
Influence of Tip Clearance Gap Thickness on the Performance and Internal Flow of Mixed Flow Pump with Semi-open Casing
Abstract
Mixed flow pumps have the characteristics of centrifugal and axial flow pumps. The meridional and blade shapes of the impeller influence the performance of the mixed flow pump. Besides that, the tip clearance gap affects the pump performance, cavitation, and pressure fluctuation. In this study, the free impeller mixed flow pump with semi-open casing was designed for a specific industrial purpose. The semi-open casing is a unique proposition, which makes the open radial outflow in a mixed flow pump by dismissing the diffuser. The pump efficiency is decreased with an increase in the tip clearance gap. At the leading edge of the shroud region, the pressure drop is significant with the clearance gap thickness. The strength of reverse flow increases with an increase in tip clearance gap thickness. Therefore, the tip clearance gap significantly influenced the performance and internal flow of a mixed flow pump with a semi-open casing.
Keywords:
Mixed Flow Pump, Semi-open Casing, Free Impeller, Tip Clearance Gap, Pump Performance, Internal Flow키워드:
사류펌프, 세미오픈 케이싱, 자유임펠러, 익단간극, 펌프 성능, 내부유동1. Introduction
The mixed flow pump is a general pumping device for water circulation at medium and high flow rates. Mixed flow pumps are widely used in agricultural irrigation, flood control, water supply systems, and cooling systems for thermal plants. Mixed flow operates between centrifugal and axial pumps, which can maintain medium head and flow rates. Hence, mixed flow pumps are used in special industrial applications. Depending on the needs of the industries, modification in the mixed flow pump is necessary. A free impeller mixed flow pump with a semi-open casing is designed for a specific industrial purpose.
The impeller and diffuser are vital components of a mixed flow pump. Many researches were conducted on the traditional mixed flow pump. The rotating stall and the energy performance of the mixed flow pump are closely related to the impeller blade thickness. The significant increase in the blade thickness hurts the stall vortex and deteriorates the flow fields(1). Wang et al. conducted the optimization in mixed flow pump impeller using the inverse design method. The effect of blade loading on the hydraulic performance of a mixed flow pump was examined by CFD analysis(2). Lu et al. proposed the modified inverse design method for the impeller meridional and blade shape optimization for mixed flow pumps(3). Besides the impeller meridional and blade shapes, the tip clearance gap influenced the performance of the mixed flow pump. The clearance between the rotating impeller and stationary casing wall is called the tip clearance gap or leakage gap(4). Generally, in a mixed flow pump, the tip clearance gap induces the tip leakage vortex, which remarkably reduces the efficiency of the mixed flow pump(5). Matsunuma investigated the effect of the tip clearance gap on the hydraulic loss and flow field of the turbine cascade(6). The tip clearance gap harms the head and efficiency of the mixed flow pump(7). Tip clearance gap induces strong reverse and secondary flows in the impeller flow passage(8). The leakage flow through the clearance gap interacts with the main flow, which causes an unstable flow pattern(9), cavitation(10), and pressure fluctuation(11) in the impeller flow passage.
Generally, many studies regarding enclosed mixed flow were conducted. The objective of this study is to design a kind of unique shape of a mixed flow pump for a specific purpose. In this study, the mixed flow pump with semi-open type casing was designed to obtain reasonable head at high flow rates. The various tip clearance gaps were prepared to encounter their effect on the hydraulic performance and internal flow characteristics.
2. Modeling and Methodology
2.1 Design and Modeling
The free impeller with semi-open casing geometry is designed according to the previous design theory(12). The mixed flow pump is designed based on a specific speed. The specific speed of the mixed flow pump is 810 [m-m³/min]. Table 1 shows the detailed specifications of the mixed flow pump.
(1) |
where Ns is the specific speed of the pump (m-m3/min), N is rotational speed (min-1), H is the effective head (m), Q is the flow rate (m3/min).
