020.115233]
-
Kim, Y. H., Shin, D. H., Kim, J., and Lee, J., 2018, “Effect of the non-condensable gas contents on heat transfer characteristics of two-phase closed thermosyphon,” International Heat Transfer Conference Digital Library, Beijing, China, pp. 4559∼4566.
[https://doi.org/10.1615/IHTC16.her.023199]
-
Kim, J. S., Kim, Y., Shin, D. H., You, S. M., and Lee, J., 2021, “Heat transfer and flow visualization of a two-phase closed thermosiphon using water, acetone, and HFE7100,” Applied Thermal Engineering, Vol. 187, 116571.
[https://doi.org/10.1016/j.applthermaleng.2021.116571]
-
Lucía, O., Maussion, P., Dede, E. J., and Burdío, J. M., 2013, “Induction heating technology and its applications: past developments, current technology, and future challenges,” IEEE Transactions on industrial electronics, Vol. 61, No. 5, pp. 2509∼2520.
[https://doi.org/10.1109/TIE.2013.2281162]
-
Stauffer, P. R., Cetas, T. C., and Jones, R. C., 1984, “Magnetic induction heating of ferromagnetic implants for inducing localized hyperthermia in deep-seated tumors,” IEEE Transactions on Biomedical Engineering, Vol. 2, pp. 235∼251.
[https://doi.org/10.1109/TBME.1984.325334]
-
El-Mashad, H. M., and Pan, Z., 2017, “Application of induction heating in food processing and cooking,” Food Engineering Reviews, Vol. 9, No. 2, pp. 82∼90.
[https://doi.org/10.1007/s12393-016-9156-0]
- Konopka, K., 2013, “Thermocouple dynamic errors correction for instantaneous temperature measurements in induction heating,” 19th IMEKO TC 4 Symposium and 17th IWADC Workshop Advances in Instrumentation and Sensors Interoperability, Barcelona, Spain, pp. 508-514.
-
Smalcerz, A., & Przylucki, R., 2013, “Impact of electromagnetic field upon temperature measurement of induction heated charges,” International Journal of Thermophysics, Vol. 34, No. 4, pp. 667∼679.
[https://doi.org/10.1007/s10765-013-1423-1]
- Comsol, A. B., 2019, “Comsol multiphysics reference manual,” COMSOL AB
-
Stute, B., Krupp, V., & von Lieres, E., 2013, “Performance of iterative equation solvers for mass transfer problems in three-dimensional sphere packings in COMSOL,” Simulation Modelling Practice and Theory, Vol. 33, pp. 115∼131.
[https://doi.org/10.1016/j.simpat.2012.10.004]
-
Min, J., Zhu, G., Yuan, Y., & Liu, J., 2021, “COMSOL simulation for design of induction heating system in VULCAN facility,” Science and Technology of Nuclear Installations.
[https://doi.org/10.1155/2021/9922503]