
공기호흡기용 Type3 용기의 자긴압력과 수명에 관한 연구
*한국가스안전공사 가스안전연구원**롯데케미칼연구소
**LOTTE Chemical Research Institute, 24-1 Jangdong, Yuseong-gu, Daejeon Metropolitan City
Abstract
In this study, experiments and finite element method analysis were used to determine the autofrettage pressure that is optimal and then maximizes the cycling life of Type3 composite cylinders used in self-contained breathing apparatus. For both approaches, the cylinders were pressurized at 100, 110, ..., 290 % of the test pressure, respectively. The stresses were computed by the FEM analysis; while the strains of cylinders were recorded and the failure modes were monitored during the cycling test. As a result, from the good agreements between the simulations and experiments, it was concluded that at least 70 % of the test pressure should be applied as the autofrettage pressure in order to takes visible effect on the cycling life, and 160 % of the test pressure induces the maximum cycling life and the desired failure mode.
Keywords:
Type3 Cylinder, Autofrettage Pressure, Cycling Life, Failure Mode키워드:
Type3 용기, 자긴압력, 피로수명, 누수형상1. 서 론
공기호흡기에 사용하는 복합재 용기는 금속재 라이너 표면을 에폭시 수지를 함침시킨 탄소섬유로 완전히 덮도록 감아서 만든 압력용기이다. 이는 가벼운 용기 무게와 함께 용기 내부 압력이 올라가면 파열보다 누출이 먼저 발생하는 장점을 가지고 있어 고압가스를 저장하는데 가장 이상적인 저장용기이다. 복합재 용기는 제조공정의 마지막에 라이너 항복강도 이상의 응력 발생을 유도하는 고압의 자긴공정을 거치며, 이때 외부 탄소섬유층의 탄성복원력에 의해 라이너에는 압축잔류응력(compressive residual stress)이 유도된다. 이후 실사용 환경에서의 라이너 응력 수준은 낮아지게 되며, 결과적으로 복합재 용기의 피로수명은 향상된다.
본 연구에서는 상용 공기호흡기 용기의 자긴압력과 피로수명 사이의 상관관계를 정량적으로 산출하기 위해 유한요소해석(FEM)과 수압반복가압시험(hydraulic ambient cycling test, 용기피로시험)을 실시하고, 그 결과를 비교분석하여 피로수명을 향상시키는 최소 자긴압력과 최대 피로수명을 유도하는 최적 자긴압력을 도출하고자 한다.
2. 유한요소해석
2.1 해석기법 및 절차
본 연구에 사용한 공기호흡기용 Type3 복합용기는 알루미늄 라이너(Al6061-T6)에 에폭시 수지에 함침한 탄소섬유(T700급)를 helical 및 hoop 방향으로 번갈아 감아 만들며, 사용압력 30 MPa, 내용적은 6.8 L이다(Fig. 1 참조). 라이너의 두께는 2.41 mm, 복합재층의 두께는 4.60 mm이며, 용기의 외경은 157 mm이다. 용기의 전체적인 형상은 축대칭(axial symmetry)이나 정확한 응력을 계산하기 위해서는 helical winding 층의 축방향 주기성을 반영하여 주기적 축대칭(Δθ=15°)으로 보아야 한다. 응력해석은 한 주기에 대해서만 실시하였다.
유한요소해석에는 ABAQUS를 사용하였으며, 가스와 맞닿는 라이너 부위에 대한 경계조건으로 균일한 압력 조건을 부여하였다. 필라멘트 와인딩 구조의 이방성과 압력용기의 국부 응력분포를 정확히 예측하기 위해 3차원 고체요소 중 직교이방성 강성을 갖는 20절점(node)의 2차 변위 요소를 사용하였다. 알루미늄 재료는 탄성-완전소성을 가정한 구성 방정식을 적용하였다. 용기에 인가하는 자긴압력으로 내압(test pressure)의 100%, 110%, 120%, ..., 290%에 해당하는 압력을 사용하여, 각 경우에 대한 압축잔류응력과 최대변형률(maximum strain distribution)을 산출하였다.
2.2 응력해석 결과
응력해석결과는 자긴압력에 따른 축방향 압축잔류응력 및 최대변형률 변화의 특징을 바탕으로 세가지로 분류하였다. 먼저, 자긴압력이 내압의 100%에서 210%인 구간에서는 압축잔류응력과 최대변형률이 용기의 몸통부위에 집중됨을 알 수 있다(Fig. 2 참조). 자긴압력이 증가함에 따라 압축잔류응력이 집중되고 최대변형률이 발생하는 지점이 용기 몸통부위에서 바깥쪽으로 점점 이동하여 자긴압력이 내압의 220%에서 250%인 구간에서는 돔부위가 응력이 집중되고 변형도 많이 일어나는 것으로 나타났다(Fig. 3 참조). 아울러 260%에서 290% 구간에서는 압축잔류응력과 최대변형률이 용기의 목 부위에 집중됨을 알 수 있다(Fig. 4 참조).