Fig. 1 shows a 3D model of a free impeller mixed flow pump with a semi-open casing. The free impeller means there is no diffuser installation in the pump passage. Fig. 2 shows the detailed view of a mixed flow pump with a semi-open casing. The flow is radially outward in a mixed flow pump with a semi-open casing. Fig. 3 indicates the tip clearance gap definition. The tip clearance gap is the difference between the casing’s inner and impeller’s outer radii. The various tip clearance gaps are designed by changing the impeller’s outer radius.
2.2 Numerical Methodology
The commercial code ANSYS 2022R2(13) is adopted to conduct the steady and unsteady state numerical analysis of the mixed flow pump with semi-open casing. The Reynolds Averaged Navier Stokes (RANS) equation solved the incompressible flow in the mixed flow pump with a semi-open casing. Fig. 4 shows the numerical grids for the mixed flow pump with semi-open casing. The hexahedral numerical grids are used to conduct the CFD analysis. ANSYS ICEM 2022R2(13) is used to prepare the numerical grids. The flow separation and reattachment occur in the boundary layers on the impeller wall, which requires a refined mesh layer. The y+ value for the mixed flow pump is less than 50 for the smooth transition in the boundary layer. The Shear Stress Transport (SST) model is widely used for hydraulic machinery analysis(14,15). The numerical analysis of mixed flow pumps with various tip clearance gaps is conducted by ANSYS CFX 2022R2(13). Fig. 5 shows boundary conditions for the mixed flow pump with semi-open casing.
Fig. 6 shows the mesh dependency test result at Q/QD=1.0. 8.6 million mesh node numbers are selected for stable CFD analysis. The inlet and outlet for the mixed flow pump are static pressure and mass flow rate, respectively. The frozen rotor and transient rotor-stator are interface models in the steady and transient state analysis, respectively. The detailed boundary conditions for the mixed flow pump are shown in Table 2. The performance curves of the mixed flow pump are prepared by changing the mass flow rate value at the pump outlet. The simulation converges after the RMS residual value of the continuity and momentum equations is less than 1× 10⁻⁶.
3. Results and Discussion
3.1 Performance curves for mixed flow pump with various tip clearance gap
The performance curves of mixed flow with various tip clearance gaps are evaluated using numerical analysis. Fig. 7 shows the performance curves of a mixed flow pump with a free impeller and semi-open casing. The best efficiency point and design point match well. It implies that the design methodology for a mixed flow pump with a free impeller and semi-open casing is acceptable. The best efficiencies for mixed flow pumps with clearance gaps of 2 mm, 3 mm, and 4 mm are 75%, 73%, and 70%, respectively. It shows that mixed flow pump efficiency is decreasing with an increase in clearance gap.
3.2 Internal flow behavior in mixed flow pump with various tip clearance gap
Fig. 8 indicates the pressure distribution in the free impeller mixed flow pump with a semi-open casing. The pressure at the impeller outlet decreases with increasing flow rate. At Q/QD=0.7 and 1.3, the impeller outlet pressures are 800 kPa and 300 kPa, respectively. The pressure drop at the impeller outlet is more significant at a high flow rate. Fig. 9 shows the pressure distribution in the mixed flow pump at Q/QD=1.0. The pressure at the impeller outlet decreases with an increase in the tip clearance gap. The low-pressure region is visible at the tip clearance gap. With an increase in tip clearance gap, the low-pressure zone increases drastically. At the impeller suction side, the low-pressure area is increased drastically with an increase in tip clearance gap thickness.
