
경사진 원형관에서의 공냉응축에 관한 실험적 연구
Abstract
In this study, the experimental investigation of air-cooled condensation in slightly inclined circular tubes with and without fins has been conducted. In order to assess the effects of the essential parameters, variable air velocities and steam mass flow rates were given to the test section. The heat transfer performance of air-cooled condensation were dominantly affected by the air velocity, however, the increase of the steam mass flow rate gave relatively weaker effects to total heat transfer capability. And in the experimental cases with the finned tube, the total heat transfer rate of the finned tube was significantly larger than that of the flat tube. From those results, it can be confirmed that the most important parameter for air-cooled condensation heat transfer is the convective heat transfer characteristics of air. Therefore, for the well-designed long-term cooling passive safety system, the consideration of the optimal design of the fin geometry is needed, and the experimental and numerical validations of the heat transfer capability of the finned tube would be required.
Keywords:
Air-cooled Condensation, Air Velocity, Finned Tube, Steam Mass Flow Rate키워드:
공냉응축, 공기 유속, 휜튜브, 증기 유량1. 서 론
수평 및 소폭 기울어진 원형관에서의 응축열전달은 경수형 원자로(Light water nuclear reactor, LWR) 피동안전계통(Passive safety system) 및 기타 발전시스템에서의 응축수 회수에 필수적으로 활용되는 중요한 메커니즘이다. 또한, 2011년에 발생한 후쿠시마 원전사고 이후, 운전원의 개입이 배제된 상황에서의 72시간 이상 전원상실 사고에 대한 완벽한 대처가 새로운 원전 안전성의 기준으로 제시되면서 원자로 및 격납용기의 장기 피동냉각 기술의 개발 및 기존 기술의 수정이 새로운 이슈로 부각되었다.
최근 국내 표준설계인허가를 획득한 신형 가압경수로 APR+(Advanced Power REactor PLus)의 PAFS(Passive Auxiliary Feedwater System) 및 중동 수출이 가시화 되고 있는 중소형 일체형 원자로 SMART(System-integrated Modular Advanced ReacTor)의 PRHRS(Passive Residual Heat Removal System)는 사고 발생 시 증기발생기 2차측의 증기를 대형 냉각수 저장탱크 내 열교환기에서 응축시켜 노심의 잔열을 제거하기 위한 피동안전계통이다.
또한 이와 유사한 개념은 격납용기 피동냉각을 위한 기술에도 적용되고 있다. 이러한 방식의 피동안전계통에서 최종 열침원은 대형 탱크 내에 저장된 냉각수이다(Fig. 1). 결국 이러한 피동냉각기술의 장기 냉각성능은 탱크 내 열교환기에서 방출되는 열로 인한 냉각수의 체적변화(증발)와 직결된다.
최근 국내(한국원자력연구원, KAERI)를 중심으로 피동냉각계통 작동 시, 냉각수 저장탱크에서 발생하는 증기를 공냉 열교환기에서 응축시켜 탱크로 재유입 시킴으로써 냉각수 수위 변화를 최소화하여 계통 작동시간을 연장시킬 수 있는 아이디어가 제안되었다.(1-2) 본 기술 개념은 원전사고 시 현장접근이 어려운 상황에서도 최종열침원(공기)을 유지할 수 있다는 점에서 큰 장점을 지니고 있다. 하지만 이러한 기술개념에 대한 정량적인 평가 및 최적화 등의 실제 응용을 위한 연구는 아직 초기단계에 머무르고 있으며, 이에 따라 공냉 열교환기 배관크기, 공기 유동방향, 배관각도, 휜(Fin) 배열 및 형상 등 구체적인 설계변수들의 영향 평가를 위한 체계적인 연구가 반드시 필요하다. 뿐만 아니라 설계 열교환기 배관 내에서의 응축현상과 관련된 2상유동양식 및 액막거동에 대한 정확한 이해가 필요하다.(3-10)
본 연구에서는 공냉을 활용한 장기 피동냉각계통 기술에 대한 기초데이터 제공을 위해 공냉 응축열전달에 관한 실험적 연구를 수행하였다. 실험을 위해 소폭 경사진(약 3도) 단일 원형관 공냉 응축실험장치를 구축하였으며, 공기 유속, 증기 유량 및 휜의 유무에 따른 열전달 성능 실험을 수행하였다.