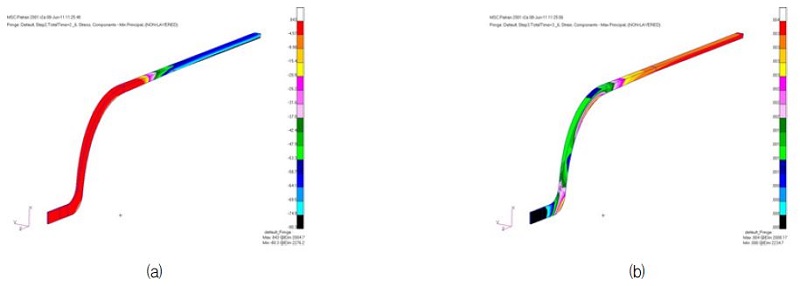
Compression residual stress (a) and maximum strain distribution of liner when 100% of test pressure is applied as the autofrettage process
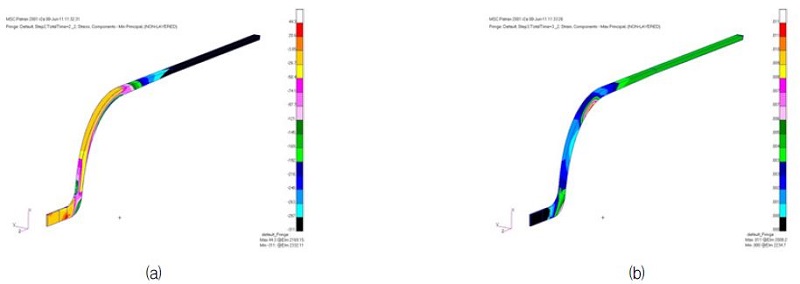
Compression residual stress (a) and maximum strain distribution of liner when 250% of test pressure is applied as the autofrettage process
3. 라이너 시편 인장시험
인가한 자긴압력에서 최대변형률로부터 응력을 도출하고, 최종적으로 피로수명을 예측하는 데에는 재료 인장시험 및 피로시험을 통한 라이너의 응력-변형률(σ-ε) 선도와 변형률 진폭(strain amplitude), S-N 선도가 필요하다. 본 연구에서 수행한 인장시험 및 피로시험에서는 미국 교통국 관련규정인 DOT-CFFC(Basic requirements for fully wrapped carbon-fiber reinforced aluminum lined cylinders)에 명시된 규격에 의하여 시험편을 제작하였고, ASTM-E08에 명시된 절차를 준수하였다. 피로시험에 사용한 응력비는 0.1이며, 시험하중의 최대값은 라이너 재료의 항복강도의 60-95% 사이의 값으로 설정하였다.
변형률 진폭은 용기의 응력해석으로부터 얻은 결과를 다음 수식에 대입하여 구한다.
(1) |
일반적으로 알루미늄에 대한 반복가압횟수(N)와 응력(S)의 관계는 로그-로그 그래프에서 정비례하는 다음의 수식으로 표현된다.
(2) |
인장시험 결과를 선형회귀법을 사용하여 m1=1,262, m2=-0.16임을 산출하였다.
4. 피로수명 예측 결과
응력-변형율 선도를 통해 변환된 응력값을 라이너 재료의 S-N 선도 식 (1)에 대입하여 예측된 피로수명을 도출하였으며, 그 결과를 Fig. 5(자긴압-수명 그래프)에 나타내었다. FE 해석에 의한 수명은 낮은 자긴압에서는 실험값보다 높게 해석되고, 높은 자긴압에서는 반대로 낮게 계산되었으나 오차의 범위는 15% 이내이다. 내압의 100%에서 160%까지 자긴압력의 증분에 따른 피로수명의 변화는 없었으나, 170%부터 피로수명의 증가가 시작되었다. 그리고 내압의 250%까지 자긴압력의 증가에 따라 함께 증가하는 결과를 보였으나, 260% 이상부터는 서서히 감소하기 시작하였다. 예측된 누출부위 역시 100%에서 250%까지의 범위에서는 실린더에서 돔 너클 부위로 변화되었으며, 260 % 이상은 돔 너클에서 보스넥 부위로 변화되었다. 이러한 현상은 자긴압력에 의해 유도된 압축잔류응력이 위치마다 다르게 발생됨에 따른 결과로서, 압축잔류응력은 실린더 부위에서 가장 높으며 돔 너클, 돔 둘레, 보스넥을 따라서 순차적으로 서서히 감소하기 시작한다. 즉, 라이너의 임의의 위치에서의 압축잔류응력은 자긴압력의 증가에 따라 증가한다. 그러나 압축잔류응력의 증가는 라이너의 압축항복강도까지만 발생하며, 항복강도를 넘어선 자긴압력의 증가는 그 위치의 반복수명에 영향을 주지 못하는 것이다.