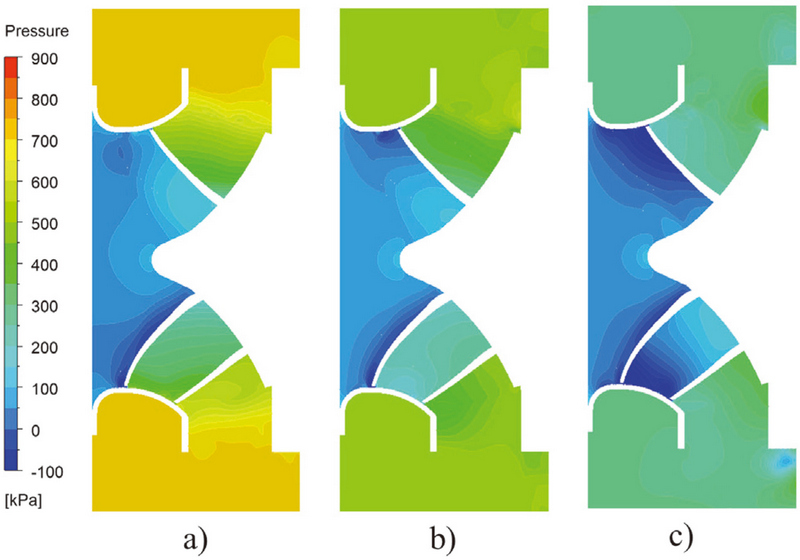
Pressure contours in impeller flow passage with tip clearance gap 3 mm at a) Q/QD=0.7 b) Q/QD=1.0 and c) Q/QD=1.3
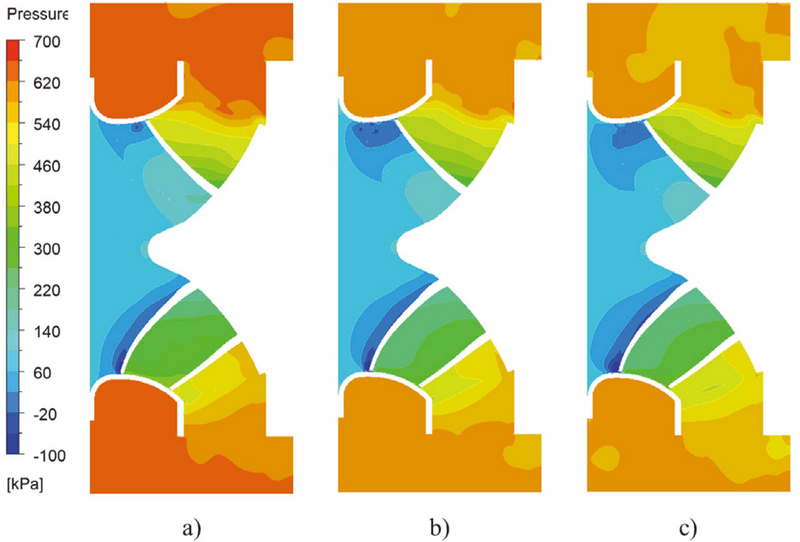
Pressure contours in impeller flow passage at Q/QD=1.0 and tip clearance gap a) 2 mm b) 3 mm and c) 4 mm
Fig. 10 shows velocity vectors in the upper half flow passage of the free impeller mixed flow pump with a semi-open casing. When the tip clearance gap is 2 mm, the velocity vectors are comparatively smoother than those of the higher tip clearance gap. However, the strength of reverse flow increased drastically with an increase in the tip clearance gap thickness.

Velocity vectors and reverse flow in impeller flow passage at Q/QD=1.0 and tip clearance gap a) 2 mm b) 3 mm and c) 4 mm
Fig. 11 shows the pressure distribution from the impeller leading edge (LE) to the trailing edge (TE). The pressure at suction and pressure sides are comparatively higher in the impeller with a 2 mm tip clearance gap. At TE of the impeller suction side, 455 kPa, 437 kPa, and 427 kPa are the pressure values with the tip clearance gaps of 2 mm, 3 mm, and 4 mm, respectively. Fig. 12 represents the pressure distribution at the mid-span of the impeller from LE to TE. The difference in the pressure value with the tip clearance gap thickness is visible in the mid-span of the impeller. Fig. 13 indicates the pressure distribution at the shroud of the impeller. The pressure value decreases with an increase in the tip clearance gap. The pressure difference is significant in the impeller shroud compared to other sections. At the middle section of the impeller blade, the pressure values are 462 kPa, 419 kPa, and 383 kPa for the tip clearance gaps 2 mm, 3 mm, and 4 mm, respectively. At the shroud region, the pressure drop of 50 kPa is possible with an increase of 1 mm of tip clearance gap thickness. At a normalized d istance of 0.8-0.9 from LE to TE, the pressure tendencies are different for 3 mm and 4 mm clearance gaps due to the inception of reverse flow.
