
스프레이 열전달을 이용한 저온도차 스털링 엔진의 고온수 공급유량 및 온도에 따른 기계 부하성능 실험
Abstract
Recently, Stirling engines are emerging as a key device for power conversion of renewable energy or waste energy. This study develops a LTDSE(Low Temperature Differential Stirling Engine) using a water spray for higher heat transfer and performs load performance tests for various flow rates and temperatures of hot water spray for variable engine loads emulated by a mechanical friction device. Internal temperature and pressure, working frequency and inlet and outlet temperature of the supply water are measured. As a result, the increases in flow rate and temperature of hot water respectively enhance the power output, efficiency and the working frequency, while the increasing engine load leads to decreases in working frequency but increases in the pressure amplitude. Eventually, it is revealed there exists a maximum shaft power of the test engine.
Keywords:
Stirling engine, Low temperature heat source, Spray, Heat transfer enhancement, Mechanical friction load키워드:
스털링 엔진, 저온 열원, 분무, 열전달 향상, 기계 마찰 부하1. 서 론
최근 화석연료 고갈로 인한 고유가 및 환경오염 문제 해결을 위해 신재생에너지 및 폐에너지와 같이 활용되지 않는 에너지를 전력으로 변환하기 위한 핵심장치로서 스털링 엔진(Stirling engine)이 각광받고 있다. 스털링 엔진은 1816년 영국에서 로버트 스털링(Robert Stirling)에 의해 처음으로 고안되었으며 닫힌 공간 내에서 작동 유체가 온도 차이에 의하여 압축 및 팽창을 일으켜 열에너지를 기계적 운동에너지로 변환하는 스털링 사이클을 이용한 열기관이다. 일반적으로 스털링 엔진은 가열부(Heater), 냉각부(Cooler), 디스플레이서 피스톤(Displacer piston), 파워 피스톤(Power piston)과 재생기(Regenerator) 및 연결링크로 구성되며 디스플레이서 피스톤은 실린더 내부의 팽창공간(Expansion space)과 압축공간(Compression space)의 부피비를 조절하여 엔진내부의 압력을 변화시키는 역할을 하며 파워피스톤은 내부 압력변화로부터 기계적 동력을 발생시키고 재생기는 열효율 향상을 위한 열교환기이다. 스털링 엔진은 이상적인 카르노 사이클에 필적하는 높은 효율, 운전 정숙성, 구조적 단순성, 다양한 열원에 대한 응용성 등 많은 장점으로 인하여, 현재 가정용 소형 열병합 발전, 태양열 발전, 폐열 회수 등에 대한 적용 연구가 활발하게 진행되고 있다.(1-2)
자연에 존재하는 태양열, 지열 및 내연기관 배기가스와 같이 활용되지 않고 버려지는 에너지는 상대적으로 열원의 온도가 크지 않다. 저온도차(Low temperature difference) 스털링 엔진은 이러한 저온 열원을 이용하기 위하여 작은 온도차에서 작동할 수 있도록 구성된 스털링 엔진이다. 저온도차 스털링 엔진은 Kolin(3)에 의해 상대적으로 적은 온도차인 50 ℃에서 50 RPM으로 작동하는 스털링 엔진이 처음으로 디자인 되면서 많은 연구자들에 의해서 다양한 연구가 진행되었다. 연구자들 중에서 Rizzo 등(4)은 저온도차 스털링 엔진의 설계가이드에서 디스플레이서 피스톤과 파워 피스톤의 행정체적비(Sweep volume ratio)가 크고, 디스플레이서 실린더의 열교환을 위한 면적이 넓으며, 디스플레이서 피스톤의 행정거리(Stroke)가 짧고, 작동주파수(Working frequency)가 느린 특징들을 가져야 한다고 제안하였다. Senft(5)는 0.5 ℃의 매우 작은 온도차에도 작동하는 감마(γ)형 스털링 엔진을 개발한 바 있다. 특히 Kongtragool 등(6)은 저온도차 스털링 엔진이 출력이 낮다는 점을 보완하기 위하여 단일 디스플레이서에 두 개의 파워피스톤을 적용한 새로운 메커니즘을 제안하였고 또 엔진의 부하성능을 측정하기 위해 마찰 부하를 통한 기계적 가변 부하 장치를 도입하여 저온도차 스털링 엔진의 부하성능을 측정한 결과 129 ℃의 온도차에서 최대 축 출력 1.63 W라는 결과를 얻었다.