결과적으로, 내압의 170%에 해당하는 자긴압력은 피로수명을 향상시키는데 필요한 최소 자긴압력이며, 내압의 160%에 해당하는 자긴압력은 실린더 부위에 최대의 잔류응력과 돔 부위에 적절한 잔류응력을 발생시켜, 최대의 피로수명과 돔 너클 부위의 바람직한 파열모드를 유도하는 최적의 자긴압력으로 판명되었다.
5. 복합재 압력용기의 피로시험 결과
본 연구에 사용한 공기호흡기용 Type3 복합용기를 미국 규정인 DOT-CFFC에 명시된 조건에 따라 반복가압시험을 실시하였다. 시험압력은 0∼30 MPa이며, 분당 10회 이하의 주기로 누출이 발생될 때까지 가압-방출을 반복하였다.
자긴압력에 따른 압력용기의 피로시험 결과는 유한요소해석을 통한 압축잔류응력 및 최대변형률 예측결과와 거의 일치하였다. 예를들어, 유한요소해석으로부터 최대변형률이 응집된 것으로 예측한 부위에서 실제 반복가압실험시 누출이 발생하였다(Fig. 6 참조). 이로부터, 유한요소해석을 통해 예측된 내압의 170%에 해당하는 자긴압력은 피로수명을 향상시키는데 필요한 최소 자긴압력이며, 260%에 해당하는 자긴압력은 피로수명을 최대로 만드는 최적의 자긴압력임을 증명하였다.
6. 결 론
본 연구에서는 메탈 라이너를 포함하는 복합재료 압력용기의 자긴압력과 반복수명의 상관관계를 규명하기 위해 유한요소해석과 반복시험을 수행하였으며, 그 결과 내압의 170%의 자긴압력이 피로수명을 향상시키는데 필요한 최소 자긴압력이며, 내압의 260%의 자긴압력이 최대의 반복수명과 안전한 파열모드를 유도하는 최적의 자긴압력으로 판명되었다. 이에 따라, 본 논문에서 제시된 해석 및 시험결과는 향후 일반적인 복합재료 압력용기의 최적의 자긴압력을 설정하기 위한 가이드라인으로서 사용될 수 있을 것이다.
Acknowledgments
본 연구는 국토교통부 플랜트연구개발사업의 연구비지원(15IFIP-B089069-02, 13IFIP-B06700801)에 의해 수행되었습니다.
References
- B. S. Kim, B. H. Kim, J. B. Kim, and C. R. Joe, (1997), “Study on the developing of composite CNG pressure vessels”, ICCM-11, Int’l Conf. on Composite Materials, Gold Coast, Australia, p401-418.
- Rosata, D. V., and Grove, C. S., (1984), “Filament winding: its development, manufacture, application, and design”, Interscience Publishers.
- James, D. E., and James, A. Y., (1987), “Graphite epoxy pressure vessel dome reinforcement study”, 32nd International SAMPE Symposium.
-
Sun, X. K., Du, S. Y., and Wang, G. D., (1999), “Bursting problem of filament wound composite pressure vessels”, International Journal of Pressure Vessels and Piping, 76, p55-59.
[https://doi.org/10.1016/S0308-0161(98)00096-9]
-
Mohammad, Z. K., (2000), “Finite element analysis of composite pressure vessels with a load sharing metallic liner,” , Composite Structure, 49, p247-255.
[https://doi.org/10.1016/S0263-8223(99)00044-6]
- Kwang, T. K., Jung, S. K., Doh, Y. D., Cho, W. M., and Jung, B., (2000), “The Performance Improvement of Filament Wound Composite Pressure Vessels”, SAMPE, p1427-1438.
- Park, J. S., Jeung, S. S., and Chung, J. H., (2006), “Cycling life prediction method considering compressive residual stress on liner for the filament-wound composite cylinders with metal liner”, The Korean Society for Composite Materials, 19(1), p22-28.