2. 실 험
2.1 실험장치 설계 및 구축
본 연구에서 구축된 실험장치는 크게 증기발생기, 과열히터, 시험부, 하류 열교환기 및 유량측정 전자저울로 구성된다. Fig. 2는 실험장치의 개념도이다.
시험부 응축관은 외경 3/4"의 상용 스테인레스 스틸 튜브(내경: 17.4 mm, 두께: 1.65 mm)를 사용하였으며, 응축관의 전체길이는 3 m로 설계하였다. 그리고 응축수의 원활한 배출을 위해 시험부를 약 3도 기울인 형태로 배치하였다.
시험부에 일정 유량의 증기를 공급하는 증기발생기에는 두 개의 카트리지 히터(총 4 kW)를 삽입하여 전력조절을 통해 증기유량을 제어하게 된다.
그리고 증기발생기 및 시험부 응축관 입구 사이에 과열히터를 배치하여 대기중으로의 열손실에 의한 유입증기의 응축을 최소화할 수 있도록 설계하였다. 시험부에서의 국부 열전달 데이터를 획득하기 위해서는 응축관 축방향으로의 균일한 공기 유동이 보장되어야 한다. 이를 위해 시험부 응축관 하단에 22개의 팬쿨러를 부착하고 쿨러로 인가되는 전압을 조절하여 최대한 균일한 유동을 조성하고, 정확한 공기 유속 제어가 가능하도록 설계하였다. 시험부에는 열전대 및 피토관을 삽입하여 공기온도, 벽면온도 및 공기유속 측정을 통해 국부 열전달계수 데이터를 획득하게 된다. 시험부 하류에는 유입되는 증기가 시험부 내에서 완전 응축되지 못할 경우, 이를 완전 응축시켜 유량측정부인 전자저울에 단상의 액체를 공급할 수 있도록 이중관 열교환기를 부착였다. 증기응축을 위한 유체는 대기압조건의 1차 증류수를 사용하였다.
2.2 실험계측 및 실험조건
본 연구에서는 공기 온도, 증기온도, 응축관 벽면온도, 피토튜브 차압, 입출구 증기 압력, 증기발생기 유체온도 및 시험부 배관 내 유체온도 등을 측정하게 된다. 그리고 모든 계측데이터는 Keysight 34970A 데이터 수집장치를 통해 1초 간격으로 획득하였다.
실험 제어변수는 증기유량, 공기유량 및 응축배관 표면의 휜의 유무이다. 증기유량은 증기발생기 히터 전력을 1.2, 2.4 및 3.6 kW로 조절하여 3개의 유량에서 실험을 수행하였으며, 공기유량은 팬쿨러에 인가하는 전압을 조절하여 6, 7 및 8 m/s의 조건에서 실험을 수행하였다.
또한 휜이 부착된 응축관의 열전달 특성을 평가하기 위해 Fig. 3과 같은 휜튜브를 제작하였다. Table 1은 본 연구에서 수행된 실험 매트릭스이다.
Table 1에서 Vair 및 는 각각 공기유속 및 증기 질량유량이다.
2.3 열전달 데이터 추출
본 연구에서는 시험부를 계측기의 위치에 따라 총 10개의 구간으로 나누어, 각 구간 내에서의 열전달량, 공기 열전달계수 및 증기 열전달 계수 등을 계측 및 계산하였으며 이를 통해 공냉 응축 열전달 거동을 분석하였다. Fig. 4는 시험부 구간에 위치한 계측기 위치를 나타내고, 식 (1)-(3)은 열전달변수 계산을 위한 계산식을 나타낸다.