하지만 저온도차 스털링 엔진의 경우 저온의 열원을 사용하고 자연대류를 이용하기에 엔진에 유입되는 열전달량이 매우 작으며 이로 인해 출력을 향상시키는데 한계가 있다. 이를 극복하기 위해서는 열교환기의 부피를 증가시켜 열전달량을 증가시켜야 하지만 이는 동시에 불용체적(Dead volume)의 증가로 이어지고 이로 인해 압축비가 감소하여 엔진의 출력이 저하되는 문제를 가지고 있다.(7)
이러한 문제를 해결하기 위하여 Siegel(8) 및 장선준 등(9)은 고온 및 저온의 액체를 노즐을 통해 엔진 내부에 분사함으로써 엔진의 작동 공간 내부에서 직접 열교환을 수행하여 열교환기의 부피 증가 즉, 불용체적 증가 없이 열전달량을 증가시킬 수 있는 스털링 엔진을 위한 스프레이 열교환기의 개념을 제시하였다. 장선준 등(10)은 실제 스프레이 열전달을 이용하는 스털링 엔진 모델을 제작하여 작동성을 검증하였으나 실질적인 적용연구을 위해서 필수적인 부하성능인 축 출력에 대한 연구는 진행되지 않았다.
본 연구에서는 장선준 등(10)이 개발한 스프레이 열전달을 이용한 저온도차 스털링 엔진을 이용하여 고온수의 공급 유량 및 온도를 변화시키면서 스털링 엔진의 부하성능을 내부 압력, 회전속도 및 부하 마찰 토크의 측정을 통해 부하성능을 관찰하고 기존의 저온도차 스털링 엔진과 비교분석을 진행하였다.
2. 실험 장치
2.1. 스털링 엔진
Fig. 1은 본 연구에서 사용된 스프레이 열전달을 이용한 저온도차 스털링 엔진의 개념도와 사진이다. 본 스털링 엔진은 감마(γ)형으로 파워피스톤과 디스플레이서가 동일 축 선상에 위치하지 않는 특징을 가지고 있다. 이로 인해 가열 면적을 증가시키기에 용이하기 때문에 일반적으로 저온도차 스털링 엔진에 주로 사용되고 있는 형태이다. 열에너지 전달에 이용되는 스프레이 열전달 유체는 액체 상태의 물이 사용되었고 전기히터(Electric heater)와 수냉장치(Water cooler)에서 각각 가열 및 냉각된 후 스털링 엔진의 디스플레이서 실린더 양면에 설치된 총 8개(가열부 4개, 냉각부 4개)의 마이크로 노즐(IKEUCHI KB Series)을 통해 엔진 내부에 액적(Spray particle)의 형태로 분무된다. 분무된 액적들로부터 엔진 내부 작동 기체로 열에너지가 공급되어 엔진이 작동하게 된다. 이때 열전달량은 액적의 수가 많을수록, 액적의 크기가 작을수록, 온도차가 클수록 증가한다. 이러한 고온수 및 저온수를 직접 분무하는 열전달 방식은 일반적인 열전달 방식인 금속판과 기체 사이의 자연대류를 이용하는 방식보다 효과적이다.(10)
2.2. 실험장치
Fig. 2(a)는 스프레이 열전달을 이용한 저온도차 스털링 엔진의 실험장치이다. 실험장치는 전체적으로 스털링 엔진, 고온수 및 저온수 공급을 위한 순환시스템, 기계적 가변 부하장치 및 필요한 정보 획득을 위한 센서들로 구성된다. 순환 시스템은 고온수 및 저온수가 각각의 저장탱크로부터 독립된 플라스틱 관을 따라서 마이크로 펌프(Orient MG204DC24)에 의해 이송되며 전기히터와 수냉장치를 통과하면서 필요한 열에너지를 공급 받고 엔진 내부로 분무되어 열에너지를 스털링 엔진에 공급한 후 출구를 통해 다시 저장탱크로 이동하면서 순환된다. 이때 고온수 및 저온수의 유량은 유량계(AMF- 1-10, Auto Flow co. Ltd)와 마이크로 펌프의 출력 조절을 통하여 직접 제어된다.