Fig. 14 indicates pressure distribution from impeller LE to TE at Q/QD=0.3. The pressure difference between LE and TE is higher in the impeller with a 4 mm clearance gap than 2 mm and 3 mm clearance gap. Hence, the impeller with a clearance gap of 4 mm has a higher head than the clearance gap of 2 mm and 3 mm at the deep partial flow rates.
Fig. 15 shows pressure distribution from the hub to the shroud of the impeller at LE. At the hub, the pressure values are 77 kPa, 74 kPa, and 73 kPa for the tip clearance gaps of 2 mm, 3 mm, and 4 mm, respectively. The linear pressure drop is observed from the hub to the shroud in the impeller LE. At the shroud region, the sudden pressure change is due to the high intensity of reverse flow in the tip clearance gap passage.
Fig. 16 shows the pressure distribution in the mid-stream impeller. At mid-stream, the pressure increases from hub to shroud. The pressures are increased from 222 kPa to 284 kPa, 216 kPa to 256 kPa, and 210 kPa to 238 kPa for the impeller with the tip clearance gaps of 2 mm, 3 mm, and 4 mm, respectively. The pressure rises from the hub to the shroud at mid-stream are 62 kPa, 40 kPa, and 28 kPa for 2 mm, 3 mm, and 4 mm tip clearance gaps, respectively. Fig. 17 shows the pressure distribution in the trailing edge of the impeller. At the TE of the shroud region, 474 kPa, 443 kPa, and 426 kPa are pressure values for the tip clearance gaps of 2 mm, 3 mm, and 4 mm, respectively. It concludes that the tip clearance gap plays a vital role in the internal flow of a free impeller mixed flow pump with a semi-open casing. When the tip clearance gap thickness increases, the pressure value in the impeller flow passage is decreased. The tip clearance gap has a significant influence on the impeller shroud region. With the increase in tip clearance gap, the cavitation inception possibility is increased at LE of the shroud region.
3.3 Suction performance of mixed flow pump with semi-open casing
The cavitation analysis is conducted in a free impeller mixed flow pump. The cavitation number is used to evaluate the suction performance of the mixed flow pump.
(2) |
where σ is the cavitation number, pin and pvap are inlet pressure and vapor pressure, respectively.
Fig. 18 shows the suction performance of a mixed flow pump with a tip clearance gap of 2 mm. The critical cavitation number determines the cavitation inception point in the mixed flow pump. The critical cavitation point is the location where the head drop is significant. The critical cavitation numbers are 0.13, 0.37, and 1.51 for Q/QD= 0.7, 1.0 and 1.3, respectively.
The possibility of cavitation is increased with high flow rates. The critical cavitation number for Q/QD= 0.7 and 1.0 is below 0.5, which implies that the cavitation susceptibility is low in the mixed flow pump. Fig. 18 shows vapor volume fraction distribution in a mixed flow pump at Q/QD=0.7. In Fig. 19, 0 and 1 represent volume fractions of the water and the water vapor, respectively. At σ=0.43 and 0.35, the water vapor volume fraction is negligible. The water vapor volume fraction becomes visible at σ=0.15. Hence, it implies that a mixed flow pump with a semi-open casing design is acceptable for the suction performance.
3.4 Pressure fluctuation in mixed flow pump with semi-open casing
The Fast Fourier Transform (FFT) is used to monitor the pressure fluctuation in the clearance gap of the mixed flow pump. Fig. 20 shows FFT analysis results at various flow conditions with a 4 mm clearance gap. The pressure is measured at the clearance gap. The pressure amplitude is occurred periodically with blade passing frequency (BPF). The blade passing frequency represents the vibration frequency generated by the impeller due to the interaction between the blades and the clearance gap. The blade passing frequency (BPF) is calculated using Eq. (3).