(1) |
(2) |
(3) |
식 (1)-(3)에서 Qs, ρair, As, cp,air, Tf,o, Tf,i, hair, , Tω,o, hsteam, , Tsat, Tω,i는 각각 구간 열전달률 (W), 공기밀도 (kg/m3), 시험부 단면적 (m2), 공기비열 (kJ/kgK), 시험부 상부 공기온도 (°C or K), 시험부 하부 공기온도 (°C or K), 공기 열전달계수 (W/m2K), 시험부 외벽 열유속 (W/m2 ), 시험부 외벽온도 (°C or K), 응축열전달계수 (W/m2K), 시험부 내벽 열유속 (W/m2), 대기압에서 증류수의 포화온도 (°C or K) 및 시험부 내벽온도 (°C or K)이다. 시험부 내벽온도는 시험부 벽면 열유속 및 외벽온도 데이터로부터 1차원열전도 방정식을 통해 획득하였다.
3. 실험결과 및 토의
3.1 시험부 전체 열전달량
Fig. 5는 증기유량에 따른 공기유속별 시험부 전체 열전달량을 나타낸다. 전체 열전달량은 시험부 각 국간에서 측정된 열전달량을 합산하여 계산하였다. 그림에서 보는 바와 같이 시험부 응축관에서의 열전달량은 공기 유속에 따라 크게 변화한다. 이는 공기 유속의 증가에 따라 응축관 외부에서의 대류열전달계수가 증가하기 때문으로 판단할 수 있다. 하지만 동일한 공기 유속에서의 전체 열전달량에 대한 증기유량의 영향은 상대적으로 작은 것으로 나타났다. 이는 공냉 응축 열전달에서 전체 열저항 중 관내 증기 응축 열전달에 의한 영향이 공기 대류열전달에 비해 현저히 낮기 때문인 것으로 판단된다.
Fig. 6은 공기 유속에 따른 증기유량별 시험부 출구 유체온도를 나타낸다.
증기유량 0.0005 kg/s의 경우 공기 유속이 증가함에 따라 시험부 출구 유체온도가 감소하는 것으로 나타났다. 이는 증기유량이 낮은 경우 시험부 응축관 내에 유입되는 증기가 완전 응축된 후, 공기 대류열전달에 의해 과냉되기 때문인 것으로 판단된다. 하지만 증기유량 0.00106 및 0.0015 kg/s에서는 시험부 내에서 증기가 완전 응축되지 않아 포화상태로 시험부 출구로 배출되기 때문에 유체온도는 공기유속에 관계없이 포화온도 부근의 값을 나타냈다.
이러한 결과로부터 공냉 응축 열전달 성능을 지배하는 변수는 공기에 의한 관외부 대류열전달이라고 판단할 수 있다.
3.2 공기 대류 및 응축 열전달계수
Fig. 7a, b 및 c는 각각 동일한 증기유량 조건에서의 공기유속에 따른 시험부 위치별 공기 대류열전달 계수 측정값 및 상관식(식 (4))(11)을 통해 계산된 열전달 계수값을 나타낸다. 예상되는 바와 같이 공기유속의 증가에 따라 대류 열전달계수는 증가하는 것으로 나타났다. 그리고 비교 상관식(11)(식 (4))은 실험에서의 열전달 계수 값을 다소 높게 예측하였으며, 공기 유속에 따른 열전달 계수의 증가 추세는 실험 및 상관식에 유사하게 나타났다. Fig. 7에서 특정위치에서 공기 열전달계수 값이 현저히 크게 나타난 것은 시험부의 해당위치에 부착된 지지구조물로 인해 공기 유동이 왜곡되었기 때문인 것으로 추정된다.