(a) Experimental test rig of the water-sprayed Stirling engine for proof-of-concept (b) detailed pictures of the test Stirling engine with sensors for temperature, pressure, displacement and load
Fig. 2(b)은 실험으로부터 필요한 값을 얻기 위해 설치된 각종 센서들이다. 압력센서(PSHH0002BCIG, Sensys)는 엔진내부의 압력 변화를 측정하였고 레이저 변위센서(DT20HI- N254B, SICK)을 사용하여 크랭크 홀(Crank hole)에서의 변위 피크를 생성하여 시간에 따른 크랭크 홀의 위치를 측정하였다. 측온저항체(RTD) 온도센서(TSRT, Sensys)를 이용하여 팽창공간과 압축공간의 공간 온도를 측정하였고 다른 형태의 온도센서(K-type thermocouple)을 이용하여 엔진 내부로 분무되는 스프레이 열전달 유체의 입·출구 온도를 측정하였다. Fig. 3은 실험 장치 계략도로 앞서 설명한 센서류 및 주변기기들이 표시되어 있다.
Fig. 4은 실험 스털링 엔진의 부하 성능을 측정하기 위한 기계적 가변 부하 장치의 개념도와 사진이다. 로드셀(CBCL600gf, 큐리오텍)과 크랭크휠, 추를 와이어를 이용해서 연결하여 추의 무게로 인해 발생하는 장력을 이용하여 기계적 마찰 부하를 크랭크휠에 가하였으며 스털링 엔진을 작동시켰을 경우 발생하는 와이어 장력의 변화를 로드셀을 이용하여 측정하였다. 크랭크휠이 지면에 수평하게 설치되어 있으므로 도르레를 이용하여 와이어의 방향을 전환하였고 추의 무게를 조절함으로 스털링 엔진에 작용하는 기계적 마찰 부하를 조절하였다. 본 구성에서 축 출력은 다음과 같은 (1)과 (2)식을 이용해서 구할 수 있다.
(1) |
(2) |
여기서 r는 크랭크휠의 반지름, S는 로드셀의 측정 값, W는 추의 무게, T는 부하 토크, f는 스털링 엔진의 작동주파수이다. 여기서 축 출력은 크랭크 축 끝에서 동력으로서 실제로 이용할 수 있는 출력을 말한다.
3. 실험 결과 및 고찰
스프레이 열전달을 이용한 저온도차 스털링 엔진의 부하성능 실험은 공급 유량 및 고온수의 온도 조건에 따라 진행되었다. 부하실험을 위해 추의 무게를 10 gf 간격으로 엔진이 정지할 때까지 증가시켰다. 공급유량 변화실험은 유량을 60, 75, 90 ml/min의 3단계로 변화시키면서 진행하였고 고온수 온도 변화실험은 공급유량 75 ml/min 조건에서 온도를 70 ℃에서 82 ℃까지 4 ℃ 간격으로 증가시켰다. 모든 실험에서 고온수와 저온수는 동일한 유량으로 공급하였으며 저온수의 온도는 상수도을 이용한 수냉장치에 의해 ~ 17 °C에서 일정하게 유지하였다.
3.1. 부하에 따른 엔진 작동 특성 및 출력 특성
스프레이 열전달을 이용한 저온도차 스털링 엔진의 부하 성능 실험은 고온수 및 저온수 유량을 일정하게 유지한 상태에서 고온수 온도를 서서히 증가시켜 팽창공간, 압축공간, 스프레이 열전달 유체의 입·출구 온도가 정상상태에 도달한 상태에서 진행되었다. 스프레이 열전달 유체의 입·출구 온도 및 유량을 이용해 엔진으로 입력되는 열량을 계산하였다.
Fig. 5은 실험 스털링 엔진의 기동 이후 크랭크 홀의 위치와 엔진 내부 압력의 변화를 보여준다. 엔진 내부 압력 진폭은 기동 초기 큰 변화를 보이나 시간이 지남에 따라 일정 범위로 수렴하였다. 크랭크 홀의 위치로부터 엔진의 작동주파수 및 엔진 내부 부피와 압력 간의 위상 차이를 산출하였다. 여기서 엔진 내부 부피 변화는 엔진 구조에 의해서 결정된 부피의 최대 값 및 최소 값과 엔진의 작동주파수에 의해서 나타내어진다. 이를 이용하여 실험 스털링 엔진의 압력 체적 선도를 작성하였다.