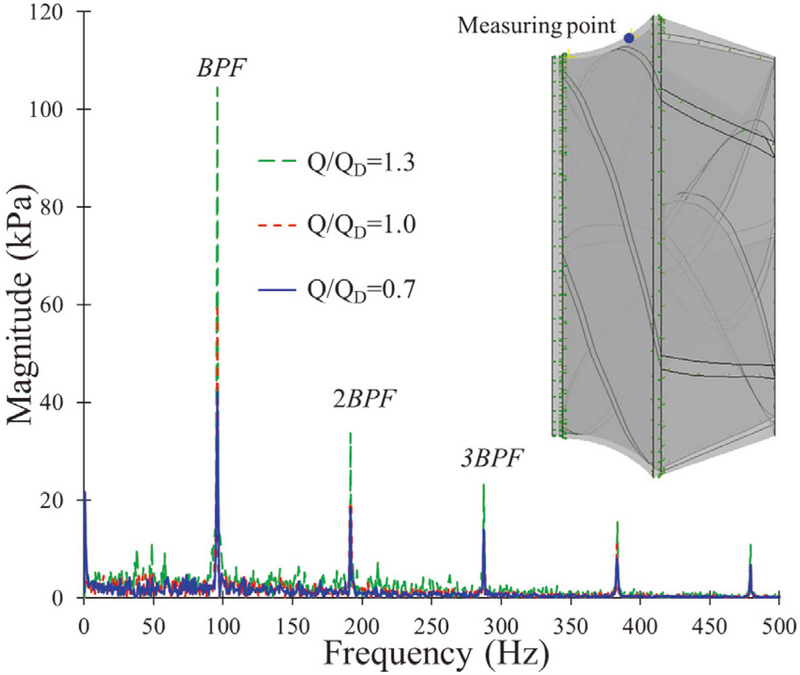
Pressure fluctuations in the impeller flow passage with tip clearance gap 4 mm at various flow rates
(3) |
where N is impeller rotational speed (min-1), and z is the number of impeller blades.
The blade passing frequency for the free impeller mixed flow pump is 95.83 Hz. The peak pressure amplitudes are 60 kPa at the BPF and 19 kPa at the 2BPF. It shows that pressure amplitude is reduced threefold when frequency increases from BPF to 2BPF. The pressure amplitude is high at Q/QD=1.3 compared to those of Q/QD=1.0 and 0.7. The maximum pressure amplitudes of 42 kPa, 60 kPa, and 105 kPa are observed in impeller flow passage at Q/QD=0.7, 1.0, and 1.3, respectively.
4. Conclusion
The free impeller mixed flow pump with semi-open casing was designed for a specific industrial purpose. The semi- open c asing design makes t he o pen radial flow in the mixed flow pump without a diffuser. The effect of the tip clearance gap on mixed flow pump performance was investigated. The increase in the tip clearance gap harms the efficiency and head of the mixed flow pump. When the tip clearance gap thickness increases from 2 mm to 4 mm, the pump efficiency is reduced by 5%, and the pump head is decreased from 47m to 40m at the design point. A slight increase in the tip clearance gap shows the damaging loss in the mixed flow pump.
The tip clearance gap contributes to the leakage flow and secondary vortex. The magnitude of the reverse flow from the tip clearance gap is directly proportional to its thickness. A significant pressure drop is observed in the impeller flow passage when the tip clearance gap thickness is increased. The tip clearance gap significantly influenced the impeller’s leading edge and shroud region.
Acknowledgments
본 논문은 2023년 국방기술진흥연구소 지원과제인 “고압 압축공기를 이용한 터보펌프 설계 기술 (과제번호 : 20-102-D00-003)”의 지원을 받아서 수행한 연구개발 결과입니다.