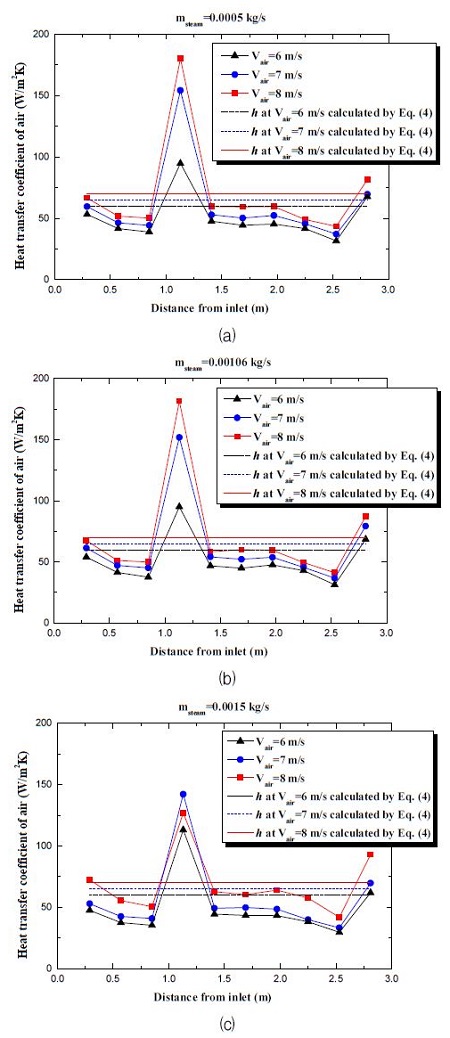
Air-side heat transfer coefficient distributions with air velocity; (a) ṁsteam = 0.0005 kg/s, (b) ṁsteam = 0.00106 kg/s, (c) ṁsteam = 0.0015 kg/s
(4)(11) |
식 (4)(11) 에서 , D, kair, , ReD 및 Pr은 각각 평균 공기 대류열전달계수 (W/m2K), 응축관 외경 (m), 공기 열전도도 (W/mK), 평균 너셀트 수, 레이놀즈 수 및 프란틀 수이다.
Fig. 8은 증기유량에 따른 시험부 위치별 응축열전달계수 분포를 나타낸다. 시험부에서의 응축 열전달계수는 전체적으로 증기유량이 증가함에 따라 증가하는 경향을 나타냈으며, 관내에서 응축이 발생함에 따른 시험부 위치별 응축 열전달 계수는 뚜렷한 경향성을 나타내지 않았다. 하지만 최소 증기유량 0.0005 kg/s의 실험조건에서 시험부 출구 부근에서 증기가 완전 응축된 후 단상 열전달 영역이 형성되어 열전달계수가 급격히 감소하였다.
그리고 Fig. 7 및 8에서 공냉 응축열전달 성능은 국부적인 위치에 따라 비교적 큰 변화를 나타낸다. 이는 응축관 국부위치에서의 공기유동특성이 상이하기 때문으로 판단된다. 그러므로 수평관 공냉 응축열전달에서 평균적인 공기유속뿐만 아니라 국부적인 공기유동특성이 중요한 변수라는 것을 알 수 있다.
3.3 휜튜브 공냉응축 열전달 성능 평가
본 연구에서는 앞서 제시된 사양의 휜튜브에 대한 공냉 응축 열전달 성능 평가실험을 수행하였다. 시험부 배관 형상 이외의 실험조건은 동일하게 유지하였다. Fig. 9는 휜튜브 배관에서의 증기유량에 따른 공기유속별 열전달량을 나타낸다. 모든 증기유량 실험조건에서 동일한 증기유량 유입 시 공기 유속이 증가함에 따라 시험부 전체 열전달량은 현저히 증가하였다. 이는 공기 유속증가에 따라 관 외부 대류열전달계수가 증가하였기 때문이다. 그리고 동일한 공기 유속에 대해 증기유량이 증가함에 따라 총 열전달량이 급격히 증가하였다. 이는 증기유량의 증가로 인한 응축열전달계수의 영향이기 보다는 증기유량이 증가함에 따라 시험부 내에서 응축 열전달이 발생하는 구간이 길어지고, 이에 따라 상대적으로 배관 외벽온도가 높은 구간이 넓게 분포함에 따른 결과인 것으로 판단된다.