Crank position and engine pressure at the moment of engine start-up (Condition: 75 ml/min, 82 ℃, no load)
Fig. 6는 실험 스털링 엔진의 압력 체적 선도이다. 엔진 내부 압력의 측정 값들을 상용프로그램(MatlabⓇ)의 Curve fitting tool 함수를 이용해 하나의 폐곡선으로 근사화 시켰으며 그림에서 검은 선으로 표시하였다. 여기서 압력 체적 선도상의 폐곡선의 면적은 단일 사이클당 엔진이 한 일의 양을 가리킨다. 여기에 작동주파수를 곱하여 스털링 엔진의 열역학적 출력(Thermodynamic engine power)으로 정의되는 엔진출력(Engine power)을 산출하였다. Fig. 7(a)는 부하 따른 작동(Operation) 특성인 작동주파수 및 압력진폭을 나타난다. 그림에서 보듯이 부하의 증가는 작동주파수를 감소시키고 압력 진폭은 증가시킴을 알 수 있는데 여기서 작동주파수의 감소는 마찰 부하 증가로 인해 기계적 에너지의 손실이 증가되는 것으로 설명할 수 있으며 압력 진폭의 증가는 마찰 부하를 극복하고 파워 피스톤을 왕복운동 시키기에 필요한 압력증가로 설명된다.
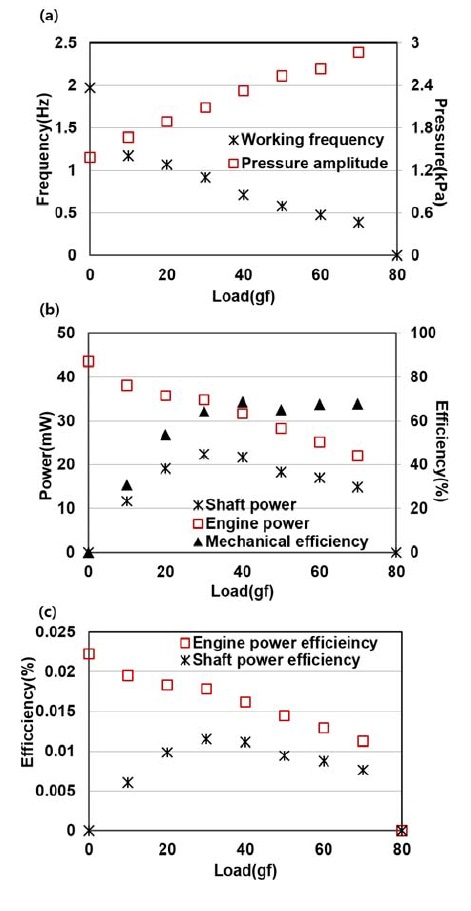
(a) Working speed, pressure amplitude and (b) power, mechanical efficiency and (c) efficiency with increasing loads (Condition: 75ml/min, 82 ℃)
Fig. 7(b)는 부하에 따른 출력(Power) 특성인 엔진출력, 축 출력 및 기계적 효율을 나타내었다. 엔진출력은 열역학적 출력을 의미하며 축 출력(Shaft power)은 부하를 가하였을 때 마찰력에 대하여 엔진이 실제 한 일을 가리킨다. 기계적 효율(Mechanical efficiency)은 엔진의 열역학적 출력으로부터 실질적으로 적용할 수 있는 축 출력으로의 변환되는 비율이며 ηmechanical = (Wshaft / Wengine) × 100로 정의된다. 여기서 엔진출력은 부하 증가와 함께 다소 감소함을 볼 수 있는데 이는 압력 진폭의 증가로 인해 파워피스톤과 실린더 사이 간 간격(Clearance)에서 발생하는 압력손실이 증가하기 때문이라고 설명할 수 있다. 축 출력은 부하 증가에 따라 증가 후 감소함을 볼 수 있는데 여기에 최적 작동 점이 존재하고 이때 축 출력이 최대가 된다. 기계적 효율은 최적 작동점 이후부터 거의 일정해짐을 볼 수 있다.
Fig. 7(c)는 부하에 따른 엔진 출력 효율(Engine power efficiency)과 축 출력 효율(Shaft power efficiency)이 나타나있다. 엔진 출력 효율은 엔진출력을 입력 열량으로 나눈 값이며 ηE.P.E (Wengine / Q∈) × 100로 정의된다. 엔진 출력 효율은 부하 증가와 함께 다소 감소하고 있음을 볼 수 있는데 이는 부하 증가에도 입력 열량은 일정하지만 엔진출력은 감소하기 때문에 엔진출력과 같은 경향이 나타났다. 축 출력 효율은 축 출력을 입력 열량으로 나눈 값이며 ηS.P.E (Wshaft / Q∈) × 100로 정의된다. 축 출력 효율도 마찬가지로 축 출력과 같은 경향이 나타났다.