References
-
Ji, L., Li, W., Shi, W., Tian, F. and Agarwal, R., 2021, “Effect of blade thickness on rotating stall of mixed-flow pump using entropy generation analysis,” Energy, Vol. 236, pp. 121381.
[https://doi.org/10.1016/j.energy.2021.121381]
-
Wang, M., Li, Y., Yuan, J. and Osman, F.K., 2021, “Influence of span-wise distribution of impeller exit circulation on optimization results of mixed flow pump,” Applied Sciences, Vol. 11, No. 2, pp. 507.
[https://doi.org/10.3390/app11020507]
-
Lu, Y., Wang, X., Wang, W. and Zhou, F., 2018, “Application of the modified inverse design method in the optimization of the runner blade of a mixed-flow pump,” Chinese Journal of Mechanical Engineering, Vol. 31, No 105, pp. 1∼17.
[https://doi.org/10.1186/s10033-018-0302-x]
-
Laborde, R., Chantrel, P. and Mory, M., 1997, “Tip clearance and tip vortex cavitation in an axial flow pump,” ASME Journal of Fluids Engineering, Vol. 119, No. 3, pp. 680∼685.
[https://doi.org/10.1115/1.2819298]
-
Liu, Y., Tan, L., Hao, Y. and Xu, Y., 2017, “Energy performance and flow patterns of a mixed-flow pump with different tip clearance sizes,” Energies, Vol. 10, No. 2, pp. 191.
[https://doi.org/10.3390/en10020191]
-
Matsunuma, T., 2006, “Effects of Reynolds number and free-stream turbulence on turbine tip clearance flow,” Journal of Turbomachinery, Vol. 128, No. 1, pp. 166∼177.
[https://doi.org/10.1115/1.2103091]
-
Hao, Y. and Tan, L., 2018, “Symmetrical and unsymmetrical tip clearances on cavitation performance and radial force of a mixed flow pump as turbine at pump mode,” Renewable Energy, Vol. 127, pp. 368∼376.
[https://doi.org/10.1016/j.renene.2018.04.072]
-
Kim, S., Choi, C., Kim, J., Park, J. and Baek, J., 2013, “Effects of tip clearance on performance and characteristics of backflow in a turbopump inducer,” Proceedings of the Institution of Mechanical Engineers, Part A: Journal of Power and Energy, Vol. 227, No. 8, pp. 847∼857.
[https://doi.org/10.1177/0957650913499014]
-
Goto, A., 1992, “The effect of tip leakage flow on part-load performance of a mixed-flow pump impeller,” Journal of Turbomachinery, Vol. 114, No. 02, pp 383∼391.
[https://doi.org/10.1115/1.2929155]
-
Xu, B., Shen, X., Zhang, D. and Zhang, W., 2019, “Experimental and numerical investigation on the tip leakage vortex cavitation in an axial flow pump with different tip clearances,” Processes, Vol. 7, No. 12, pp. 935.
[https://doi.org/10.3390/pr7120935]
-
Feng, J., Luo, X., Guo, P. and Wu, G., 2016, “Influence of tip clearance on pressure fluctuations in an axial flow pump,” Journal of Mechanical Science and Technology, Vol. 30, No. 4, pp. 1603∼1610.
[https://doi.org/10.1007/s12206-016-0315-2]
- A. J. Stepanoff, 1957, Centrifugal and axial flow pumps: theory, design, and application, John Wiley & Sons, Inc., New York.
- ANSYS Inc., 2022, “ANSYS CFX documentation version 2022R2”, http://www.ansys.com, .
-
Shrestha, U. and Choi, Y-D., 2020, “A CFD-based shape design optimization process of fixed flow passages in a Francis hydro turbine,” Processes, Vol. 8, No. 11, pp. 1392.
[https://doi.org/10.3390/pr8111392]
-
Shrestha, U. and Choi, Y-D., 2022, “Estimation of Reverse Flow Rate in J-Groove Channel of AJP and SCP Models Using CFD Analysis,” Processes, Vol. 10, No. 4, pp. 785.
[https://doi.org/10.3390/pr10040785]