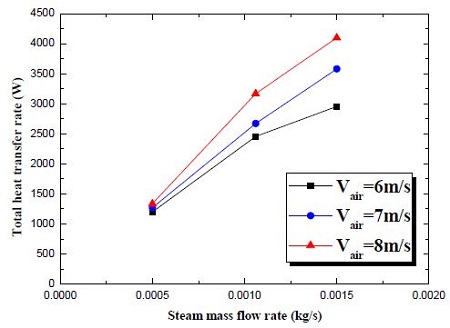
Total heat transfer rates of finned tube experiments along with steam mass flow rate and air velocity
Fig. 10은 본 연구에서 수행된 모든 휜튜브 실험케이스에서의 응축관 전단과 후단에서의 공기 온도차를 나타낸다. 배관 내 응축열전달이 발생하는 지점에서의 공기 온도차와 비교하여 단상액체로 추정되는 구간에서는 공기 온도차가 현저히 감소하는 것을 볼 수 있다.
최대 공기유속 약 8 m/s 및 최대 증기유량 0.0015 kg/s의 실험조건에서 본 연구에서 사용한 휜튜브는 약 3 m의 길이에서 최대 약 4 kW의 열을 제거할 수 있는 것으로 나타났다. Fig. 11은 휜튜브 실험에서의 공기 유속에 따른 증기유량별 시험부 출구 유체온도를 나타낸다. 이를 통해 최소 공기유속 (6 m/s) 및 최대 증기유량 (0.0015 kg/s)의 실험조건을 제외한 모든 휜튜브 실험조건에서 시험부 배관 내 증기가 완전 응축되는 것을 확인할 수 있다.
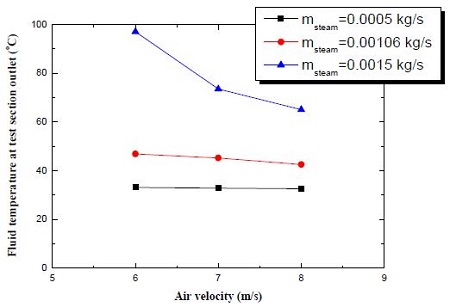
Outlet fluid temperature of finned tube experiments along with steam mass flow rate and air velocity
이러한 휜튜브 응축열전달 성능 실험결과는 앞서 언급한 바와 같이, 공냉 응축 열전달성능을 지배하는 인자가 공기측 열전달이며 적절한 휜의 설계를 통해 열전달 성능을 향상시킬 수 있다는 것을 보여준다. Fig. 12는 최대 공기유속 8 m/s에서의 증기유량에 따른 휜이 부착되지 않은 튜브 및 휜튜브 배관에서의 총 열전달량을 나타낸다. 모든 증기유량 구간에서 휜튜브의 열전달 성능이 우수하며, 이러한 효과는 증기유량이 증가할수록 더욱 현저하게 나타난다. 이 그림에서 휜이 부착되지 않은 튜브의 경우, 공기측의 지배적인 열저항으로 인해 응축관으로부터의 전체 열전달량은 증기유량의 증가와 관계없이 거의 동일하게 나타났다.
하지만 휜튜브의 경우, 휜부착으로 인한 열전달면적의 증가가 공기측 열저항을 현저히 감소시켜, 모든 증기유량에서 응축관 내 증기를 완전응축시킬 수 있었다. 이러한 결과로부터 휜부착은 본 실험에서의 최대 증기유량을 완전응축시킬 수 있도록 공기측 열전달을 감소시켰다고 해석할 수 있다.
4. 결 론
본 연구에서는 길이 약 3000 mm, 외경 3/4" 배관내부에 증기유동을 조성하고, 배관 외부를 공기로 냉각하여 공냉 응축 열전달 성능을 평가하기 위한 실험연구를 수행하였다. 핵심변수에 의한 영향을 평가하기 위해 공기유속 및 증기 유량을 변화시켜가며 실험을 수행하였고, 그 결과를 상세히 분석하였다. 공냉 응축 열전달 성능은 공기 유속에 의해 지배적인 영향을 받았으며, 증기유량 증가에 의한 관내 응축 열전달은 전체 열전달 성능에 큰 영향을 미치지 않는 것으로 나타났다. 그리고 휜 튜브에 대한 실험결과 실험조건 전구간에서 휜이 부착되지 않은 튜브에 비해 열전달 성능이 현저히 증가하는 것을 확인할 수 있었다. 이러한 결과로부터 공냉 응축 열전달 성능에 지배적인 영향을 미치는 변수는 공기측 열전달 특성이라고 판단할 수 있다. 그러므로 공기에 의한 대류 열전달을 증진시키는 것이 전체적인 열전달 성능을 증가시키는데 핵심적인 역할을 할 것이다. 공냉을 통한 장기냉각 피동계통의 설계를 위해서는 적절한 휜형상의 설계가 필수적이고, 이러한 설계는 실험 및 수치해석을 통해 정량적으로 검증되야 할 것이다. 이에 추가로, 공기측 열저항을 감소시키는 것과 동시에 관내 응축열전달을 증진시킬 수 있는 응축관 각도변화 및 관내벽 표면특성 개질 등에 대한 연구가 이루어진다면 공냉 응축열교환기의 성능 최적화를 달성할 수 있을 것으로 판단된다.