3.2. 고온수 유량 및 온도에 따른 부하성능
Fig. 8은 실험 스털링 엔진의 고온수 공급 유량에 따른 부하성능을 측정하기 위하여 다양한 고온수 유량 조건(60, 75, 90 ml/min)에서 엔진의 부하 실험을 진행하여 축 출력을 측정하였다. Fig. 8(a)에는 고온수 공급 유량에 따른 축 출력의 변화가 나타나있고 Fig. 8(b)에는 각각의 고온수 공급 유량 조건에서 최적 출력이 나타나있다. 공급 유량이 증가함에 따라 축 출력 및 엔진출력이 전체적으로 상승함을 볼 수 있다. 여기에서 공급유량의 증가가 스털링 엔진의 출력을 향상시킨다는 것을 알 수 있다. 이는 공급유량이 늘어날 때 입력 열량이 증가될 뿐 아니라 노즐의 작동성(분무각도 및 면적)이 향상되는데서 그 이유를 찾을 수 있다.

(a) Shaft power with increasing load and (b) shaft power and engine power with increasing flow rates at optimum operation point
Fig. 9는 실험 스털링 엔진의 부하성능을 고온수 온도에 따라서 측정한 결과이다. 실험 조건은 공급유량을 75 ml/min으로 유지하고 고온수 온도를 70 ℃에서 82 ℃까지 4 ℃간격으로 증가시키며 진행하였다. 실험 결과 고온수 온도의 증가는 엔진출력 및 축 출력 상승으로 이어졌다. 이러한 출력 향상의 원인은 고온수 온도 상승으로 인해 입력 열량이 166 W에서 195 W로 증가하였기 때문이다.

(a) Shaft power with increasing load and (b) shaft power and engine power with increasing hot water temperatures at optimum operation pointoperation point
Table 1은 각각의 고온수 공급유량 및 온도 조건에서 얻은 최대 출력 및 효율 값을 보여주고 있다. 특히 엔진 출력 효율과 축 출력 효율이 고온수 온도 증가 및 고온수 공급유량 증가와 함께 미세하게 증가하고 있음을 볼 수 있다. 이는 입력 열량의 증가가 엔진의 부하 성능을 향상시킨다고 설명할 수 있다.
3.3. 기존 스털링 엔진과의 비교분석
Table 2는 비교 대상인 Kongtragool(6)의 엔진과 본 실험에 사용된 엔진의 설계인자이다. 설계인자들을 식 (4)에 기술한 Schmidt(9)의 공식에 대입하면 각 스털링 엔진의 이론적인 사이클당 출력을 산출할 수 있다.
(4) |
여기서 X와 Y는 각각
4. 결 론
최근 스털링 엔진은 활용되지 않는 에너지와 발전소 및 내열기관 폐열 등 한번 사용되고 버려지는 에너지를 전력으로 전환시키는 장치로서 각광을 받고 있다. 특히 저온도차 스털링 엔진은 작은 온도차에서도 작동할 수 있다는 장점을 가지고 있으므로 저밀도 에너지 즉, 저온으로 존재하는 대다수의 열원에 대하여 적용하기에 적합하다. 하지만 열전달량이 적다는 한계를 보완하기 위해서 열교환기의 부피를 늘릴 경우 불용체적이 증가하여 출력이 감소하는 단점을 가지고 있다. 본 연구에서는 이러한 문제를 해결하기 위한 대안으로 스털링 엔진 내부에 고온수 및 저온수를 직접 분무하여 열에너지를 전달하는 방식인 스프레이 열전달을 이용하는 스털링 엔진의 출력 측정실험을 진행하였다.
스프레이 열전달을 이용한 저온도차 스털링 엔진의 부하성능 시험은 기준 조건(75 ml/min, 82 ℃)에서의 작동 특성 및 출력 특성을 부하에 따라서 관찰하였고 고온수 공급유량 변화 및 고온수 온도 변화에 따른 스털링 엔진의 출력 특성에 대해 측정 하였다. 실험조건은 고온수 공급유량은 60 ml/min - 90 ml/min 이고, 고온수 온도는 70 ℃ - 90 ℃ 이다. 저온수 온도는 각각의 실험 조건에서 일정하게 유지된다.