Acknowledgments
이 논문은 2016년도 산업통상자원부의 원자력 연구개발 프로그램의 재원으로 수행된 연구임(No. 2012T100100066).
References
- Kim, Y. I., Kim, K. K., Bae, Y. M., Yoon, J. H., Ha, J. J., Lee, W. J., and Kim, T. Y., (2013), “Cooling system of emergency cooling tank and nuclear power plant having the same”, Korea Patent App. No. 10-2013-0052051 & United States Patent App. No. 20140334590.
-
Kim, M. J., Moon, J. H., Bae, Y., Kim, Y. I., and Lee, H. J., (2015), “Feasibility test of the concept of long-term passive cooling system of emergency cooldown tank”, Annals of Nuclear Energy, Vol. 80, p403-408.
[https://doi.org/10.1016/j.anucene.2015.02.025]
- Baker, O., (1954), “Design of pipelines for simultaneous flow of oil and gas”, Oil Gas J, Vol. 53, p185-195.
-
Mandhane, J. M., Gregory, G. A., and Aziz, K., (1974), “A flow pattern map for gas-liquid flow in horizontal pipes”, Int. J. Multiphase Flow, Vol. 1(Iss. 4), p537-553.
[https://doi.org/10.1016/0301-9322(74)90006-8]
-
Taitel, Y., and Dukler, A. E., (1976), “A model for predicting flow regime transitions in horizontal and near horizontal gas-liquid flow”, AIChE J, Vol. 22(No. 1), p47-55.
[https://doi.org/10.1002/aic.690220105]
-
Breber, G., Palen, J. W., and Taborek, J., (1980), “Prediction of horizontal tubeside condensation of pure components using flow regime criteria”, J. Heat Transfer, Vol. 102(Iss. 3), p471-476.
[https://doi.org/10.1115/1.3244325]
-
Soliman, H. M., (1982), “On the annular-to-wavy flow pattern transition during condensation inside horizontal tubes”, Canadian J. Chem. Engr, Vol. 60(Iss. 4), p475-481.
[https://doi.org/10.1002/cjce.5450600405]
-
Dobson, M. K., and Chato, J. C., (1998), “Condensation in smooth horizontal tubes”, J. Heat Transfer, Vol. 120(Iss. 1), p193-213.
[https://doi.org/10.1115/1.2830043]
-
Hajal, J. El., Thome, J. R., and Cavallini, A., (2003), “Condensation in horizontal tubes, part 1: two-phase flow pattern map”, Int. J. Heat Mass Transfer, Vol. 46(Iss. 18), p3349-3363.
[https://doi.org/10.1016/S0017-9310(03)00139-X]
-
Thome, J. R., Hajal, J. El., and Cavallini, A., (2003), “Condensation in horizontal tubes, part 2: new heat transfer model based on flow regimes”, Int. J. Heat Mass Transfer, Vol. 46(Iss. 18), p3365-3387.
[https://doi.org/10.1016/S0017-9310(03)00140-6]
-
Churchill, S. W., and Bernstein, M., (1977), “A correlating equation for forced convectionm from gases and liquids to a circular cylinder in crossflow”, J. Heat Transfer, Vol. 99(No. 2), p300-306.
[https://doi.org/10.1115/1.3450685]