실험 결과, 스털링 엔진의 부하가 증가할 경우 작동주파수 감소, 압력진폭 증가, 엔진출력 감소가 관측되었고 축 출력은 부하에 따른 최적 작동 점이 존재함을 확인하였다. 또 고온수 공급유량 및 온도가 증가할 경우 입력 열량의 증가로 인하여 엔진출력 및 축 출력이 증가하는 것을 확인하였다. 고온수 온도 및 유량이 각각 82 ℃, 75 ml/min인 조건에서 최대 축 출력 22.4 mW으로 측정되었다.
실험에 사용된 스털링 엔진의 경우 플라이휠의 무게에 의해서 크랭크 정렬이 제대로 이뤄지지 않았고 엔진의 실린더가 납작한 모양이기에 스프레이 열전달이 원활하게 이뤄지지 않았다. 이와 같은 이유로 인해서 엔진의 성능이 떨어졌음에도 불구하고 기존 스털링 엔진과 비교분석을 진행한 결과 이론적 출력 대비 측정된 축 출력의 비율이 비교 엔진보다 본 연구의 엔진이 약 4배 이상 높다는 결과를 얻었다. 결과적으로 스프레이 열전달을 이용하는 것이 일반적인 방식인 자연대류 보다 효과적이라는 것을 확인하였다.
본 연구에서는 스프레이 열전달을 이용한 저온도차 스털링 엔진의 부하성능을 실험을 진행하였고 측정된 값들을 분석하였다. 향후 스털링 엔진의 출력 향상을 위한 연구와 활용되지 않고 버려지는 에너지를 이용하기 위한 연구 등을 수행하고자 한다.
Acknowledgments
이 연구는 서울과학기술대학교 교내 학술연구비(일부)지원으로 수행되었습니다. 이에 관계자 여러분께 감사드립니다.
References
-
Kongtragool, B., and Wongwises, S., (2003), "A Review of Solar Powered Stirling Engines and Low Temperature Differential Stirling Engines", Renewable and Sustainable Energy Reviews, 7, p131-145.
[https://doi.org/10.1016/S1364-0321(02)00053-9]
-
Paepe, M. D., D'Herdt, P., and Mertens, D., (2006), "Micro-CHP Systems for Residential Applications", Energy Conversion and Management, 47, p3435-3446.
[https://doi.org/10.1016/j.enconman.2005.12.024]
- Kolin, I., (1983), “Isothermal stirling-cycle engine", Inter university centre pub, Dubrovnik, Croatia.
- Rizzo, J. G., (1997), “The Stirling Engine Manual, Camden Miniature Steam Services", Somerset, p1, 153, 155, 1997.
- Senft, J. R., (1991), “An Ultra-Low Temperature Differential Stirling Engine”, Proceedings of the 5th International Stirling Engine Conference, Paper ISEC 91032, Dubrovnik.
-
Kongtragool, B., and Wongwises, S., (2007), “Performance of A Twin Power Piston Low Temperature Differential Stirling Engine Powered by A Solar Simulator”, Solar Energy, 81, p884-895.
[https://doi.org/10.1016/j.solener.2006.11.004]
-
Kongtragool, B., and Wongwises, S., (2006), “Thermodynamic Analysis of A Stirling Engine Including Dead Volumes of Hot Space, Cold Space and Regenerator”, Renewable Energy, 31(3), p345-359.
[https://doi.org/10.1016/j.renene.2005.03.012]
- Siegel, A., and Schiefelbein, D., (1997), "Stirling Engine with Injection of Heat Transfer Medium", United States Patents, 5638684.
- Jang, S.-J., Lee, Y. P., and Cho, B. H., (2013), “Stirling Engine of Which the Heat-Exchanger Parts are Improved", Korean Patent 10-1239846.
-
Jang, S.-J., Lee, Y. P., and Sim, K. H., (2014), “Experimental Feasibility study on Low-Tempreature Differential Stirling Engines with Water Spray Heat Transfer", The Korean Society of Mechanical Engineers, 38, p475-482.
[https://doi.org/10.3795/KSME-B.2014.38.6.475]
- Remsburg, R., (2000), "Thermal Design of Electronic Equipment", CRC press, p62, http://dx.doi.org/10.1201/9781420042368.
- Holman, J., "Heat Transfer 4th edition", McGraw, p219, 1976.
- Totalnozzle, http://www.totalnozzle.com.